Análise de falhas é um processo que consiste em analisar a ocorrência de um determinado problema, seu grau de severidade e encontrar a sua causa raiz dessa falha. Essa análise pode ser realizada de diversas formas, e cada método terá uma melhor funcionalidade conforme a situação.
Portanto, o profissional deve saber como selecionar essas ferramentas e como combiná-las para chegar em uma conclusão e propor uma solução com maior eficiência e menor custo.
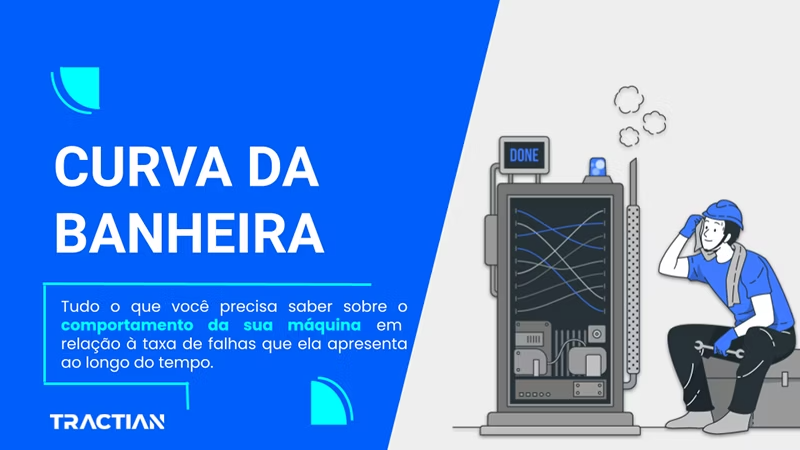
Você sabe identificar e analisar de forma correta as falhas dos ativos de sua empresa? Se você procura soluções que buscam te ajudar a analisar essas falhas, nós iremos te ajudar com as 5 principais ferramentas e métodos.
Sendo assim, vamos entender sobre 5 principais ferramentas e métodos que são fundamentais para essa análise de falhas.
1. Análise: os 5 porquês
Falhas inesperadas acontecem por diversas causas — raramente um mesmo motivo gera diferentes erros. No entanto, quando acontece uma falha sempre nos perguntamos: “Por que isso aconteceu?”
A metodologia dos Porquês consiste em uma série de perguntas que contribuem com um entendimento da causa raiz do problema. A resposta da primeira pergunta gera uma segunda pergunta, que terá uma resposta e gerará a terceira pergunta. Esse é o sistema principal da metodologia.
Com uma média de 5 perguntas, é possível encontrar o início do problema. No entanto, é importante que continue perguntando “por quê” até descobrir uma causa raiz plausível para a falha em questão.
Utilizaremos uma situação básica de um motor industrial queimado, por exemplo. A pergunta fundamental é: por que esse motor queimou? Essa pergunta dará início aos questionamentos que permitirão encontrar a causa raiz do problema. Veja a sequência da metodologia:
Resposta da pergunta fundamental: O motor teve o eixo de rotação bloqueado.
Pergunta 1: Por que o motor teve o eixo de rotação bloqueado?
Resposta da pergunta 1: Tinha sedimento no vão do motor que impedia a rotação do eixo.
Pergunta 2: Por que o sedimento que impedia a rotação do eixo do motor estava ali?
Resposta da pergunta 2: A deterioração da estrutura em que se encontrava o motor possibilitou a deposição deste sedimento no vão do eixo de giro.
Pergunta 3: Por que a estrutura estava se deteriorando?
Resposta da pergunta 3: A estrutura está se deteriorando pela falta de orçamento para manutenção de tal aspecto.
Pergunta 4: Por que falta orçamento para o aspecto estrutural?
Resposta da pergunta 4: Falta orçamento porque a equipe de manutenção fez um plano de orçamento que voltasse pouca parte do financeiro para os aspectos estruturais.
Causa Raiz: O plano de manutenção mal feito direcionou baixo orçamento para os aspectos estruturais, permitindo a deterioração dos mesmos e causando bloqueios na funcionalidade do motor.
No exemplo, foi possível encontrar a causa raiz na quarta pergunta, o fundamental é aprofundar as situações e os motivos gerais para entender a real causa.
Quando se trata de análise de falhas de componentes (rolamentos, retentores, componentes elétricos, etc.), essa ferramenta é uma ótima opção. O fato de os parâmetros de construção, manutenção e operação dos componentes estarem bem definidos pelo fabricante facilitam o processo de análise de falhas. Por outro lado, a ferramenta não funciona tão bem para causas humanas e organizacionais.
Algo que pode atrapalhar a metodologia dos porquês é: a técnica é baseada no conceito de que cada falha tem uma causa única — o que, quando falamos de máquinas e equipamentos, é raro. Se várias causas podem resultar na mesma falha, podem ser negligenciadas.
Quando múltiplos caminhos dos cinco porquês na manutenção são utilizados, pode haver mais de uma resposta para algumas das perguntas e a análise se torna complexa. Uma maneira de resolver este problema é, em um mesmo relatório, combinar essa ferramenta com outras citadas abaixo.
2. Análise: Diagrama de Ishikawa (Espinha de Peixe)
O método do diagrama de Ishikawa, chamado também de espinha de peixe, é uma ferramenta gráfica usada para identificar possíveis causas raízes e qual categoria de variações no processo representa a maior fonte de variabilidade na saída.
A metodologia usa um sistema de categorização de causas, seja por função ou por sequência no processo. Em cada categoria, são listadas causas potenciais, que são testadas para validação usando evidências ou outra ferramenta analítica. Dessa forma, temos uma espinha central e as ramificações das causas que formam algo semelhante ao esqueleto de um peixe.
Assim, com esse diagrama, é possível separarmos 6 categorias principais de causas, sendo elas:
- Máquina;
- Mão de Obra;
- Medidas e Dados Quantitativos;
- Meio-Ambiente e Condições de Operação;
- Método;
- Material.
A ferramenta visa categorizar possíveis falhas e quando todo o diagrama estiver preenchido, é possível enxergar o que é ou não, uma possível causa raiz. O preenchimento do Diagrama de Ishikawa começa sempre da direita para esquerda, onde é apontado o efeito da falha e as suas possíveis causas de acordo com a respectiva categoria.

Um diagrama espinha de peixe é útil, pois mostra as relações entre causas potenciais e seus efeitos. É uma boa maneira de envolver as pessoas na resolução de problemas.
3. Análise: Árvore Lógica das falhas
A árvore de falhas nada mais é do que uma maneira organizada de correlacionar falhas e causas. Essa metodologia permite descobrir as raízes físicas, humanas e latentes de uma falha.
Para usar a ferramenta, devemos começar com uma declaração de problema descrevendo o incidente — as falhas funcionais. Após a caracterização e detalhamento das falhas funcionais, deve-se desenhar uma árvore lógica de acordo com os acontecimentos correlatos às falhas.
A segunda etapa é a lista dos modos de falha. Este processo é repetido até que as raízes físicas sejam alcançadas. Serão necessárias interações adicionais para chegar às raízes humanas e latentes.
Parece complicado, mas fica fácil entender como funciona a Árvore Lógica das falhas no exemplo abaixo:

A análise da árvore de falhas é ótima em mostrar como um sistema é resistente às falhas simples ou múltiplas. Pode começar em um nível funcional ou de componente. No entanto, as árvores de falhas também exigem uma definição cuidadosa do problema. Dependendo desse detalhamento, nem sempre é possível encontrar todas as falhas.
Se o escopo do problema for muito grande, o processo fica atolado na análise de elementos não-consequenciais, e se torna uma abordagem de dispersão para tentar abordar raízes que não são causais para a falha.
4. Análise: Diagrama de Pareto
A metodologia do diagrama de Pareto é usada para quantificar e conflitar causas de um evento com seu determinado efeito. Ou seja, a partir desse diagrama, é possível enxergar quais são as causas que mais impactam na disponibilidade e confiabilidade do equipamento.
O diagrama de Pareto é uma representação gráfica dos problemas do processo na ordem de classificação do mais ao menos frequente. Ilustra a frequência dos tipos de falha ou defeito. Usando essa análise, é possível decidir qual evento necessita prioridade para ser solucionado.
A regra básica subjacente ao princípio de Pareto é que, em quase todos os casos, 80% do total dos problemas incorridos são causados por 20% das causas da falha. Portanto, concentrando-se nos principais problemas primeiro, é possível eliminar a maioria deles.

5. Análise: Diagnóstico IA
Uma das formas mais modernas de analisar falhas em equipamentos é através do monitoramentos constante de equipamentos e processamento de dados. Com um modelo baseado na internet das coisas e inteligência artificial, torna-se possível monitorar aspectos básicos e complexos dos ativos em plataformas, podendo ter um controle e diagnóstico muito mais preciso de causas e efeitos das falhas.
Além de criar um histórico consistente de informações sobre manutenções e condição dos equipamentos, a boa análise de dados detecta falhas quando estão no estágio inicial, permitindo que equipes de manutenção ajam antes que a quebra ocorra. Ou seja, as análises são feitas quando ainda existe possibilidade de contornar a situação. Como assim?

Ao inspecionar, por exemplo, o entupimento do filtro de uma bomba d’água, a análise de dados permitiria identificar um aumento da temperatura do equipamento logo quando o filtro fosse prejudicado. Dessa forma, a equipe de manutenção poderia intervir e trocar o filtro antes que uma falha grave parasse toda a produção.
Ao utilizar outros métodos, possivelmente a análise da falha só ocorreria depois que o estrago estivesse feito. Por isso, muitas indústrias estão buscando plataformas de manutenção especializadas nesse tipo de análise.
Se quiser saber mais sobre como implementar uma plataforma para monitorar os dados de seus equipamentos fale com algum de nossos especialistas e agende uma demonstração abaixo: