Considerando todos los factores que afectan la productividad y rentabilidad de una empresa, la pérdida de producción en operaciones de mantenimiento es una de las principales causas. Después de todo, es la principal variable en rentabilidad y resultados.

Las pérdidas de producción son problemas que afectan a la empresa de diversas formas, ya que disminuyen la producción y generan importantes pérdidas económicas. La búsqueda de mejoras debe ser continua: al reducir el coste de mantenimiento se agiliza la cadena productiva, y con ello se obtienen mejores resultados a final de mes.
Sin duda, una parte importante de la prevención, es conocer las principales causas de retraso de producción. En este post te explicamos 7 de ellas son algunas de éstas y cuáles son las técnicas de mantenimiento predictivo y los sistemas de gestión adecuados para enfrentarlas.
1. Parada en la línea de producción
La fabricación de un producto en cualquier industria está directamente relacionada con el funcionamiento de la producción y operación de sus máquinas. En consecuencia, si uno de ellos deja de funcionar, toda la fábrica se verá afectada.
- Mantenimiento correctivo: uno de los que causa mayor daño, pues se realiza cuando un componente del equipo presenta una falla funcional y necesita ser reemplazada por falta de prevención.
- Puesta a punto del equipo: ocurre cuando se interrumpe la producción para preparar la maquinaria para un nuevo envío de productos o limpieza.
- Ociosidad: es posible identificar cuando no hay miembros del equipo disponibles para manejar el equipo.
- Materia prima: la cadena de suministro puede fallar y alterar la entrega de insumos, tanto en tiempo como calidad.
- Retraso en la entrega entre líneas de producción: ocurre cuando el paso anterior se retrasa en la secuencia de producción, o la siguiente se sobrecarga.
Para evitar que ocurran todos estos imprevistos, la empresa debe asegurarse de realizar un mantenimiento planificado, dotando a los técnicos e ingenieros de una plataforma capaz de mostrar las condiciones de funcionamiento reales del equipo para apoyarles a evitar las paradas inesperadas en la producción.
Toda la estrategia de mantenimiento industrial debe funcionar con base en información obtenidas en procedimientos de termografía, ultrasonido, análisis de aceite, vibración y temperatura, para identificar si existe necesidad de revisión por adelantado y eliminar el desmontaje innecesario.
Conoce el Software Líder de Gestión del Mantenimiento
2. Exceso de producción
Cuando el responsable de esta tarea realiza la adquisición de demasiados insumos, sin planificación, automáticamente aumentan los costos innecesariamente y se ocupa mucho espacio de almacenamiento.
Por lo tanto, es fundamental que el gerente comprenda las necesidades del departamento de mantenimiento y producción, comprando materiales que realmente satisfagan la demanda.
Por un lado, se debe evitar la producción cuantitativa. Es cuando se produce mucho más que los pedidos. Por ejemplo, una industria recibió un pedido de 200 piezas, pero el gerente decidió producir 350. Al final de la producción, el exceso estará en stock.
Por el otro lado, con una buena planeación, el gerente de mantenimiento puede implementar producción por anticipación, que consiste en mantener un stock de producción regular previo a la solicitud de pedidos.
Para que esto suceda e influya positivamente al calcular la rentabilidad, es fundamental que el gerente pueda monitorear los equipos, asegurando que toda la producción anticipada sea acorde con cada pedido y con su plan de gestión de activos.
3. Almacenamiento
El stock de una empresa no solo está compuesto por productos terminados, sino también por insumos que conforman la cadena de producción. Si se tiene un volumen muy alto de materias primas detenidas, habrá pérdida de capital y espacio de almacenamiento.
Por lo tanto, es fundamental que el gerente solicite únicamente aquellos insumos que necesita la producción.
4. Falta de gestión asertiva
Cuando la gestión de activos es ineficiente por un exceso de órdenes de trabajo sin procesar, generalmente da lugar a que las intervenciones correctivas consuman tiempo y dañen la rentabilidad.
El uso de tecnología para aminorar la carga de trabajo produce el efecto contrario: incrementan la rentabilidad. Por ejemplo, usar un Software de Mantenimiento GMAO (CMMS) facilita la planificación de las tareas de mantenimiento, pues automatiza las órdenes de trabajo de forma simple y rápida.
Además, genera indicadores de mantenimiento clave sobre los activos críticos de la planta, con lo que se robustece la base de datos disponible. Con esto, el gerente puede plantear objetivos más ambiciosos para el equipo de mantenimiento y agilizar su toma de decisiones.
Este tipo de mantenimiento tiene como objetivo optimizar los procesos y hacer que el día a día de la empresa sea vuelva más dinámico y competitivo.
Descarga ebook: Software de Gestión CMMS/GMAOAutomatiza y optimiza tu gestión.¿Qué es la CMMS/GMAO?Las ventajas de utilizar la CMMS/GMAOTracOS™: El Software líder de gestiónDescarga Ebook
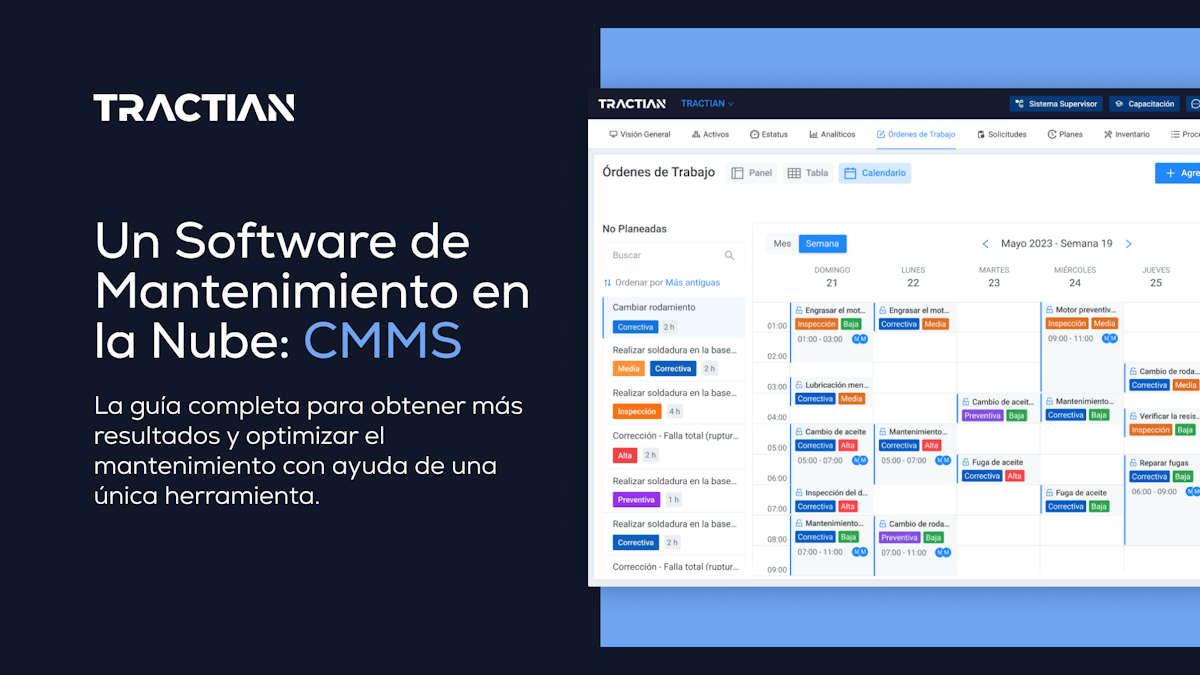
5. Falta de logística adecuada
Cuando hablamos de la logística de una empresa, no debemos pensar solo en la entrega del producto al consumidor. La logística comienza con un diseño bien organizado.
Si las prácticas no benefician el flujo continuo de las rutinas de la empresa, obligando a los empleados a realizar movimientos innecesarios, dificultando la comunicación, o desordenando los insumos, seguramente interferirá en la productividad de los empleados.
Por ello, contar con un árbol de equipos bien planificado según las necesidades de cada sector es sin duda una ventaja.
6. Desperdicio en actividades ineficaces
Si tu empresa no genera las ganancias esperadas, es probable que se deba a que los empleados pierden mucho tiempo en la realización de actividades de carácter más operativo.
Este desgaste se puede reducir automatizando procesos y asignando empleados a actividades relevantes. Así no sólo se aumenta el rendimiento y se agilizan los procesos, sino que facilita a los encargados de la gestión de equipos acceder fácilmente los procedimientos.
7. Fabricación de productos defectuosos
Encontrar productos que no cumplen con los estándares de calidad y que no funcionan bien, generan no solo problemas en el servicio al cliente, sino también un daño importante a la empresa. La fabricación sin calidad resulta en pérdidas de producción.
Este tipo de merma suele ocurrir cuando el producto está dañado o cuando se toman acciones innecesarias en el activo para cumplir con las especificaciones del pedido.
Tener un control de calidad y un equipo bien capacitado es fundamental para que la empresa no tenga defectos en el proceso. Además, tener una visión clara de las máquinas garantiza el conocimiento sobre la confiabilidad de los activos.
Disminuye tus pérdidas en producción con TRACTIAN
Para evitar estas pérdidas en la producción, podemos utilizar la tecnología como un aliado importante.
Con un sistema de monitoreo en tiempo real, donde es posible administrar todo el árbol de activos, recibir datos asertivos sobre la condición del equipo, los técnicos no tendrán la necesidad de recolectar datos manualmente.
Además de realizar las tareas de forma más eficiente, con una adecuada planificación, evitando pérdidas y asegurando la productividad de la planta.
Obtén más información sobre cómo la plataforma Tractian puede ayudar a aliviar sus pérdidas de producción.