Os indicadores são uma das principais formas de se medir os resultados em manutenção. Afinal, o que não se mede não se gerencia.
Eles são muito importantes para os gestores de manutenção, já que a rotina de trabalho, equipes, processos e equipamentos podem ser analisados com a ajuda dos indicadores. Mas será que seus equipamentos e suas operações conseguem dar conta dessas análises?
Basicamente, é possível mensurar qualquer atividade que gere números ou valores em manutenção. A questão é descobrir quais são os indicadores de desempenho mais importantes, assim não perdemos tempo acompanhando os menos relevantes. Pensando nisso, a TRACTIAN selecionou os 8 principais indicadores:
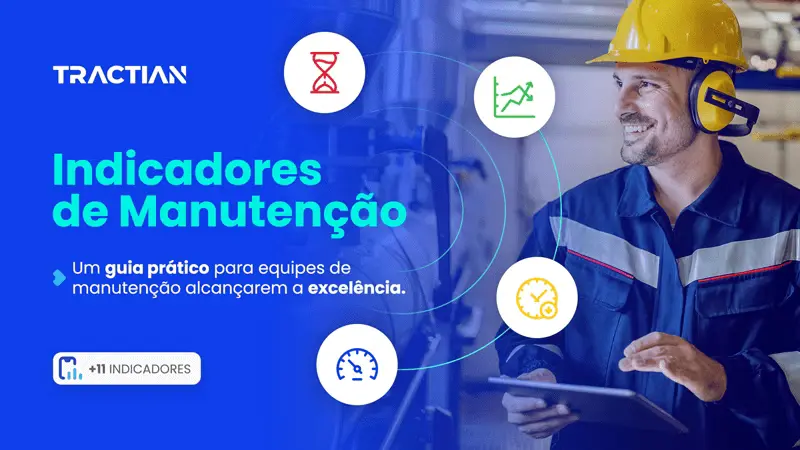
MTBF, MTTR e outros indicadores de manutenção indispensáveis:
- MTBF: Tempo médio entre falhas;
- MTTR: Tempo médio para reparo;
- Disponibilidade;
- Confiabilidade;
- Backlog;
- CMF: Custo de Manutenção sobre Faturamento;
- CPMV: Custo de manutenção sobre valor de reposição;
- Distribuição por tipos de manutenção.
MTBF e MTTR: como analisar esses indicadores de manutenção?
A seguir, saiba mais sobre as funções de cada um, suas diferenças e por que são indispensáveis. Boa leitura!
1. MTBF: Mean Time Between Failures
O MTBF ou tempo médio entre falhas é um dos indicadores mais importantes para o setor de manutenção. Ele é necessário para medir o tempo total de bom funcionamento médio entre as falhas de um equipamento reparável, sendo uma ótima forma de mensurar a confiabilidade da máquina.

Conheça o melhor EAM/CMMS do mercado, com maior custo-benefício!
A maneira mais eficiente de administrar esse indicador é aplicando-o em cada equipamento. Essa aplicação individual das ações facilita o processo, já que considera os diferentes ciclos de vida dos equipamentos.
Para exemplificar, imagine que durante um determinado período o motor elétrico de uma fábrica operou 140 horas até falhar, depois mais 190 horas e, por fim, outras 215 horas. Nesse caso, o MTBF será:

Uma vez identificado o tempo médio de uma falha a outra, conseguimos definir a frequência com que devemos realizar nossas atividades de manutenção preventiva e inspeções dentro do PCM (Planejamento e Controle de Manutenção).
O recomendado é calcular 70% do tempo médio de falhas para realizar essa inspeção. Ou seja, se o motor elétrico apresenta um MTBF de 181,6 horas, a cada 127,1 horas (181,6 x 0,7) deve-se realizar a inspeção no equipamento.
Logicamente, quanto maior o MTBF, melhor, já que os equipamentos estão demorando mais para falharem, ou seja, você alcançou uma frequência menor de quebras.
Principais erros cometidos no cálculo do MTBF
- Somar o MTBF de todos os equipamentos para encontrar a média global;
- Calcular o MTBF em equipamentos irreparáveis;
- Zerar o MTBF a cada mês (é preciso somá-lo).
Atualmente, existem alguns softwares de manutenção preditiva que conseguem, através da análise de vibração e temperatura dos equipamentos, estimar quando acontecerá a próxima quebra e criar automaticamente ordens de serviço para resolver o problema. Dessa forma, a análise deixa de ser manual e em planilhas e passa ser online e em tempo real. Isso aumenta consideravelmente a acurácia dos
2. MTTR: Mean Time To Repair
Esse indicador está muito associado à mantenabilidade, ou seja, a facilidade que uma equipe de manutenção encontra em fazer um equipamento voltar a executar suas funções após uma falha. Em outras palavras, o MTTR indica o tempo médio para reparo.

Ao contrário do MTBF, quanto menor o MTTR, melhor, portanto devemos trabalhar para mantê-lo baixo.
Adicionando-o ao exemplo do motor elétrico, suponha que, durante o mesmo período, a equipe de manutenção levou as quantidades de horas listadas abaixo para colocar o motor elétrico de volta à operação após cada uma das falhas:
- Falha 1: 9 horas de reparo
- Falha 2: 15 horas de reparo
- Falha 3: 12 horas de reparo
Nesse caso, o MTTR será:

Descubra o poder da análise preventiva para suas máquinas!
Com isso, conseguimos mensurar qual é o lucro cessante — o quanto a empresa deixa de ganhar quando esse ativo quebra. Se considerarmos que tal máquina gera R$ 5.000 por hora, o prejuízo da empresa com a falha dela ficará por volta de R$ 60 mil (5.000 x 12).
Principal erro cometido no cálculo do MTTR
- Estabelecer um referencial para o MTTR. Isso não existe e, ao exigir que as equipes de manutenção mantenham um valor ideal baixo de MTTR, a chance é grande de induzi-las ao erro.
Muito melhor do que manter o MTTR baixo é evitar as quebras. O gestor de manutenção deve incentivar suas equipes a utilizar técnicas de manutenção preditiva e sensitiva que avaliam a condição de saúde das máquinas, identificando os “sintomas” em tempo real para que o ativo não perca sua performance a ponto de chegar em uma situação crítica de quebra.
3. Disponibilidade
Diferença entre disponibilidade e confiabilidade
Disponibilidade refere-se à capacidade de um item de estar em condições de executar uma certa função em um dado instante ou durante um intervalo de tempo determinado.
Confiabilidade é a probabilidade de um item desempenhar sua função especificada no projeto de acordo com as condições de operação e durante um intervalo específico de tempo.
O significado é parecido, não? Para que as diferenças fiquem claras, vamos exemplificar.
A disponibilidade de um equipamento é a porcentagem no qual esse ativo se manteve disponível em um determinado período. Já a confiabilidade será a probabilidade de um equipamento se manter disponível em um período futuro.
Prefere as fórmulas? Confira:
Esses dois indicadores são fundamentais para o Planejamento e Controle da Manutenção, já que o objetivo principal do PCM é garantir e elevar a disponibilidade e confiabilidade dos ativos, otimizando a produtividade da indústria. Por isso resolvemos colocá-los juntos.
Ambos são determinados a partir do MTBF e do MTTR. Mas, antes de calculá-los, vamos entender o significado de cada um segundo a norma NBR 5462.

Ou seja, se usarmos o exemplo do motor elétrico (MTBF = 181,6 e MTTR = 12), a disponibilidade inerente do equipamento foi de 93,8%. Isso quer dizer que, naquele período, o motor operou normalmente cerca de 93,8% do tempo em que ficou ligado. Padrões de classe mundial determinam que uma boa disponibilidade é aquela acima de 90%. Portanto, o equipamento está dentro dos padrões globais.
4. Confiabilidade
E se quiséssemos calcular a probabilidade de o motor funcionar em perfeito estado durante a próxima semana? Nesse caso, usamos o cálculo da confiabilidade:

Se aplicarmos a fórmula para o motor elétrico (MTBF = 181,6), conseguimos saber que, para os próximos 7 dias (168 horas), a confiabilidade desse equipamento — isto é, a probabilidade de ele operar normalmente sem falhar— será de 39,69%. Veja abaixo:

Principal erro cometido no cálculo da confiabilidade
- Indicar a confiabilidade sem atrelá-la a um período de tempo.
ERRADO: A confiabilidade dessa centrífuga é de 85,4% – qual é o período?
CERTO: A confiabilidade dessa centrífuga é de 85,4% nas próximas 400 horas.
- Usar a fórmula para equipamentos irreparáveis. Para tais itens, deve-se utilizar a Análise Weibull.
5. Backlog
O backlog pode ser entendido como o tempo de mão de obra necessário para realizar todos os serviços atuais, ou seja, o acúmulo de atividades pendentes. Logo, tal indicador demonstra a relação entre a demanda de serviços e a capacidade de atendê-los.
Podemos entender o backlog como uma carteira de serviço oriunda das atividades de manutenção. Em outras palavras, é a soma da carga horária dos serviços planejados, programados, executados e pendentes do setor.
Por ser um indicador de tempo, deve ser calculado em minutos, horas, dias, semanas, meses, etc. Confira a fórmula:
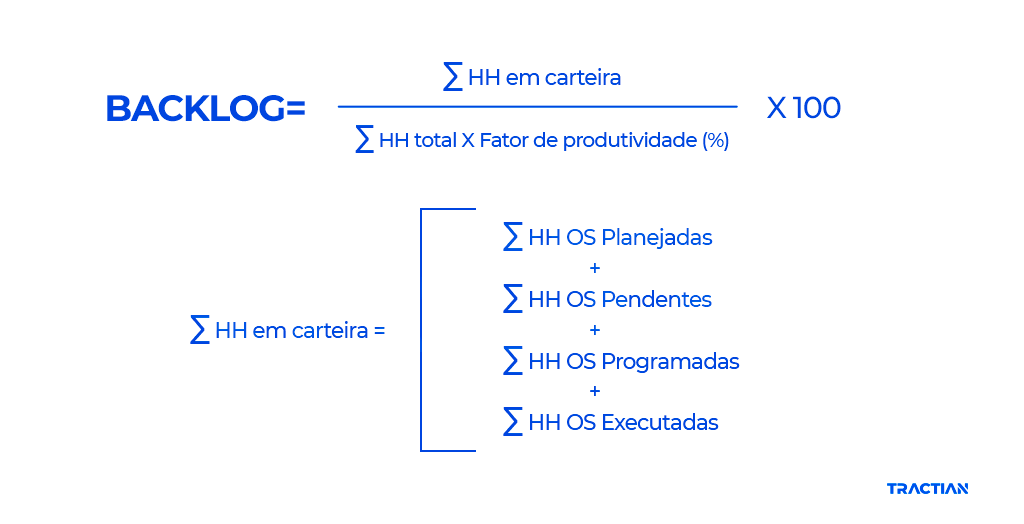
O gráfico de backlog também é de grande importância para decisões gerenciais. Ao todo, há basicamente seis tipos de curvas. Considere o eixo vertical como sendo valores de backlog e o eixo horizontal como os meses do ano:

- Curva A: estável. Exige análise para checar se está em um valor aceitável para a tomada de decisão;
- Curva B: decréscimo da demanda de serviço. Pode gerar pessoal ocioso devido à queda de atividades;
- Curva C: backlog com tendência de alta constante, o que pode gerar problemas como baixa qualidade da manutenção;
- Curva D: subida brusca. Pode ocorrer quando há corretivas com tempo de execução muito alto;
- Curva E: queda brusca. Nesse caso, pode ter ocorrido contração de serviços externos, mobilização interna para redução, entre outros;
- Curva F: Oscilação. Costuma ser justificável em indústrias que tenham forte característica de sazonalidade, como por exemplo ligadas a agricultura.
Principal erro cometido:
- Associar o backlog a “atividades em atraso”. Esse é um erro comum quando utilizamos o indicador, por isso, é importante lembrar que ele engloba muito mais do que os atrasos e se refere a todas as atividades que precisam ser feitas, desde as urgentes até as cotidianas.
6. CMF: Custo de Manutenção sobre Faturamento
Indicadores ligados aos custos são excelentes evidenciadores do efeito da manutenção no desempenho da empresa, o que os tornam uma arma feroz para a diretoria. Com eles, é possível identificar se o setor de manutenção está fazendo uma boa administração financeira dos recursos.
O custo de manutenção engloba todas as despesas com:
- Pessoal;
- Materiais;
- Contratação de serviços externos;
- Depreciação;
- Perda de faturamento.
Um dos grandes motivos desse destaque é que o custo da manutenção pode impactar diretamente na precificação do produto. Logo, se a empresa gasta muito com manutenção, o preço do produto será mais alto e ela perderá competitividade em comparação com seus concorrentes.
O indicador que melhor trabalha com esse cenário é o CMF, justamente por ser uma comparação direta entre o faturamento e o custo da manutenção. Observe a fórmula:

Imagine que uma determinada indústria têxtil teve um gasto total de R$1 milhão com manutenção no último ano. No mesmo período, o faturamento bruto da empresa foi de R$25 milhões. Portanto, o CMF é de 4%. Mas como saber se isso é bom ou ruim?
Depois de calculado, o melhor a se fazer é compará-lo com a média do segmento em que sua empresa atua. Nesse caso, a média do CMF para a indústria têxtil é de 1%, o que indica que a empresa analisada no exemplo gastou 4 vezes mais do que a média do segmento. No entanto, a mesma empresa está na média das brasileiras em geral, já que, segundo a ABRAMAN, em média 4% do faturamento das empresas no Brasil é empregado em manutenção.
7. CPMV: Custo de manutenção sobre valor de reposição
Outro indicador financeiro importante é o CPMV, porque é uma maneira de analisar o custo de manutenção empregado em cada equipamento e identificar se seria mais vantajoso manter o ativo ou comprar um novo. A recomendação é que esse indicador seja utilizado para equipamentos de alta criticidade
O cálculo é simples, mas antes vamos entender o que é a sigla ERV (Estimated Replace Value). O Valor Estimado de Troca, como o próprio nome já entrega, é a quantidade de capital que será preciso investir para comprar um novo equipamento. Assim, a fórmula do CPMV é a seguinte:

Para exemplificar, pense que foram gastos R$4.000 com a manutenção de uma ponte rolante, enquanto o valor de uma nova seria R$190.000. Logo, o CPMV é de 2,1%.
O valor máximo aceitável para esse indicador é 6% num período de um ano. No entanto, o limite pode depender da análise do equipamento — em alguns casos, 2.5% já é o bastante. Se encontrarmos um número maior, significa que será mais vantajoso comprar um novo equipamento do que continuar mantendo o antigo.
Uma forma mais eficaz de reduzir os gastos com manutenção é mudar a dinâmica do “quebra, conserta”, ou seja, tentar reduzir ao máximo o número de manutenções corretivas e usar o poder dos dados para prever as falhas antes que elas aconteçam. Isso porque o gasto para manter um plano de manutenção preditiva é infinitamente menor do que o custo para reparar o equipamento e colocá-lo de volta em funcionamento.
8. Distribuição por tipos de manutenção
Esse indicador revela o percentual da aplicação de cada tipo de manutenção que está sendo desenvolvido.
Evidentemente, o tipo de instalação ou equipamento pode determinar variações desses valores para mais ou menos. De modo geral, o gestor de manutenção deve manter as práticas corretivas não planejadas em até 20%, sendo sempre bom restringi-las ao máximo. As outras práticas não possuem um limite próximo: no Brasil, a manutenção preventiva costuma oscilar entre 30% e 40%. Em padrões de confiabilidade global, as empresas sempre mantêm a manutenção preditiva com a maior porcentagem na distribuição.

Como a tecnologia pode ajudar sua empresa no acompanhamento dos indicadores?
A tecnologia, como softwares de gestão da manutenção e dispositivos de monitoramento da condição do maquinário, tem revolucionado a rotina de manutenção, substituindo as planilhas extensas, auxiliando na coleta e gerenciamento de dados dos indicadores, tornando as informações mais confiáveis e entregando insights valiosos sobre confiabilidade e disponibilidade dos ativos em tempo real.
Quer saber mais sobre como a TRACTIAN está tornando a rotina de gestores de manutenção mais prática e intuitiva? Agende uma demo gratuita!