Na indústria, a análise de falhas é um método muito utilizado para encontrar possíveis causas raiz de falhas ou quebras em processos produtivos. Isso ocorre em diversas situações em um processo fabril, não sendo exclusivamente corretivas em máquinas e equipamentos.
O nosso foco aqui, é falar sobre a manutenção de ativos e o uso desse método para encontrar a causa raiz de falhas ou quebras. Um fator importante que precisamos enfatizar é que realizar uma análise de falhas, normalmente é para eventos que já aconteceram. Mas isso também pode ser feito para falhas potenciais, ou seja, quando se procura alcançar a confiabilidade de um ativo.
Quando usar o método da análise de falhas?
Colocar em prática a metodologia de análise de falhas requer alguns parâmetros que devem ser estabelecidos pela Gestão ou do PPCM. Esse método de análise de falhas é vital na gestão da manutenção, pois através dela é possível conhecer a causa raiz das falhas, quebras ou defeitos.
Outro fator também que pode-se considerar, é que esse método é viável para evitar recorrências (corretivas), prevenir possíveis ocorrências (confiabilidade), ou mesmo as duas situações simultâneas. Podemos ter falhas que podem ser avaliadas em ativos similares ou diferentes, mas com componentes, equipamentos ou peças iguais ou similares.
Independentemente das estratégias que a manutenção trabalha, é importante definir alguns parâmetros para disparar a necessidade de fazer a análise de falhas que poderiam ser:
- Máquinas classificadas com nível de criticidade “A”, todas as paradas por falhas devem ser analisadas;
- Máquinas classificadas com nível de criticidade “B”, deve-se analisar todas as paradas por falhas acima de 2 horas de interrupção;
- Máquinas com taxa de utilização de produção acima de 70% devem fazer análise de falha;
- Falhas que elevam os riscos de segurança ou de riscos ambientais devem ser todas analisadas;
- Falhas com alto índice de repetitividade, por exemplo: acima de 5 ocorrências no mês;
- Falhas de um ativo independentemente da sua criticidade e que podem acontecer em outros iguais ou similares, devem fazer a análise de falhas.
Como vimos acima, esses parâmetros são necessários e podem ser definidos em conjunto entre Manutenção, Produção, Gerência Industrial e PCP, por exemplo.
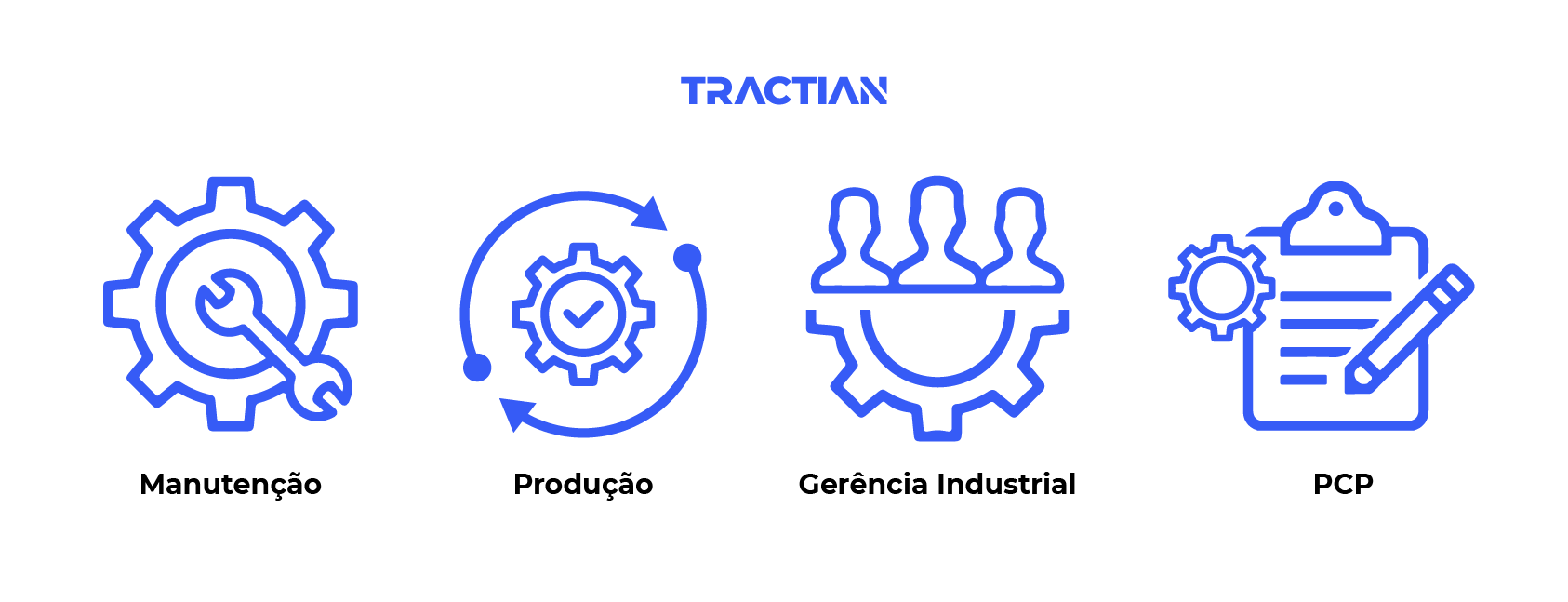
Metodologia de Análise de falhas
Normalmente a Gestão da Manutenção e PPCM elaboram um procedimento operacional padrão (POP), para ser seguido por todos ao fazer a análise de falhas que pode ser da seguinte maneira:
- Elaborar um formulário padrão para registro da falha;
- Definição dos participantes do processo de análise de falhas;
- Definição das ferramentas de análise a serem usadas tais como: Gráfico de Pareto, brainstorming, Diagrama de causa e efeito (Ishikawa), 5 Porquês entre outros;
- Definição de como as ações sugeridas serão implementadas e verificação dos seus resultados;
- Definição de plano de replicação em casos de máquinas iguais ou similares.
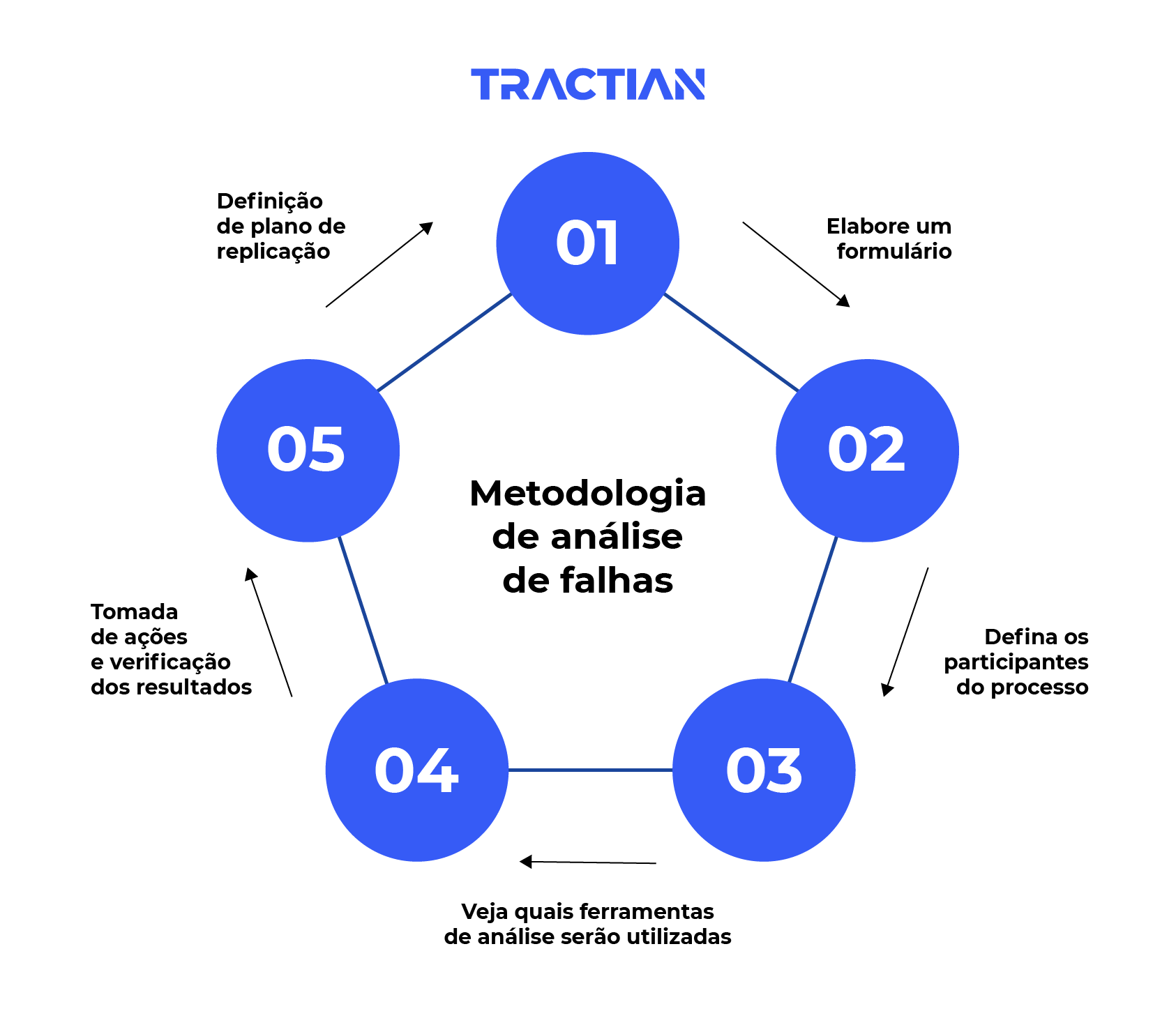
Definido quais parâmetros a seguir, é necessário criar um fluxograma da análise de falhas definindo também quem “dispara” e conduz todas as etapas do processo. Normalmente quem faz isso é o PPCM ou alguma pessoa destinada pelo gestor da área.
Outro fator importante, é que para cada análise de falhas se faz necessário a participação de pessoas envolvidas para cada ocorrência do evento.
Exemplo: digamos que uma máquina está apresentando falhas de impressão em potes plásticos e por conta disso, está perdendo produtos por causa dessas irregularidades. A manutenção então é acionada várias vezes para intervir, porque considera que o problema está em algum sistema da máquina.
Nesse caso é importante participar dessa análise de falhas: o operador ou líder dessa máquina, os manutentores que trabalharam nas intervenções e alguém da qualidade que identificou o problema. E claro, o PPCM como condutor do processo ou o responsável pela gestão.
E não pode faltar o produto com a falha e possíveis peças trocadas durante as intervenções. Como podemos entender, tudo o que se relaciona com essas falhas deve fazer parte desse processo.
O método de análise de falhas é investigativo e para isso precisa de um histórico com todas as informações e itens que fizeram parte do problema.
Melhores práticas na manutenção
Quando pensamos no conceito das melhores práticas, isso quer dizer que ao longo do tempo e da experimentação, certa maneira de fazer algo se mostrou como a melhor opção e solução para um determinado problema ou operação.
Na manutenção, as melhores práticas seguem o mesmo caminho, onde a ambição é, por exemplo, diminuir os custos de manutenção até um valor aproximado de 2% do orçamento, como um cumprimento de 90% da programação de serviços.
No Brasil, costuma-se pensar que programas têm começo e fim, mas na realidade, é um processo constante e interminável, as melhores práticas na manutenção devem estar em curso de maneira constante, assegurando que o que se busca atingir seja um compromisso adotado em todas as etapas do processo.
Um dos primeiros passos é o treinamento das pessoas, visto que para atingir as melhores práticas, o coletivo da equipe deve estar preparado para desempenhar o que for necessário, da melhor maneira possível. Além da adoção de uma sistemática, envolvimento de toda a organização, perseverança na aplicação e acompanhamento do progresso.
Análise do Modo e Efeito da Falha – FMEA
Como uma das integrantes das melhores práticas, a Análise do Modo e Efeito da Falha (Failure Mode and Effect Analysis, em inglês) é um dos métodos mais recorrentes e indicadas no chão de fábrica para pretende identificar e analisar as falhas em potenciais por meio de sua hierarquização.
A FMEA se organiza em três estágios: projeto, processo e sistema. Para iniciar, o projeto se baseia na eliminação de falhas ainda quando o equipamento está em fase de projeto, ou seja, ele ainda não está pronto, mas já pode ser revisto e analisado para evitar que falhas aconteçam no futuro, como a mantenabilidade e segurança.
O processo é focado em como o equipamento opera e como é mantido, enquanto o sistema se preocupa com o gargalo geral da operação. A manutenção, por sua vez, se preocupa mais com o que tange ao processo, pois é nesse estágio onde pode interferir de maneira mais direta e combativa.
A equipe que atuará no processo deve ser composta de engenheiros e técnicos, com conhecimentos multidisciplinares capazes de aprimorar as análises e identificar com mais clareza as falhas de cada equipamento.
Em suma, a FMEA é a medida de risco de uma falha. Portanto, quanto mais pessoas estiverem envolvidas nesse processo, maiores serão as chances de acertos e de resultados com altas taxas de confiança.
Benefícios da análise de modo de falha e efeitos
O uso desse método para encontrar a causa raiz de um problema, quer seja uma falha, defeito ou quebra, traz muitos benefícios. Dentre eles podemos citar alguns como:
- Evitar a recorrência do problema;
- Evitar que essa ocorrência aconteça em ativos iguais ou semelhantes;
- Maior disponibilidade do ativo;
- Menores custos de manutenção;
- Maior segurança de operação;
- Melhoria dos métodos de trabalho;
- Possibilidades de melhorias nas partes analisadas;
- Moral da equipe elevada.
Bons resultados de uma análise de ocorrência de falhas começa com definições de responsabilidades e métodos assertivos na sua realização. É muito importante também a definição de quando fazer uma análise, já que tudo começa com premissas.
Uma alternativa é considerada um dos meios mais modernos para análise de falhas, é pelo monitoramento online. Nele os ativos críticos ao processo, são monitorados o tempo todo por sensores IoT combinados à uma inteligência artificial, assim o gestor tem controle e um diagnóstico mais preciso de causas e efeitos.
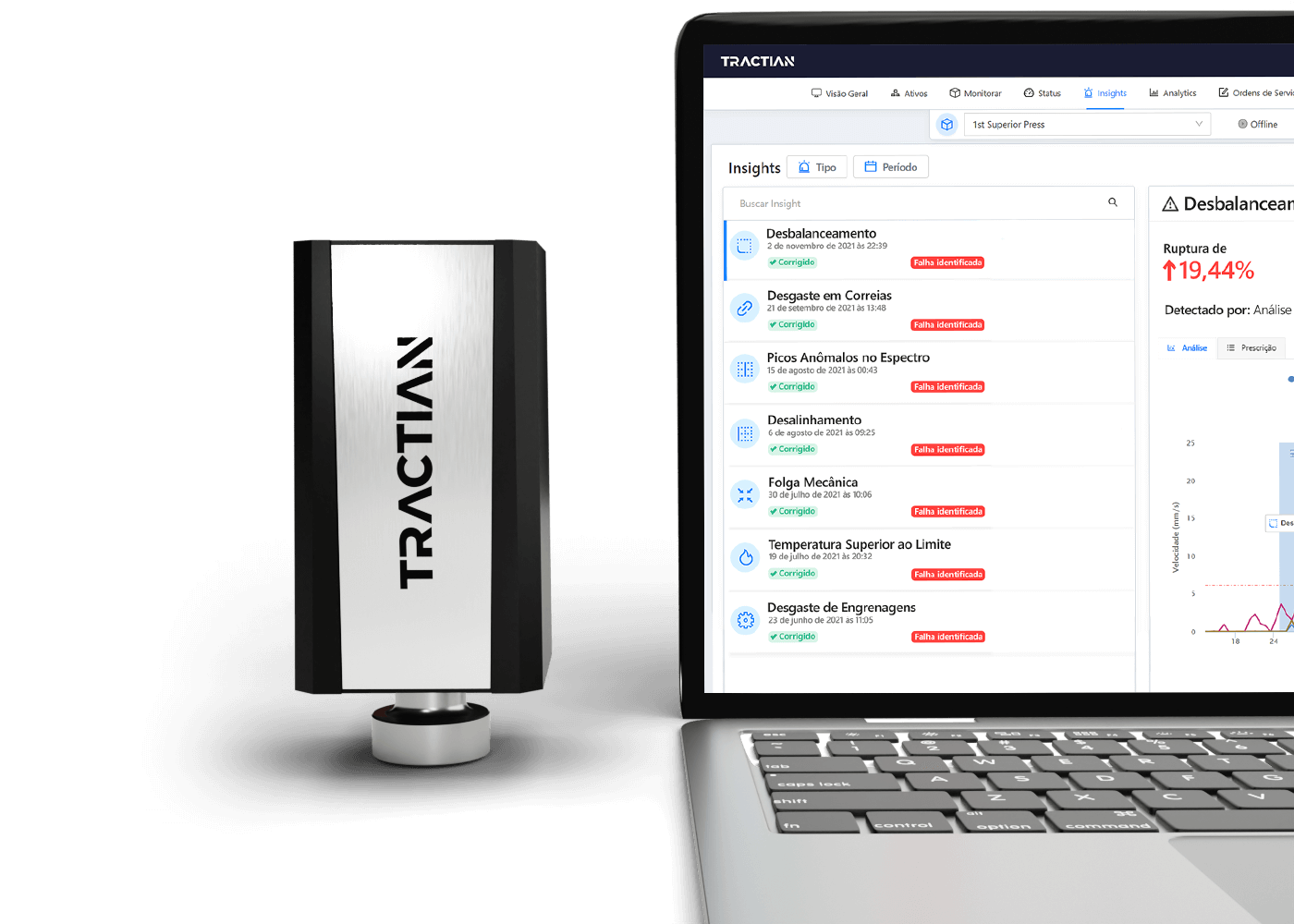
O monitoramento constante cria um histórico de dados sobre as ocorrências e as condições dos ativos, permitindo agir antes que ocorra a quebra.
Saiba como implementar esse método e livrar de vez das falhas inesperadas nos seus equipamentos, agende uma demonstração.