Much is discussed about different types of maintenance and how they’ve evolved over time. But one thing is crystal clear: technology plays a pivotal role in giving rise to new categories of maintenance. And the freshest example of this phenomenon is Artificial Intelligence Assisted Maintenance.
AI has been a hot topic in industrial and manufacturing circles over the past few years. What used to feel remote from the everyday lives of maintenance experts and shop floor professionals has now seamlessly integrated into the routines of countless factories and a myriad of individuals across the globe.
As the concept gains increasing popularity year by year, numerous extremely intelligent and advanced solutions have emerged in the industrial sector, thereby strengthening the notion of AI-assisted Maintenance.
There are some well known types of maintenance on the market today: reactive, preventive, predictive, and prescriptive for example. The purpose of this article is to finally add Assisted Maintenance to the list.
The main maintenance types are:
- Reactive Maintenance: also known as corrective maintenance, this approach is used only after a failure or an inssue has already affected the equipment or machine. The intervention is carried out to restore functionality, though it can lead to unplanned downtime and unforeseen expenses.
- Preventive Maintenance: consists of carrying out periodic and scheduled maintenance, regardless of current equipment condition. The objective is to avoid breakdowns by changing parts and components before problems come to the surface, seeking to reduce the risk of unplanned downtime.
- Predictive Maintenance: uses data and analytics to anticipate potential failures based on key performance indicators (KPIs) and trends. This way, corrective actions can be taken before the failure actually takes place.
- Prescriptive Maintenance: Beyond predictive maintenance, the prescriptive approach takes it one step further by furnishing comprehensive recommendations for preventive actions, thus sidestepping future problems.
- Assisted Maintenance: in addition to prescribing actions, assisted maintenance technology offers accurate diagnoses based on data collected online, using prescriptive comparison. In other words, it cross-references a vast amount of information from numerous machines, manufacturer manuals, and data input from online monitoring sensors.
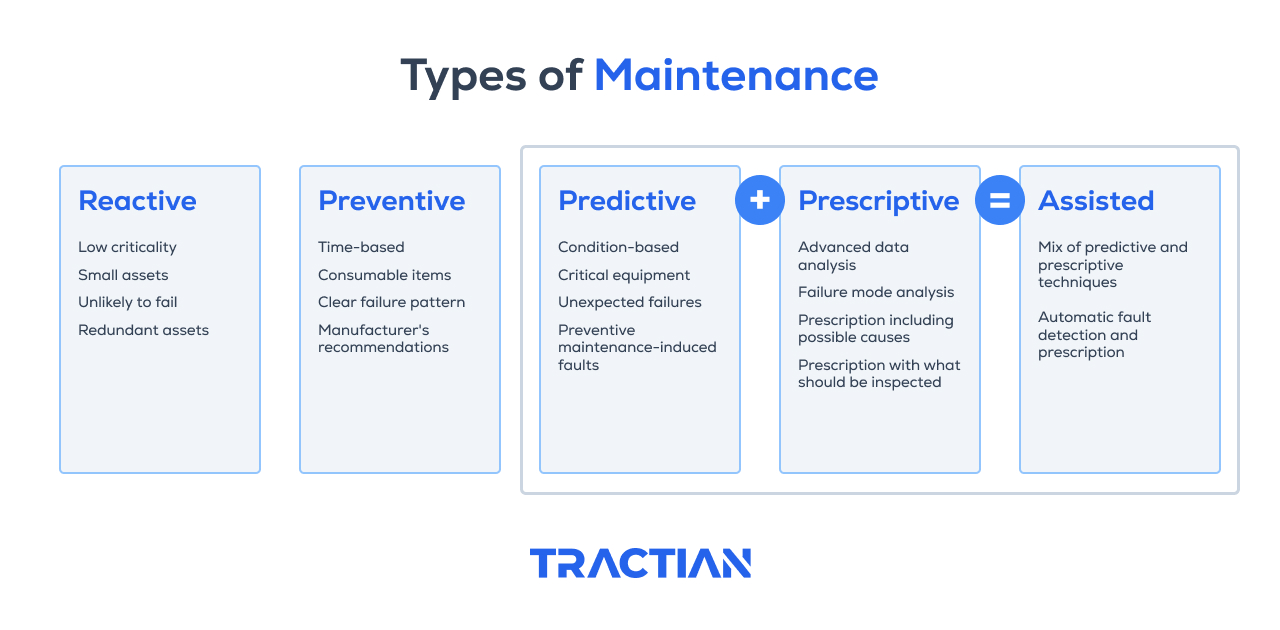
AI-assisted Maintenance = Prescriptive + Predictive + AI
The assisted maintenance category is the combination of prescriptive and predictive techniques, positioning itself at the forefront of risk management. Within this category, we find subcategories:
- AI Assisted Maintenance;
- Augmented Reality (AR) Assisted Maintenance;
- Virtual Reality (VR) Assisted Maintenance;
- Maintenance Assisted by Industrial Internet of Things (IIoT);
- CMMS/EAM Assisted Maintenance;
- Maintenance Assisted by Additive Manufacturing (EM);
- 3D Technology Assisted Maintenance
AI-assisted Maintenance represents the integration of Artificial Intelligence with other advanced technologies, such as online condition monitoring and the use of maintenance management software (CMMS/EAM) to optimize processes.
The synergy of online condition monitoring and the CMMS/EAM is the core of this approach, providing a live perspective on asset performance and streamlining maintenance planning and scheduling. Uninterrupted monitoring facilitates instantaneous data access, a pivotal factor in promptly detecting shifts in machine behavior. CMMS/EAM on the other hand, acts as a centralized hub for managing maintenance-related information such as intervention history, preventive plans, and performance logs.
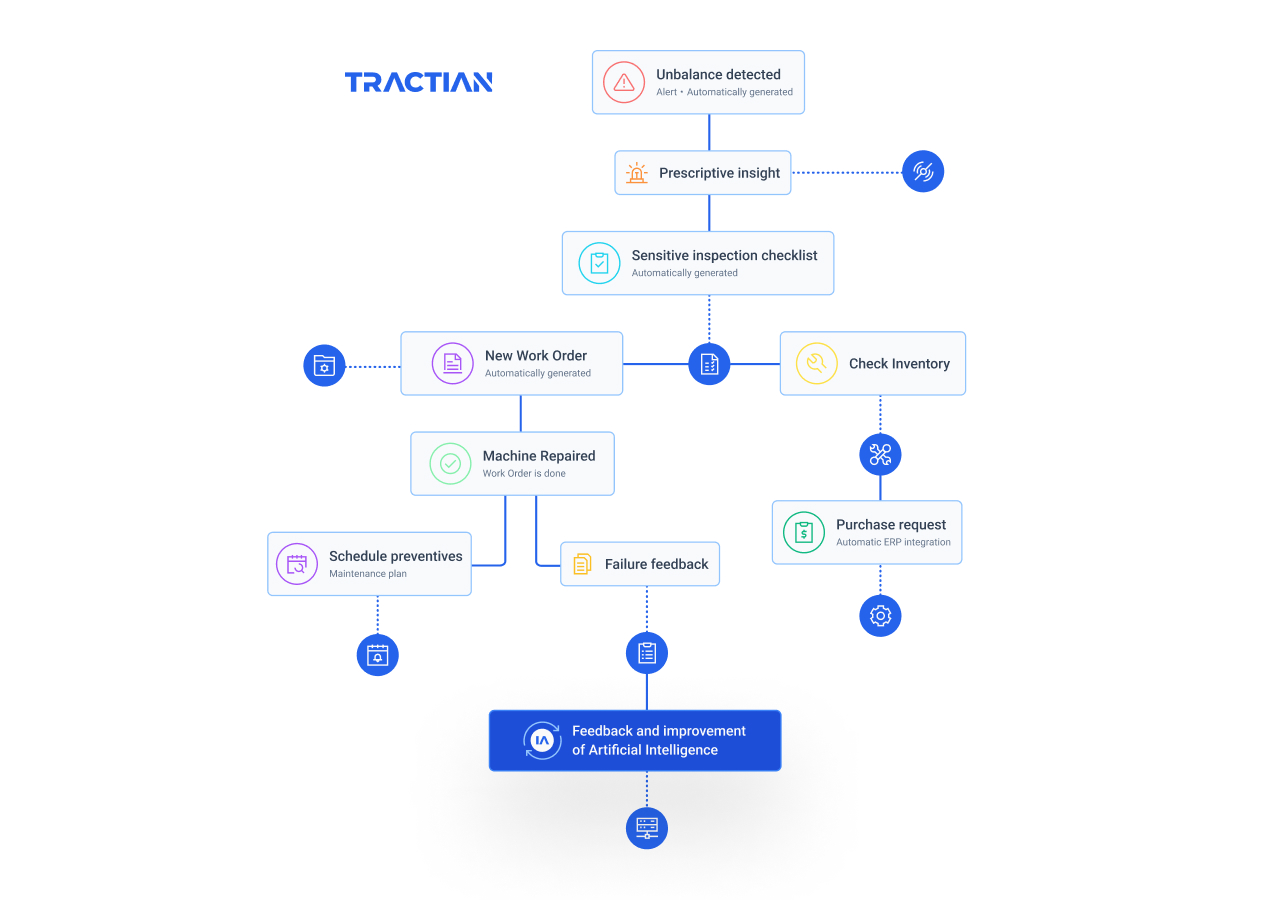
In addition to prescribing, AI-assisted Maintenance suggests a diagnosis using prescriptive comparison. This evolution is possible thanks to the AI’s ability to process and analyze large volumes of information from several sources.
By meticulously cross-referencing data from thousands of machines, manufacturer manuals, and insights gleaned from online condition monitoring sensors, AI can deliver actionable prognoses, fortified by robust technical underpinnings. It can identify patterns, trends, and even subtle anomalies, constituting a paramount innovation in industrial maintenance.
This brings what we know as smart maintenance solutions onto the shop floor, which is something that conventional methods would struggle to achieve. Yet, through the utilization of prescriptive benchmarking, AI becomes an indispensable ally for maintenance workers and operational leaders, providing an all-encompassing view of the condition of machinery and equipment.
The key element to ensure the assertiveness of this approach is human participation in the process, or human-in-the-loop feedback. Despite the analytical capacity of AI, human intervention is fundamental to provide the context, expertise, and critical judgment that can complement the computational power of AI for maintenance.
This sophisticated approach empowers technicians with a dependable and meticulous prognosis regarding the requisite actions for sustaining seamless operations. This, in turn, guarantees reliability and prolongs the lifecycle of industrial assets.
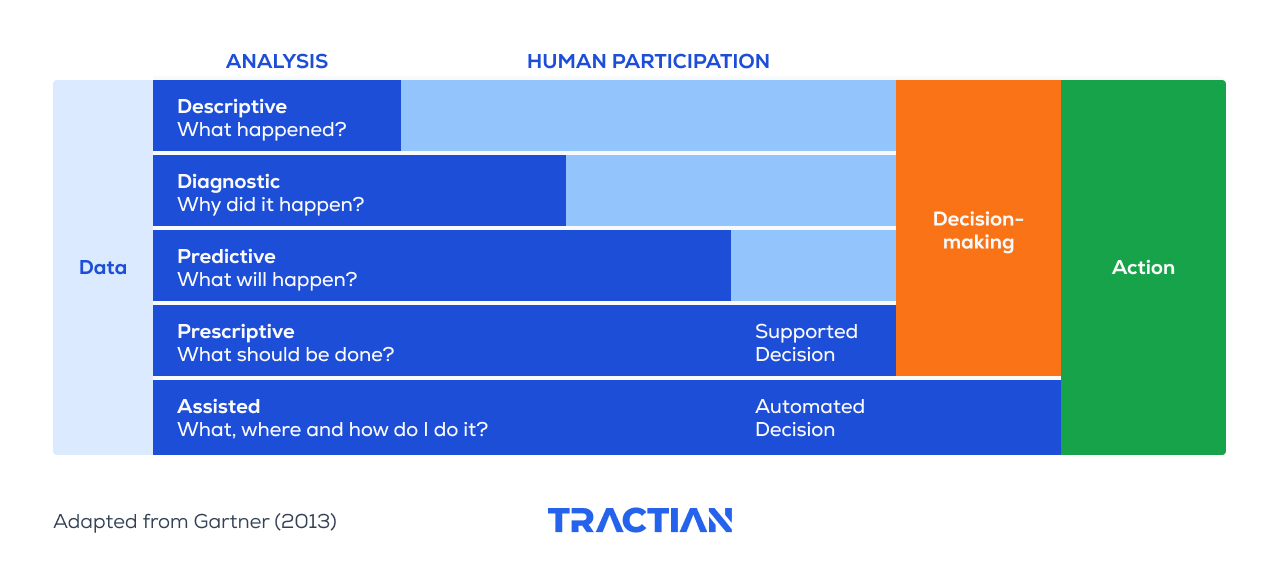
The constant analysis of real-time data facilitated by AI initiates a virtuous cycle of continuous learning and improvement. Each new diagnosis and prognosis feeds the system with valuable information, further refining its ability to identify potential failures and improving its assertiveness over time.
Through Artificial Intelligence Assisted Maintenance, enterprises can attain unparalleled levels of availability and productivity. The capability to anticipate and avert issues prior to their emergence, combined with diminished operational expenses, positions this approach as a distinctive competitive advantage across diverse industries.
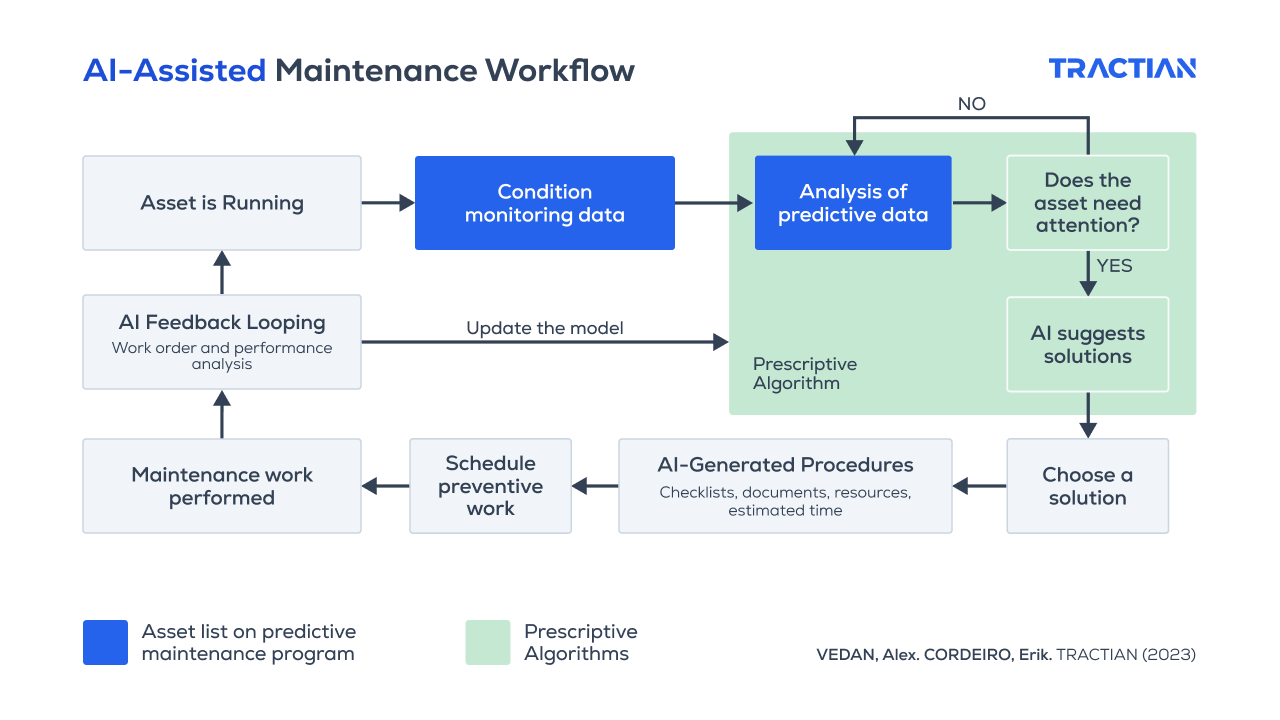
AI-assisted Maintenance Applications
Assisted maintenance is now a reality in industries and manufacturing facilities worldwide. The aeronautics sector is a successful example: advanced floorplans systems monitor equipment condition in real time.
A comprehensive signal derived from the production line vividly illustrates the status of each equipment piece. In the event of problems or anomalies, the system promptly identifies and notifies operators through illuminated indicators. Faulty equipment is signaled with either red or yellow lights, contingent upon the gravity of the issue.
By enabling remote, mobile-first access to data directly on cell phones, maintenance experts benefit from enhanced flexibility and mobility. They can instantly assess equipment conditions, scrutinize faults, and acquire comprehensive insights into the root causes of issues in real time. Consequently, operational leaders and decision-makers are empowered to respond swiftly, conserving both time and resources and thereby amplifying overall productivity.
AI automatically generates detailed reports encompassing spectral analysis, pinpointing the failure modes responsible for heightened vibrations in particular equipment, such as unbalances, lubrication problems, or bearing wear. This capacity facilitates the estimation of component longevity, drawing upon measurement data obtained from analogous assets.
For a practical example, suppose a centrifugal water recirculation pump has high vibration levels in all directions. Utilizing spectral analysis, AI adeptly identifies a high-frequency random noise—a distinct indicator of cavitation, a phenomenon well-recognized in such contexts.
AI will then automatically generate a prescriptive report that details the failure mode, severity, possible causes, and what maintainers should inspect.
Based on these results, the maintenance management system (CMMS/EAM) can automatically generate Work Orders containing all the necessary information for execution, such as specific procedures for each failure, materials, tools, documents, and manuals. Managers and supervisors can then direct their teams quickly to the required activities and facilitating collaborative troubleshooting to resolve the issue.
When analyzing that specific pump’s data and other similar assets, AI identifies changes in the pump suction pressure. This revelation points to the fact that the underlying trigger of the cavitation issue isn’t attributed to pump malfunction, but rather, it originates from a different stage within the process.
With the Work Order already charted out by the maintenance team, technicians are directed to investigate the preceding phases of the process, rather than focusing solely on the pump. This strategic shift leads to enhanced productivity and expeditious execution of inspections and repairs, underscoring the agility and efficiency gained through this approach.
Another example is AI’s ability to recommend future actions, such as ascertaining the prime moment for asset replacement when maintenance expenses surpass the asset’s total replacement value. By incessantly monitoring these metrics, AI discerns the opportune juncture and triggers an alert, signifying that the time has arrived for replacement.
When using IoT sensors for energy management, AI constantly monitors energy indicators, analyzes the power factor, issues alerts of increased consumption, and generates automatic reports.
Suppose that production needs an extra shift of work to complete the weekly demand, AI can indicate the ideal times and places to carry out the activities taking into account the cost in relation to the energy rates, evaluating the demand and the energy efficiency of the machines that will be used.
The costs of installing and maintaining these systems have become more affordable due to technological advancement and lower prices for sensors and other components.
In essence, Artificial Intelligence Assisted Maintenance heralds a revolutionary paradigm shift in our approach to industrial maintenance. By harmonizing cutting-edge technology with expert technical insight, it delivers precise diagnoses, reliable prognoses, and exact preventive measures, thereby ensuring operational excellence and unwavering reliability across industries.
This represents a substantial stride towards optimization, expense curtailment, and elevated process dependability, propelling industries towards a future defined by elevated performance and unceasing innovation.