Industry 4.0, also known as the Fourth Industrial Revolution, is transforming manufacturing processes, especially the maintenance sector. It has been revolutionizing production chains around the world through new technologies.
In the context of Industry 4.0, industrial maintenance management has become even more crucial. The convergence of advanced technologies, such as artificial intelligence (AI), big data, and automation, has transformed the way companies approach the maintenance of their assets.
In this article, we’ll discuss how Industry 4.0 is revolutionizing industrial maintenance. First, we’ll explore the main tools and technologies that are being used to improve maintenance processes. We’ll also cover how the adoption of management software can help to optimize these processes, increase efficiency, and generate a return on investment (ROI).
The Pillars of Industry 4.0
This significant change in the way we view technology, particularly as it applies to maintenance, is based on seven pillars:
Robotics: Robots are increasingly able to operate autonomously, and can already interact with each other, assist humans, and modify their behavior based on data.
Simulation: Simulations using digital models, such as augmented reality (AR) and plant visualization, can be used in product development, production process improvement, and better monitoring of teams on the shop floor. This type of technology provides better control, predictability, and visualization of information.
Big Data and Analytics: The amount of data generated by industrial machines and equipment has increased exponentially with the advancement of technology. All Big Data is, is the ability to collect, store, and analyze large datasets. The data collected can be used to extract information, identify patterns and trends, predict failures, and improve decision-making in industrial maintenance.
Systems Integration: Currently, not all information systems are integrated. Companies, projects, suppliers, and customers aren’t well-connected, which makes many processes slow and bureaucratic. Industry 4.0 proposes an integration of processes, making the chain automated.
Integrating various computer systems and software applications, either physically or digitally, to work together as a unified system facilitates the exchange of information between them. This integration provides companies with a holistic view of their business operations.
By having access to real-time information about the production process, managers can make quicker decisions, and strategic choices can be easily implemented in the production plant. It’s important to note that installing ERP packages alone isn’t enough: integrating them with industrial production control systems is necessary.
Internet of Things (IoT): This consists of a system that connects various devices, allowing them to collect, transmit, and share data. This data can be used for automating tasks, remotely monitoring equipment, and making informed decisions.
In the context of maintenance, IoT is used to monitor metrics such as vibration, temperature, hour meter, and energy consumption. By collecting and analyzing this data, it becomes possible to predict when an asset is likely to fail, enabling preventive maintenance to be scheduled.
Additive Manufacturing: Also called 3D printing, it has been increasingly used for prototyping and production. This technology comes with the advantage of high performance in producing small batches of customized products.
Cloud Technology: This technology allows users to access information remotely, without having to take up space on company servers. This can save businesses time and money, as well as improve the efficiency of entire teams. Additionally, cloud technology is an essential tool for large storage and integration between traditional software and enterprise resource planning (ERP) systems.
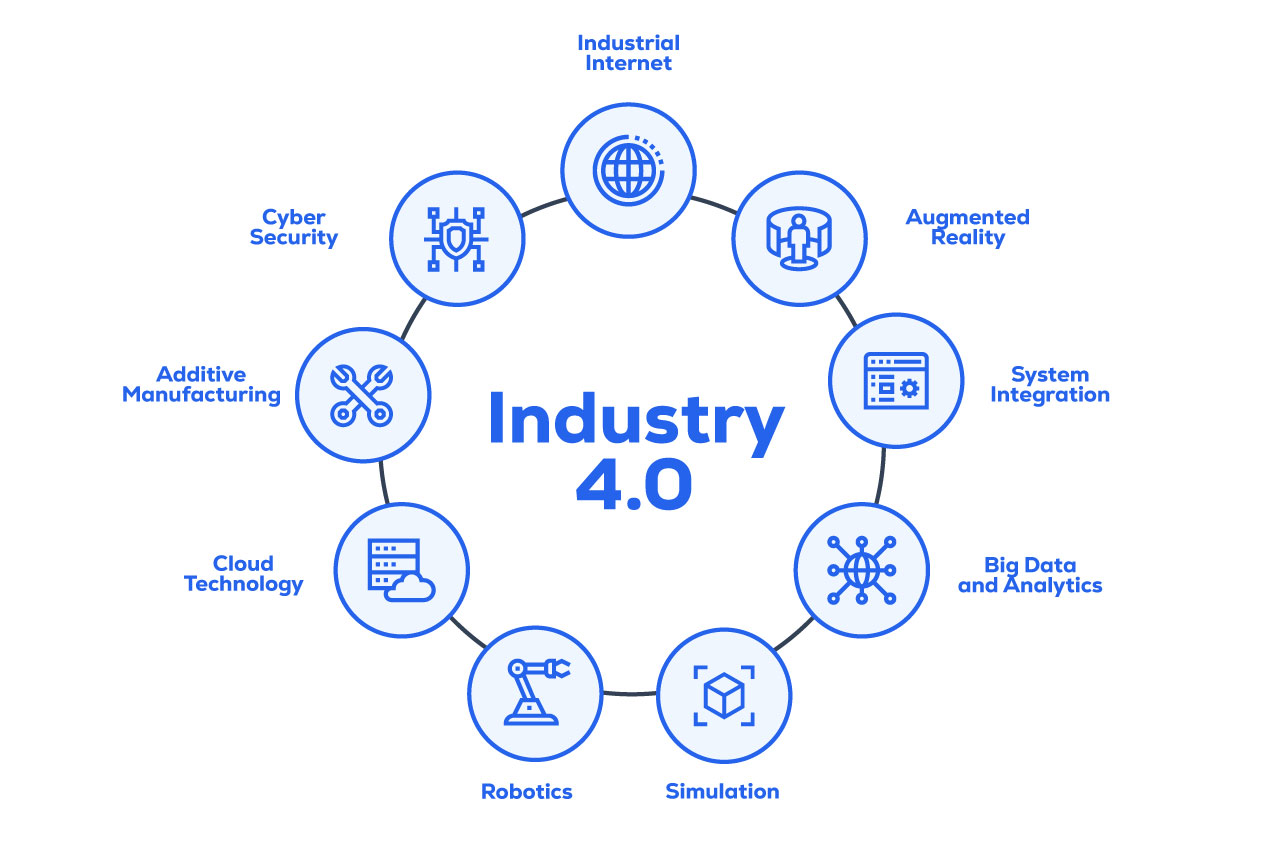
Management in Industry 4.0
Industries are constantly seeking to modernize and improve management strategies, with the aim of increasing productivity and reducing costs. Maintenance is one of the sectors that directly impact these results.
Managing physical assets has become easier since Industry 4.0. Maintenance teams can now manage an asset’s life cycle from start to finish through computer software – this optimization avoids equipment unavailability and unplanned downtime.
This revolutionary approach replaces dated maintenance paradigms. Reactive maintenance is now substituted by planned preventive maintenance, made easier by adoption of cloud-based platforms.
Besides, Industry 4.0 has introduced innovative technologies, with AI standing out as a powerful ally in industrial maintenance management. By analyzing large amounts of data and identifying patterns, AI enables a proactive approach and informed decision making.
When integrated into management, AI becomes a differentiator, making companies more likely to improve production quality, achieve significant results and stand out from the competition.
Industry 4.0 and Its Impact on Maintenance Processes
One of the most promising applications of Industry 4.0 and artificial intelligence is the generation of intelligent maintenance planning. By analyzing historical maintenance data, AI can identify trends and correlations that can be used to predict when an asset is likely to fail.
In the Fourth Industrial Revolution, asset management gains even more importance. The interconnection of systems and automation allow real-time data collection on asset performance, providing improvements in efficiency and productivity for companies.
Manually managing all assets is unfeasible, so it is essential to have asset management software that automates the entire process and connects with the various manufacturing facilities.
Integrating plants with an intelligent asset management system brings several benefits, such as:
- Reduction of unplanned downtime
- Reduction of inventory costs
- Minimization of production interruptions
- Reduction of equipment failures
- Increased plant availability
- Increased maintenance efficiency
- Improved equipment productivity
A practical example of the application of Industry 4.0 and management software is the generation of smart and automatic work orders.
When planning your preventive orders, you can distribute the activities among the technicians or teams responsible, establishing the hours available for each one to perform the assigned operations. This is very similar to what is done in SAP when scheduling Maintenance Orders.
You select as many performers as needed for each operation, and enter the start date and time of the activities to be carried out.
Repetitive tasks such as data recording and issuing work orders can be automated, avoiding manual data imputation.
This allows the maintenance team to direct their time and effort to strategic and complex activities, improving overall efficiency.
Now, with smart planning, it is possible to optimize maintenance activities, resulting in a more efficient allocation of resources, reduction of operational costs and minimization of unplanned downtime.
Dashboard Generation
Another advantage offered by AI in industrial maintenance management is the generation of advanced dashboards and reports. By analyzing data collected in real time, AI can provide valuable information in a visually appealing and easy-to-understand format.
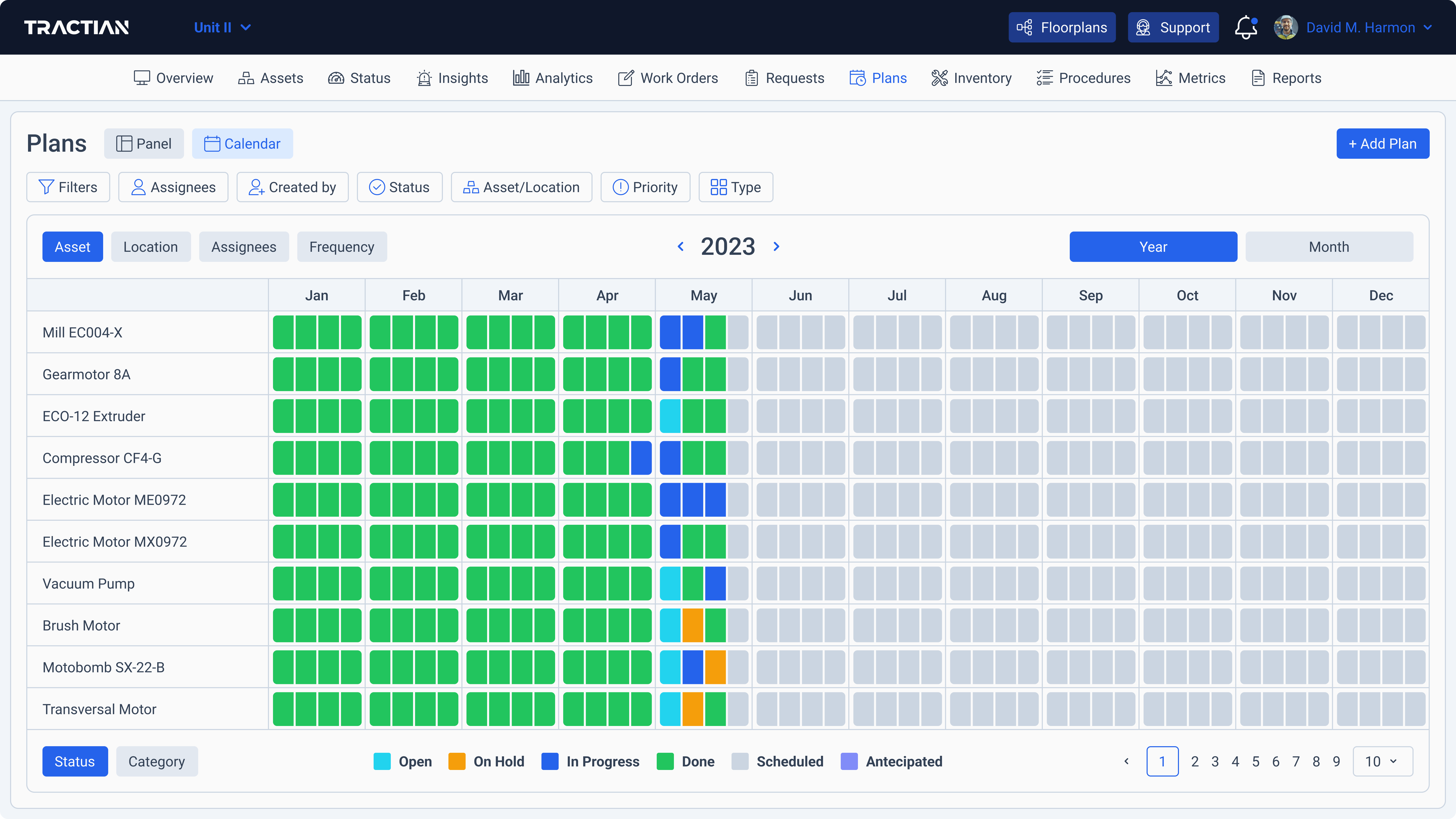
These dashboards provide maintenance managers with a comprehensive view of equipment performance, key metrics and efficiency KPIs. This allows them to make data-driven decisions, identify trends, detect problems and make necessary adjustments to optimize the operation.
Return on Investment
All these benefits culminate in an amazing return on investment, including the best fiscal budget planning in the industry.
Optimizing planning, automating routines and generating advanced reports contribute to reducing operating costs, minimizing unscheduled downtime and increasing the efficiency of maintenance staff.
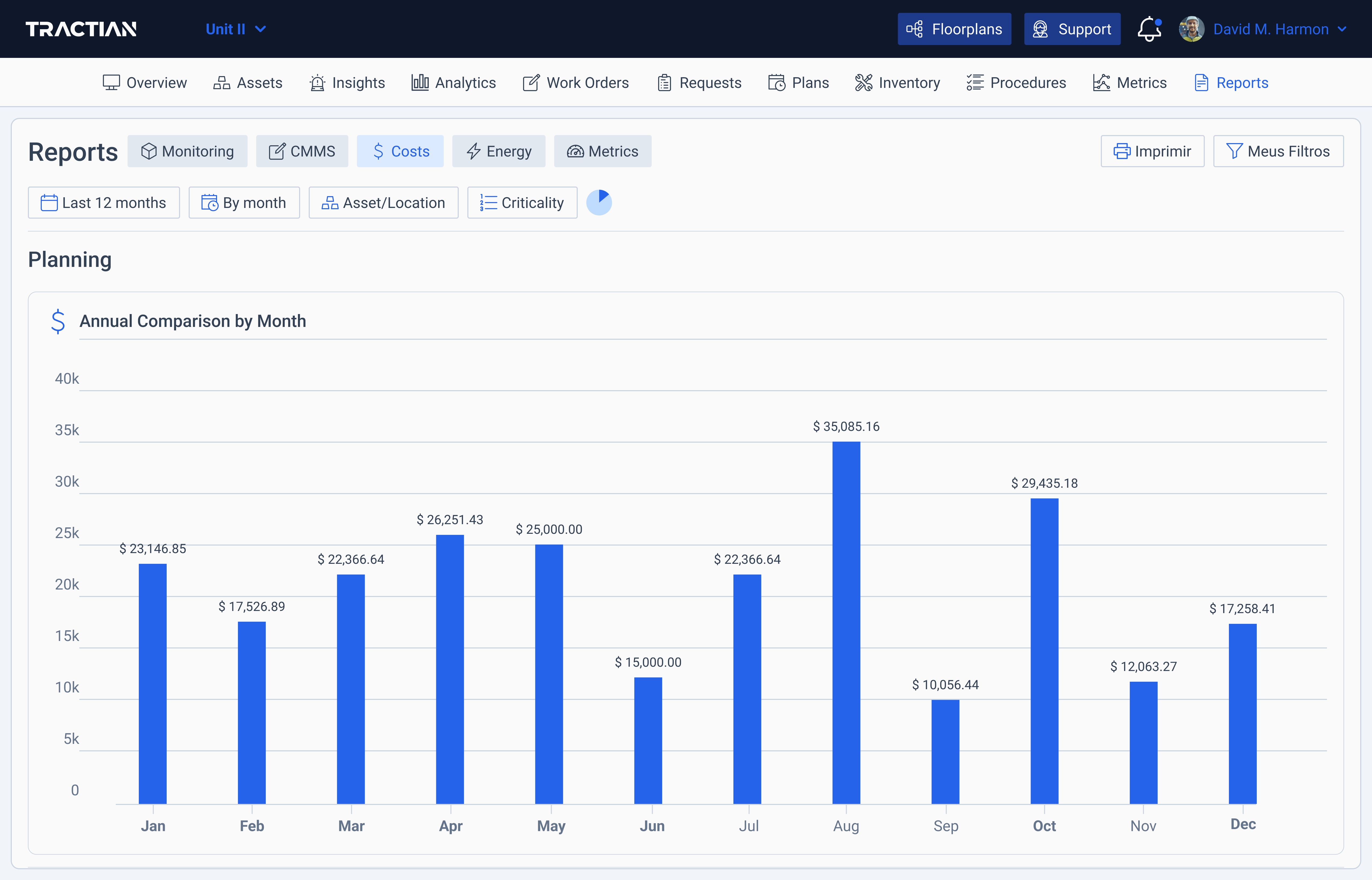
By doing so, companies can achieve higher equipment availability, improved operational reliability and stronger financial results.
Maintenance Indicators and Asset Lifespan
By combining the technical knowledge of maintenance staff with new technologies, it’s possible to achieve a significant improvement in the efficiency and effectiveness of industrial maintenance management.
The application of artificial intelligence, big data, and asset management can extend the life of machines, reduce unscheduled downtime and failures, and improve performance indicators such as mean time between failures (MTBF) and mean time to repair (MTTR).
Integration with ERPs
An important pillar of Industry 4.0 is the integration of maintenance management software with traditional ERPs, such as SAP, ORACLE, NetSuite, and Sankhya. The integration automates the exchange of information between systems, eliminating the need for manual data entry.
This means that maintenance-related data such as work orders, activity records, parts inventory, and costs are synchronized and taken in real time. This ensures that the information is consistent and accurate across the industry.
The integration of maintenance management software and traditional ERPs can optimize workflow, reduce errors, and streamline decision-making, promoting efficient and integrated management in Industry 4.0.
Impacts on Routine Maintenance
The application of advanced technologies, such as artificial intelligence, can enable intelligent planning, automated routines, and the generation of dashboards and advanced reports.
A maintenance management software better organizes internal processes, ensures complete control and oversight of the shop floor, increasing the availability and reliability of plant assets.
These processes, which were once manual and time-consuming, can now be automated and completed in a shorter amount of time.
In addition to the impacts already mentioned, maintenance teams can achieve other levels of productivity. These benefits can be thought of in a more tangible way, such as a more efficient allocation of resources, reduced operating costs, increased equipment availability, and an overall improvement in maintenance performance.
Therefore, industrial maintenance managers should adopt management software to improve efficiency and achieve a solid return on investment.
Use AI to your advantage and take action with precision and efficiency.