Se habla mucho de la especialización en el área del mantenimiento, pero muchas veces nos encontramos con conceptos sencillos que debemos tener bien claros. Hoy te presentaremos las diferencias entre el mantenimiento correctivo, el mantenimiento preventivo y el mantenimiento predictivo.
La 4ª Revolución Industrial está marcada por la alta adopción de tecnologías, emergiendo la necesidad de invertir en profesionales de ciencia de datos y startups de inteligencia artificial, con el objetivo de facilitar las operaciones en el sector del mantenimiento. Como es bien sabido, un fallo en los equipos hoy equivale a millones en pérdidas.
La Industria 4.0 también está relacionada con el uso de sensores en los activos, para que estos se vuelvan más inteligentes, y con ello sea posible extraer datos cada vez más precisos sobre los activos, en tiempo real. Exactamente es lo que compañías como TRACTIAN están brindando a las empresas, haciendo que el mantenimiento de rutina sea más simple, efectivo e intuitivo.
Los datos recopilados por la plataforma ayudan, principalmente, en el tema del mantenimiento de los equipos. Y muestran dónde y cuándo se debe realizar una reparación, o qué máquina es susceptible de fallos inesperados.
La práctica del mantenimiento proporciona dos contrapuntos. El primero es anticiparse a los problemas más frecuentes, adoptando el mantenimiento periódico como forma de evitar paradas no planificadas, generando mayor eficiencia. El segundo es que si no se prevé, se corre el riesgo de parar toda la continuidad de los activos y la pérdida sería enorme.

Mantenimiento preventivo
El mantenimiento preventivo es fundamental para garantizar la eficiencia y confiabilidad en las operaciones industriales, evitando el desgaste y los posibles fallos de los activos. Significa planificar una acción para revisar, controlar y monitorizar los equipos, para que puedan desempeñar el papel deseado.
De acuerdo con la norma 5462 de ABNT, el mantenimiento preventivo tiene como objetivo reducir las probabilidades de fallos o degradaciones, que surgen de la operación incorrecta o intensiva de una máquina. Las ventajas de este tipo de mantenimiento incluyen: Optimización de los recursos, aumento de la vida útil de estos activos, mejor calidad de operación y prevención de accidentes.
Como ejemplos de mantenimiento preventivo podemos tener: Inspecciones periódicas de vehículos y máquinas, lubricación de rutina, inspecciones y revisiones de equipos y calibración de instrumentos.
Para realizar este método necesitas:
- Recoger datos de los equipos;
- Analizar el historial de acciones realizadas sobre los activos;
- Hacer un plan de acción;
- Definir un plan operativo, qué acciones se tomarán en cada caso.
Descarga ebook: Tipos de MantenimientoLa guía completa para especialistas de la industria.¿Cuáles son los tipos de mantenimiento?¿Cuándo y cómo debo aplicarlos?Aprender los pasos de cada unoDescarga Ebook
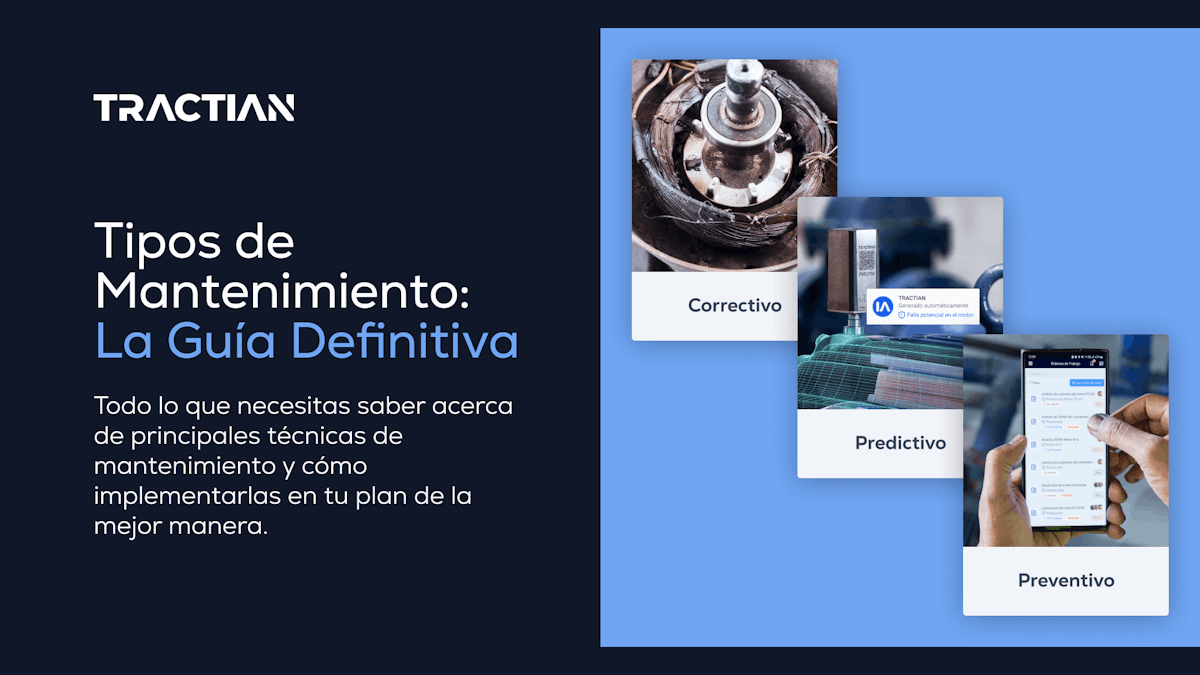
Mantenimiento Predictivo
Podemos catalogarlo como una monitorización de rutina, ya que se basa en las condiciones reales en las que se encuentra el activo, con el objetivo de reducir la probabilidad de fallos, desgaste y daños en los equipos. Las irregularidades generadas pueden evolucionar hacia fallos mayores, lo que perjudicaría la producción y podría llevar a la empresa a grandes pérdidas.
Este tipo de mantenimiento permite un diagnóstico precoz, permitiendo que acciones adecuadas sean realizadas para impedir que un equipo se detenga. Esta estrategia de mantenimiento predictivo se puede ejecutar basándose en la información recogida, por medio de la termografía, ultrasonido, análisis de aceite, vibración y temperatura. Ella determina de manera anticipada, la necesidad de revisión de la máquina. Elimina desmontar innecesariamente un activo, aumenta la durabilidad de los equipos, reduce el trabajo no planificado e impide que los daños aumenten.
Por ejemplo, imagine la facilidad de pegar un dispositivo similar a una “curita, tirita o apósito” en el equipo de su empresa. Un mecanismo que, a través de sensores inteligentes, puede medir la temperatura y vibración del equipo, detectando posibles anomalías y monitorizando la vida útil y la salud del activo. La constante monitorización durante la producción brinda mayor confiabilidad a los equipos. Todo esto es enviado a una plataforma en manos de ingenieros y supervisores, quienes son capaces de tomar decisiones más rápidas y eficientes, evitando fallas y cuellos de botella en la línea de producción.
Implementa Mantenimiento Predictivo con el Sensor de Vibración Líder
Este seguimiento es fundamental para agilizar y optimizar el proceso productivo, en base a los datos que proporciona nuestra plataforma.
Para realizar este método es necesario:
- Hacer un plan para evaluar qué estrategias y técnicas se utilizarán;
- Recopilar datos, almacenarlos y analizarlos para la evaluación del desempeño;
- Verificar continuamente las máquinas y ver si hay cambios en las características;
- Comparar los datos iniciales con los recopilados;
- Realizar mantenimiento predictivo.
Consulta nuestra guía de mantenimiento predictivo.
Mantenimiento Correctivo
El mantenimiento correctivo fue pionero después de la Segunda Guerra Mundial, y se utiliza para corregir fallos, averías o roturas en los equipos. Su finalidad es restaurar las condiciones originales de los activos, dejándolos listos para funcionar nuevamente.
Este mantenimiento no está programado ya que se realiza después de que se averíe un activo. Además de tener un impacto financiero mayor que otros, ocurre cuando un determinado equipo o parte ya está funcionando mal y necesita ser reemplazado.
Hay pérdidas altas con el mantenimiento correctivo, por ejemplo: retrasos en la producción, actividades no planificadas que se realizan, falta de stock de repuestos, además de parar toda la producción.
Esta gestión se divide en dos tipos:
Mantenimiento correctivo planificado
Se lleva a cabo cuando se identifica el problema del equipo, antes de que deje de funcionar por completo. Sin embargo, la reparación está programada, pero mientras el activo no está reparado, funciona con bajo rendimiento.
Mantenimiento correctivo no planificado
Es el más clásico. Ocurre cuando el equipo deja de funcionar por completo, resultando en una parada inmediata, requiriendo un mantenimiento urgente. Proviene de algún síntoma de fallo que se observó a través del mantenimiento predictivo, debido a la falta de monitorización del desempeño de los activos, lo que genera numerosas pérdidas en la producción.
Ten un mantenimiento de clase mundial en tu empresa con tecnología 4.0 e inteligencia artificial.