Sabe o que realmente tira o sono de quem está à frente da manutenção em uma indústria? Se pensou em downtime, acertou.
Esse é um problema que ameaça os resultados operacionais e financeiros das empresas por todo o mundo — que assola desde as manufaturas de bairro, até as principais indústrias de um país.
Mas o que é exatamente e como podemos colocar um freio nessas paradas não programadas?
É o que vamos compartilhar nesse artigo: toda nossa expertise — de forma condensada — sobre o tempo de inatividade, suas causas raízes, estratégias de prevenção e o papel das tecnologias para mitigar esse problema.
Vamos lá? É só continuar a leitura.
Downtime: O que é + tipos
Downtime é algo que pode virar um pesadelo para quem gerencia o chão de fábrica. Basicamente, trata-se do tempo de inatividade de uma máquina ou equipamento. Ou seja, é quando a produção para, ponto.
Porém, muita calma, nem todo downtime é vilão.
Existe a parada planejada ou parada técnica, o momento em que a empresa diz: “Vou parar para fazer uma manutenção preventiva ou trocar um equipamento”.
Ou seja, tudo sob controle.
Agora, o downtime não planejado é o problema que causa dores de cabeça.
Aquele que aparece quando uma máquina pifa do nada ou a energia vai embora sem avisar.
É esse tipo “ruim” que ninguém quer, mas que todo chão de fábrica enfrenta.
Sem perder tempo: a TRACTIAN tem as soluções necessárias para seu negócio ELIMINAR o tempo de inatividade em suas máquinas. Descubra como!
Impactos das paradas não planejadas na indústria
As paradas não planejadas são o calcanhar de Aquiles na indústria, afetando tudo: da linha de montagem até os números finais do financeiro.
O Grupo Aberdeen mostrou isso em números em uma pesquisa feita alguns anos atrás: de acordo com os cálculos deles, as paradas não planejadas podem custar cerca de €220.400 (isso mesmo, euros!) por hora.
E não para por aí, a CXP Group aponta que para as empresas europeias, 90% dos principais pontos críticos que enfrentam vem do downtime não planejado e da manutenção emergencial.
Isso significa produção parada, entrega de pedidos atrasada, e claro, dinheiro perdido.
E não é “só” o financeiro que leva a pancada: a moral da equipe e a confiança dos clientes também levam um baque.
Ou seja, downtime não planejado é sinônimo de problemas em 360 graus para o negócio.
10 principais causas de downtime na Indústria
Certo, mas o que mais causa o tempo de inatividade em um negócio? Compilamos os principais:
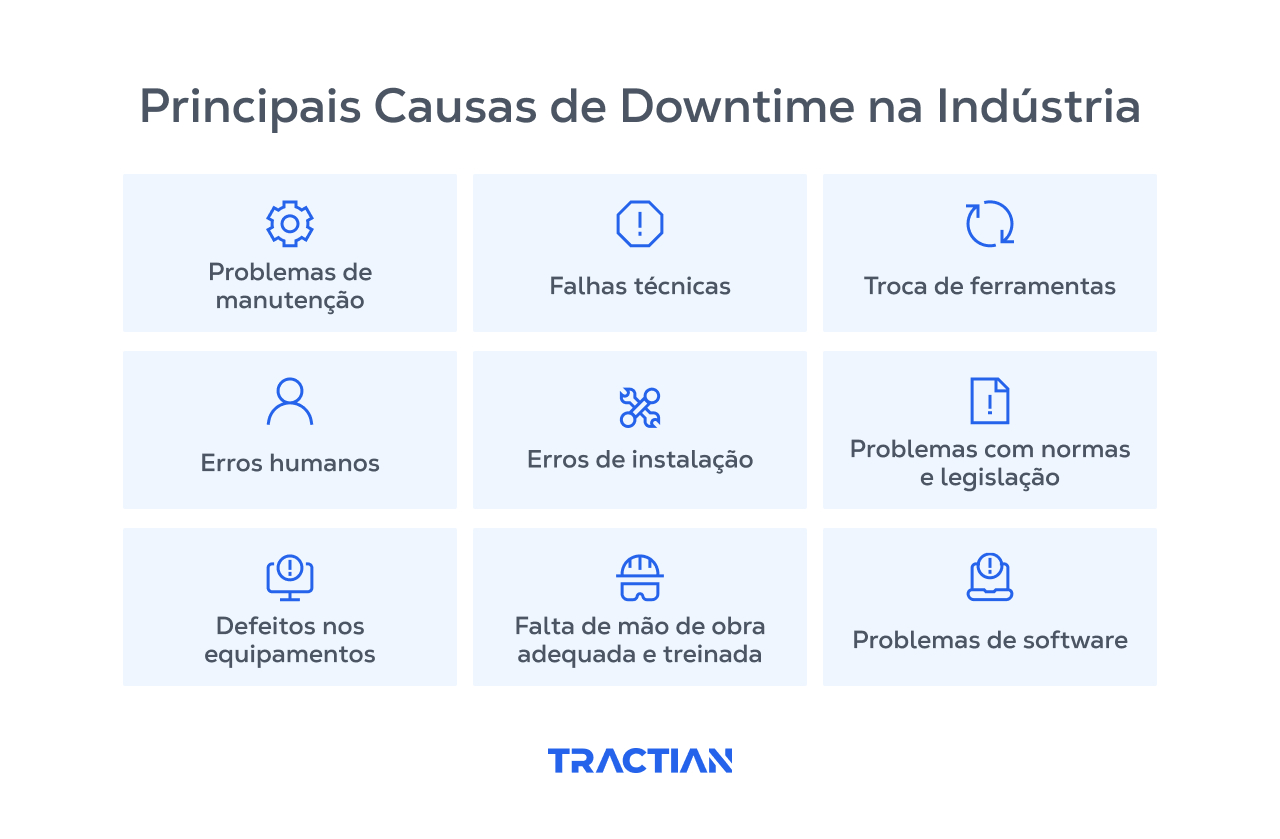
- Problemas de manutenção;
- Falhas técnicas;
- Troca de ferramentas;
- Falhas logísticas;
- Problemas de infraestrutura;
- Falha de gerenciamento;
- Erros de instalação;
- Problemas com normas e legislação;
- Defeitos nos equipamentos;
- Falta de mão de obra qualificada.
Cada uma dessas causas tem seu papel nas paradas não planejadas. Manutenção negligenciada, falhas técnicas ou um simples erro humano podem transformar um dia normal em um caos total.
E não é só isso: problemas legais ou mesmo na instalação também jogam no time do downtime.
Entender esses fatores é o primeiro passo para evitar que eles transformem seu chão de fábrica num palco de desastres.
Como medir e monitorar as paradas não programadas?
Como qualquer tarefa de gestão, o monitoramento e a medição depende de uma coisa: entender quais são os KPIs e métricas certas. Separamos uma lista com os principais.
Anote-os e nos diga: eles já fazem parte da sua gestão de indicadores?
- MTBF (Mean Time Between Failures): tempo médio entre falhas.
- MTTR (Mean Time To Repair): Tempo médio para reparar.
- Availability (Disponibilidade): Quanto tempo os equipamentos estão prontos para funcionar.
- Backlog: A fila de trabalhos esperando para serem executados.
- Confiabilidade de ativo: Quando sua máquina funciona sem dar problemas.
- Lost time (Tempo perdido): Cada segundo conta quando o jogo é a produção.
- MPd – Cumprimento dos planos de manutenção preditiva: Sua empresa possui e segue à risca o cronograma de manutenção e os dados preditivos obtidos?
- OEE (Overall Equipment Effectiveness): É a principal métrica, que diz se seus equipamentos estão realmente ajudando o negócio ou sugando seus recursos.
- PMP (Planned Maintenance Percentage): O quanto da sua manutenção é planejada versus a corrida contra o tempo.
Como acabar com o tempo de inatividade? 5 Dicas para aplicar já!
1. Tenha um planejamento de manutenção
Anote de forma minuciosa como está sendo realizado o trabalho de manutenção, esse acompanhamento é ideal para reduzir ou até eliminar as corretivas de emergência e, por consequência, a dinâmica do quebra/conserta das máquinas.
Além disso, lembre-se de considerar como as tarefas estão sendo atribuídas e metrificadas na manutenção industrial.
Acompanhar os indicadores é uma forma de medir os resultados da manutenção.
Separamos um artigo sobre indicadores de manutenção se você quiser conhecer tais métricas e melhorar o desempenho da sua empresa.
2. Pare de apagar incêndios
Busque prevenir falhas inesperadas ao invés de apenas consertá-las. A partir disso é possível agir proativamente na manutenção, evitando paradas fora de hora.
Planeje quais acontecimentos podem gerar uma falha futura e execute uma inspeção antes que seja tarde demais.
3. Mantenha as paradas de manutenção dentro do cronograma
Planeje todos os aspectos antes de realizar a parada. Tente manter um cronograma, especificando quem irá realizar tal manutenção, quando e onde.
Realizando o trabalho de forma mais efetiva e otimizada. Uma maneira de executar tal tarefa é criar ordens de serviços para o colaborador mais apropriado para aquela atividade.
Com a Tractian é possível automatizar essas ordens de serviço e garantir uma maior segurança para a sua indústria.
4. Utilize equipamentos de monitoramento
Monitore constantemente seus equipamentos para identificar os primeiros sinais de falhas.
Sensores inteligentes conseguem coletar dados de vibração e identificar possíveis problemas que podem gerar a quebra do equipamento.
Escrevemos um artigo sobre como a análise de vibração pode ajudar na saúde dos ativos. Que tal separar um tempinho para ler logo após esse conteúdo?
5. Use sensores inteligentes
Utilizar técnicas preditivas aliadas a manutenção preventiva, é fundamental para evitar que paradas indesejadas afetem a produção.
O sensor IoT, Smart Trac, monitora dados de vibração, temperatura e horas trabalhadas do ativo, todos os dias da semana, sendo um processo automatizado. Já que minutos depois de ser acoplado ao ativo, ele já começa a coleta de dados.
Assim, é possível entender a real condição do ativo, evitando qualquer tipo de quebra inesperada. Ao menor sinal de falha identificada os gestores e responsáveis pelo ativo são avisados, agindo antecipadamente.
Como diminuir paradas não programadas
A cultura organizacional é essencial na luta contra as paradas não programadas. Uma mentalidade de melhoria contínua não só prepara o terreno para prevenir o downtime, mas também cria um ambiente onde ele é gerenciado de forma proativa.
Quando a cultura da empresa encoraja a antecipação de problemas e a inovação constante, paradas inesperadas tornam-se cada vez menos frequentes.
Além disso, um ambiente que valoriza a capacitação e a colaboração fortalece as equipes, permitindo que elas respondam rapidamente e eficientemente aos imprevistos.
Assim, fomentar uma cultura que prioriza a eficiência operacional e a resiliência é fundamental para minimizar essas situações.
No seu negócio, essas ações são incentivadas?
Downtime e Sustentabilidade
Quem diria que reduzir o downtime pode dar um boost nas práticas sustentáveis? Isso mesmo, controlar as paradas não programadas não é só bom para o bolso, mas também para o planeta!
Pense bem: encaixar essa “vontade” na estratégia de ESG (Ambiental, Social e Governança) da empresa é uma jogada de mestre.
Mas como? Menos paradas não programadas significa menos desperdício de recursos, menos emissões e mais eficiência operacional.
Ou seja, você avança duas casas de uma vez só: otimiza a produção e ainda dá um upgrade na responsabilidade ambiental e social.
Assim, cada ação para reduzir o tempo de inatividade se transforma em um passo firme em direção à sustentabilidade.
Conclusão
Esse é o fim do nosso guia sobre paradas não programadas.
Vimos que lidar com as paradas não programadas é essencial para manter a indústria girando sem perrengues.
Desde entender o que é downtime, passando pelas suas causas, até as táticas de medição e monitoramento, tudo aponta para a necessidade de uma gestão esperta e proativa.
E, claro, sem esquecer da pegada sustentável que uma boa gestão de paradas traz, alinhada ao ESG.
Agora, é hora de as empresas abraçarem uma visão holística e inovadora, tornando a gestão de inatividade parte integral da estratégia para sucesso industrial.
Vamos nessa, fazer a diferença e manter as máquinas rodando?
Conte com a TRACTIAN
Nossas soluções são feitas sob medida para elevar sua estratégia de manutenção, enriquecendo seus esforços para reduzir custos, tempo de inatividade e desorganização do chão de fábrica.
Não por menos, os clientes da TRACTIAN experimentam um sintoma em comum: payback em menos de 4 meses, com ROI de até 18x do valor investido em nossas soluções.
E quais são essas soluções? Olhamos tanto para o backoffice industrial, quanto para a fábrica em si.
Primeiro, vale a pena conhecer nosso CMMS/EAM, um software de gestão de manutenção que vai além de um simples CMMS e atua como um EAM, possibilitando um gerenciamento aprofundado de todos os seus ativos.
E claro, nossos sensores inteligentes: Energy trac (para monitorar os níveis de energia) e o Smart Trac Pro (que revoluciona sua gestão de ativos e disponibilidade).
Um exemplo? A Vetorial Siderurgia, que eliminou mais de 1,2 mil horas de manutenção corretiva com nossa solução de Autodiagnóstico™ de Falhas, reduzindo 30% do custo geral de manutenção.
Fale com nossos especialistas e entenda como a TRACTIAN pode ajudar seu negócio a eliminar o fantasma do downtime.