Es común escuchar hablar de “actividades de mantenimiento” como si fueran actividades generales, pero esto no es del todo cierto. Existen algunos tipos principales de mantenimiento y, dentro de ellos, subtipos, que al no conocerse en profundidad pueden generar confusión.
Ya conocemos los términos correctivo, preventivo y predictivo: TRACTIAN incluso explicó las diferencias entre estos tres grupos de actividades de mantenimiento en otro artículo. Pero saber qué significan estos tres conceptos generales no es suficiente.
Para que el plan de mantenimiento sea lo más asertivo posible, previniendo fallas antes de que sucedan y reduciendo los costos del sector, el gerente debe dominar todos los tipos de subtipos de mantenimiento. Solo así sabrás designar la actividad idónea para cada activo, definiendo con precisión qué, dónde y cuándo se debe realizar.
Descubra a continuación los ocho tipos de mantenimiento más importantes, así como sus diferencias y situaciones ideales de aplicación – contenido adaptado por TRACTIAN basado en el libro “A Anatomia do PPCM”, de José Wagner Braidotti Jr.
Y nunca lo olvide: el plan ideal involucra todos los tipos y subtipos, priorizando la implementación de herramientas tecnológicas e inteligentes, capaces de hacer que las actividades de mantenimiento sean aún más precisas y rentables. ¡Disfruta de la lectura!
Mantenimiento Correctivo / Corrective Maintenance
El mantenimiento correctivo es el más antiguo, el menos complejo y el más caro. Pero tranquilos, esto no quiere decir que el correctivo sea malo o que deba quedar fuera del plan.
Consiste en reparar o reemplazar componentes después de una falla, o cuando está a punto de ocurrir. A menudo no está programado, lo que aumenta su impacto financiero (es costoso y retrasa la producción).
Por lo tanto, los mantenimientos correctivos, especialmente los de emergencia, deben evitarse con la ayuda de otros tipos de mantenimiento, pero no excluidos del plan. Después de todo, no todo es predecible y evitable, y el gerente siempre debe estar preparado para un reemplazo o una reparación “sorpresa” de equipos críticos.
Para saber más sobre la criticidad de los equipos y qué actividades de mantenimiento son las más adecuadas para cada grado, consulta este artículo de TRACTIAN.
Podemos separar el mantenimiento correctivo en dos aspectos, en función de la predictibilidad de la falla que la intervención busca corregir.
Mantenimiento Correctivo No Planificado (CNP) / Unplanned Maintenance
El Mantenimiento correctivo no planificado generalmente lo llamamos solo “correctivo”, “de emergencia” o “reactivo”, y algunos lo llaman Mantenimiento Correctivo No Predecible. En inglés, se puede encontrar como Unplanned Maintenance ou Unscheduled Maintenance.
Básicamente, consiste en la actividad de mantenimiento no planificada que se lleva a cabo después de ocurrir una falla funcional del activo.

Como este problema sorprende al equipo de mantenimiento, lo ideal es que la falla funcional que antecede a una actividad correctiva ocurra en equipos menos críticos. Así, el impacto económico es menor, ya que estos son generalmente más sencillos y económicos de reparar o reemplazar, y no afectan la continuidad de la producción.
Para garantizar que los activos más importantes para la operación no necesiten correcciones de emergencia, el gerente debe priorizar otras técnicas de mantenimiento en el plan, como el monitoreo en línea y constante de activos críticos, que presentaremos más adelante.
Mantenimiento Correctiva Programado (CPL) / Planned Maintenance
El mantenimiento Correctivo Programado también es conocido como “urgente”, es la actividad de mantenimiento prevista y planificada que se realiza luego de la ocurrencia de una falla funcional en la máquina. A diferencia del anterior, se utiliza mayoritariamente para solucionar problemas que no están afectando directamente el pleno funcionamiento del equipo.
Por ser programado, es mucho más económico, seguro y rápido que el correctivo de emergencia. Y dicha planificación suele definirse en base a un seguimiento predictivo o detectivo del componente, y puede aplicarse a activos de alta y baja criticidad.
Descarga ebook: Tipos de MantenimientoLa guía completa para especialistas de la industria.¿Cuáles son los tipos de mantenimiento?¿Cuándo y cómo debo aplicarlos?Aprender los pasos de cada unoDescarga Ebook
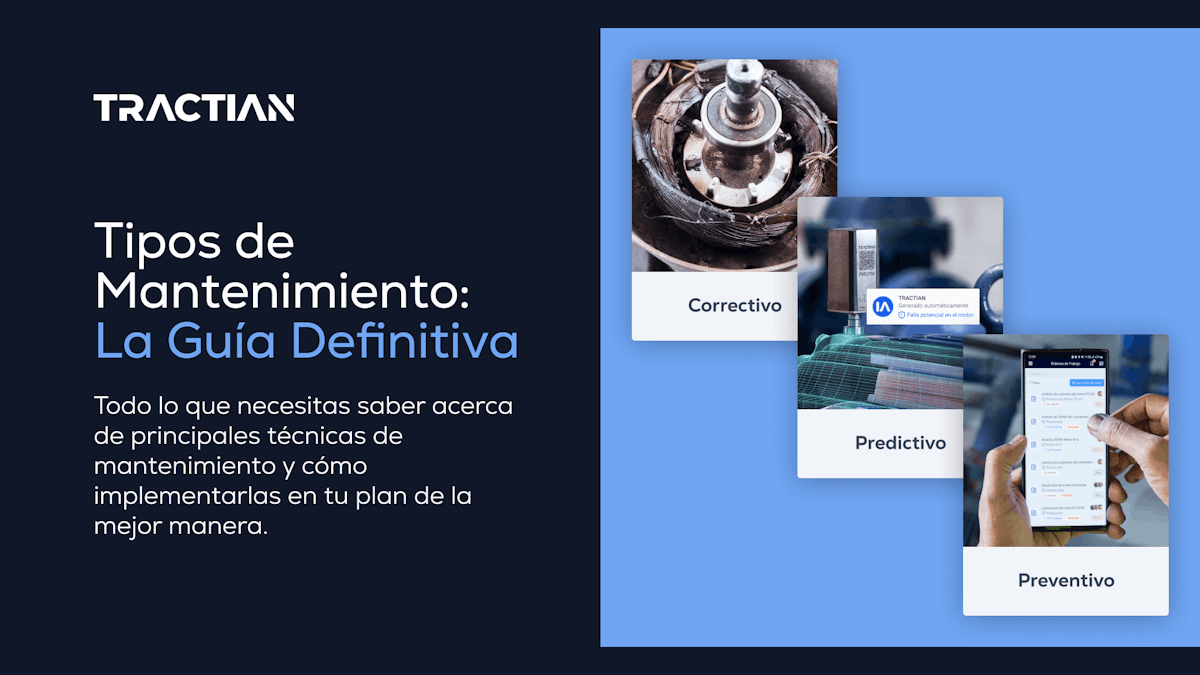
Mantenimiento Preventivo / Preventive Maintenance
Esencial para garantizar la eficiencia y confiabilidad de la maquinaria industrial, el mantenimiento preventivo trabaja con actividades para detectar, reemplazar y reparar componentes y activos antes de que ocurra cualquier falla.
Al explicar la definición de la norma 5462 de la Asociación Brasileña de Normas Técnicas (ABNT), las actividades preventivas tienen como objetivo reducir el desgaste y la posibilidad de fallas en los equipos, que generalmente surgen con el mal funcionamiento de las máquinas. En la práctica, se conocen revisiones periódicas, ajustes de rutina, calibraciones e inspecciones.
Las técnicas preventivas de mantenimiento son muy populares, pero una cosa que no todos los técnicos de mantenimiento conocen es que estas estrategias se dividen en dos tipos: mantenimiento preventivo basado en el tiempo y mantenimiento preventivo basado en la condición.
Es importante conocer las diferencias y aplicaciones de cada grupo para poder programar las intervenciones con mayor precisión y hacer más estratégico el plan de mantenimiento.
Mantenimiento Preventivo Basado en Tiempo (TBM) / Time Based Maintenance
Esta técnica es la que solemos llamar mantenimiento “preventivo” en el día a día del sector. Sus actividades, como su nombre ya lo explica, se definen en función del tiempo de uso del activo físico en cuestión, que suele pertenecer a los grupos más críticos (A y B).
Las intervenciones del mantenimiento TBM cumplen varios factores: siempre son periódicas y predeterminadas en el plan de mantenimiento, generalmente no requieren mano de obra especializada y pueden ser realizadas por los propios operarios de la cuadrilla, previa formación ofrecida por la empresa. Estas acciones pueden ser inspección visual, lubricación, limpieza de la máquina y reemplazo anticipado de piezas, dependiendo del tiempo de servicio del activo.
Si bien es excelente para ahorrar recursos, prolongar la vida útil del equipo, mejorar el funcionamiento y prevenir accidentes, el mantenimiento preventivo basado en el tiempo a menudo puede resultar más aleatorio que efectivo.
Es común, debido a la naturaleza aún conservadora del sector de mantenimiento en latinoamerica, establecer intervalos más cortos para las actividades preventivas, lo que conduce a paradas y reemplazos innecesarios. Lo ideal, por tanto, es combinar esta técnica con otra más asertiva y basada en datos.
Mantenimiento Preventivo Basado en la Condición (MPC ou CBM) / Condition Based Maintenance
Es posible que ya hayas escuchado a alguien llamar “predictivo” a lo que en realidad era un MPC. Es la actividad de mantenimiento realizada luego del diagnóstico periódico (TBM) realizado en campo.
A diferencia del anterior mantenimiento preventivo, este tipo de mantenimiento se basa en el estado real del activo físico respondiendo preguntas como: ¿cómo es su funcionamiento? ¿Cumple con la funcionalidad esperada en el proceso en el que está instalado?
La principal herramienta utilizada aquí (y que justifica el apodo que recibe) es precisamente otro tipo de mantenimiento, el predictivo. Con la ayuda de la recopilación de datos en tiempo real y los diagnósticos detallados que ofrecen las herramientas predictivas, es posible definir, planificar e implementar acciones preventivas más precisas que consideren los aspectos externos e internos de la máquina.
A diferencia del TBM, el mantenimiento preventivo basado en condiciones requiere experiencia técnica avanzada y, por lo tanto, generalmente se subcontrata a empresas especializadas. Sin embargo, en los últimos años han surgido tecnologías capaces de suplir esta necesidad de mano de obra hipercalificada. Son fáciles de implementar y controlar, y no requieren capacitación específica; este es el caso del sistema de monitoreo en línea de Tractian.
Mantenimiento Predictivo / Predictive Maintenance
Al igual que el anterior, el mantenimiento predictivo se basa en las condiciones actuales del activo y se puede catalogar como un monitoreo de rutina, idealmente realizado en tiempo real.
Dicho monitoreo busca reducir las fallas y el desgaste de los equipos mediante la recolección, análisis de datos y mediciones de variables y parámetros de desempeño, analizando la condición operativa de los activos con base en estos resultados.

Algunas de las herramientas de mantenimiento más inteligentes y ventajosas de la actualidad se derivan de prácticas de mantenimiento predictivo, como el software de monitoreo en línea.
Con ellos, el gerente está al tanto de todo lo que sucede dentro y fuera del equipo, las 24 horas del día, y recibe diagnósticos y datos precisos que ayudan en la elaboración de un plan estratégico, con actividades correctivas y preventivas programadas de manera propositiva e inteligente. ., y no innecesaria y aleatoria.
Además del MPC, que, como dijimos anteriormente, está relacionado con la predicción y puede considerarse una rama del mantenimiento predictivo, existen dos vertientes dentro de este grupo: sensible y monitoreada.
Mantenimiento Predictivo Sensitivo – Rutas de Inspección (MPS) / Sensitive Maintenance
Más conocido como “sensible” o incluso “detective”, el MPS tiene como objetivo identificar la condición operativa de los activos físicos, y lo hace a través de rutas sensibles. Básicamente, esto significa que utiliza los cuatro sentidos del técnico (vista, oído, olfato y tacto) para evaluar los activos.
Es, por lo tanto, una actividad de diagnóstico que busca fallas potenciales, -una especie de investigación.
A primera vista, puede parecer simple, pero no se deje engañar. Es un trabajo que requiere mucha atención por parte de los profesionales hasta en los más mínimos detalles: sus ojos, oídos, nariz y tacto deben captar la mayor información posible durante las rutas de inspección y compararla con las condiciones ideales para cada activo.
Tal carácter investigativo nos lleva precisamente al mantenimiento detectivesco, que es una variación del mantenimiento predictivo sensitivo. Consiste en un conjunto de procesos cuyo fin es verificar los sistemas de protección acoplados a las máquinas, yendo más allá del monitoreo integral de los dispositivos.
Mantenimiento Predictiva Monitoreado (MPM) / Monitoring Predictive Maintenance
Cuando piensas en “mantenimiento predictivo”, lo que probablemente te viene a la mente es la definición de MPM. Esto se debe a que su objetivo es precisamente identificar la condición operativa de los activos físicos a través de mediciones constantes de parámetros técnicos cuantitativos, – como temperatura, vibración y ruido.
Además, es una actividad de diagnóstico que, como la sensitiva y la detectivesca, busca posibles fallas. Es decir, fallas funcionales que aún no han ocurrido, pero que ya comenzaron a dejar síntomas en los equipos. Los medios de investigación del MPM, sin embargo, no son los cuatro sentidos de los mantenedores, sino la recolección de datos constantemente 24/7.
Con un software de monitoreo en línea, basado en inteligencia artificial, IoT y ciencia de datos, se detectan e interpretan todas las variaciones y síntomas de fallas que manifiesta el equipo, lo que permite al gerente y al equipo saber exactamente qué, cuándo y dónde hacer para evitar problemas. en la operación.
Eso es exactamente lo que hace TRACTIAN. Después de estar conectados a los activos más críticos, los sensores IoT escuchan con mucha atención todo lo que dice la máquina (porque habla todo el tiempo). Esta información se analiza y se pone a disposición del equipo técnico en una plataforma intuitiva que va más allá y optimiza el trabajo del sector con diagnósticos precisos y conocimientos sobre las actividades de mantenimiento que se deben realizar. Todo esto en una sola herramienta.
Soluciones como esta son excelentes formas de hacer que el plan sea más estratégico y eficiente. Además de facilitar el trabajo del equipo y permitir que los operadores se preocupen por actividades más importantes. Tales tecnologías ayudan al gerente a definir qué acciones correctivas y preventivas se deben realizar, cuándo y dónde.
El sector se vuelve así mucho más rentable y beneficioso para la competitividad de la empresa, ya que no solo reduce significativamente la ocurrencia de fallas preocupantes y paradas de producción inesperadas, sino que también reduce los costos de mantenimiento.
Mantenimiento Prescriptivo (MPT) / Prescriptive Maintenance
Gracias al auge de tecnologías cada vez más avanzadas, el concepto de mantenimiento prescriptivo surgió en la era de la Industria 4.0. Su función es utilizar la inteligencia artificial para desarrollar soluciones para fallas potenciales identificables.
A diferencia del mantenimiento preventivo, el prescriptivo no está atado a un cronograma enfocado en fallas comunes. Y frente al predictivo, va más allá, ya que no solo predice con precisión lo que sucederá, sino que también sugiere intervenciones en función de las posibilidades calculadas a partir de los datos analizados.
Todo esto nos recuerda lo que ya vimos en el tema anterior sobre el mantenimiento predictivo monitoreado. Allá usamos como ejemplo la solución TRACTIAN, que también está relacionada con MPT.
El sistema de monitoreo en línea se basa en prácticas de mantenimiento predictivo y prescriptivo, siendo este último posible gracias al cruce de datos del historial operativo y al uso de inteligencia artificial sobre la información recopilada, lo que permite al equipo de mantenimiento saber qué hacer cuando se detecta alguna anomalía.

Mantenimiento de Soporte (MAP) / Support Maintenance
El último tipo de mantenimiento está representado por actividades que no forman parte de la rutina de los talleres especializados y que trabajan para la mejora física de los activos.
En este grupo se incluyen las pequeñas reformas, reparaciones y modificaciones que son necesarias en las instalaciones y son realizadas directamente por los equipos de mantenimiento.
La clave es el uso correcto de las estrategias de mantenimiento
Hay muchas discusiones sobre cuáles son las mejores definiciones y términos para cada tipo de mantenimiento, pero hay pocas soluciones que realmente mejoren el sector de mantenimiento en América latina.
Ahora que conoces los principales tipos de mantenimiento, sus diferencias, formas de aplicación y las herramientas más eficaces, estás un paso por delante de la competencia en el proceso de ponerlos en práctica en el plan de mantenimiento, repartiendo actividades y porcentajes de actuación de forma estratégica. . Y la mejor opción es siempre priorizar la tecnología y sus herramientas inteligentes para anticiparse a los problemas y tener más control sobre las acciones que habrá que realizar sobre la maquinaria.
Todos los tipos de mantenimiento tienen ventajas y desventajas, de ahí la importancia de integrarlos y hacer que uno complemente la falta del otro. Después de todo, desde las actividades correctivas hasta las prescriptivas, todas las prácticas tienen el mismo objetivo: mejorar y mantener la disponibilidad y confiabilidad de los activos.
Para asegurarte de que el objetivo se alcance con éxito, recuerda siempre que la tecnología es el mejor amigo del gestor 4.0, que no solo quiere que las máquinas funcionen, sino mantenerlas fiables y disponibles. Si quieres unirte a este grupo y transformar los resultados del mantenimiento en tu industria, cuenta con TRACTIAN.