Maintenance used to be seen as something whose purpose was only to fix what broke down.
As time went by, the search for increased profit and production efficiency grew. And, in order for operators to be able to meet these demands, the number of machines had to increase.
Because of this, methods were created to make the maintenance management of a company more effective, and one of them is the Maintenance Planning and Control (MPC).
To help you master this subject, we have prepared the following guide that will teach you everything you need to know about MPC. We hope you enjoy it!
What is Maintenance Planning and Control?
The Maintenance Planning and Control practice contributes to a more assertive management through the adequate application of maintenance techniques.
This includes analyzing the assets’ current condition and elaborating strategies for the processes, besides evaluating costs with less impact on production by reducing downtime, failures, and production bottlenecks.
Thus, MCP in maintenance increases the availability, reliability, and controllability of procedures.
The goal will always be to make the asset available in the best conditions for production, with effective maintenance practices and strategies based on the equipment’s history, always seeking to improve the operation and ensure proper functioning.
What is Maintenance Planning and Control used for?
MPC ensures the usability, safety, and reliability of assets that are essential to the operation. In other words, the practice ensures that machines work properly.
It is also responsible for defining the best strategies to allocate the department’s resources. In this way, it organizes the manpower, time, and money available.
In addition, MPC is essential for the prevention of work accidents, since it reduces the occurrence of breakdowns and failures that can put employees at risk.
Thus, we can highlight as the main objectives of MPC:
- Reduce failures to promote the availability of plant and machinery;
- Promote the efficient use of equipment;
- Minimize equipment wear, extending its useful life;
- Raise the team’s productivity;
- Contain losses due to stops in production;
- Ensure the use of essential items for emergencies;
- Prevent work accidents and occupational diseases;
- Minimize the total cost of maintenance;
- Improve product quality for the final consumer;
- Raise the reliability and availability of infrastructure.
The importance of MPC
It is important to have a very well structured management system so that companies can achieve the best performance, reduce waste, and increase production.
Maintenance Planning and Control aims to optimize this management, increasing the predictability and availability of the machines.
It also helps with the decision making process and in finding information that can solve problems.
The advantages of using MPC
Among the gains generated by MPC, we can highlight:
- Time optimization;
- Increase in productivity;
- Improvement of strategies;
- Greater availability of equipment.
With the information provided for decision making, it is possible to reduce the exaggerated consumption and waste of resources.
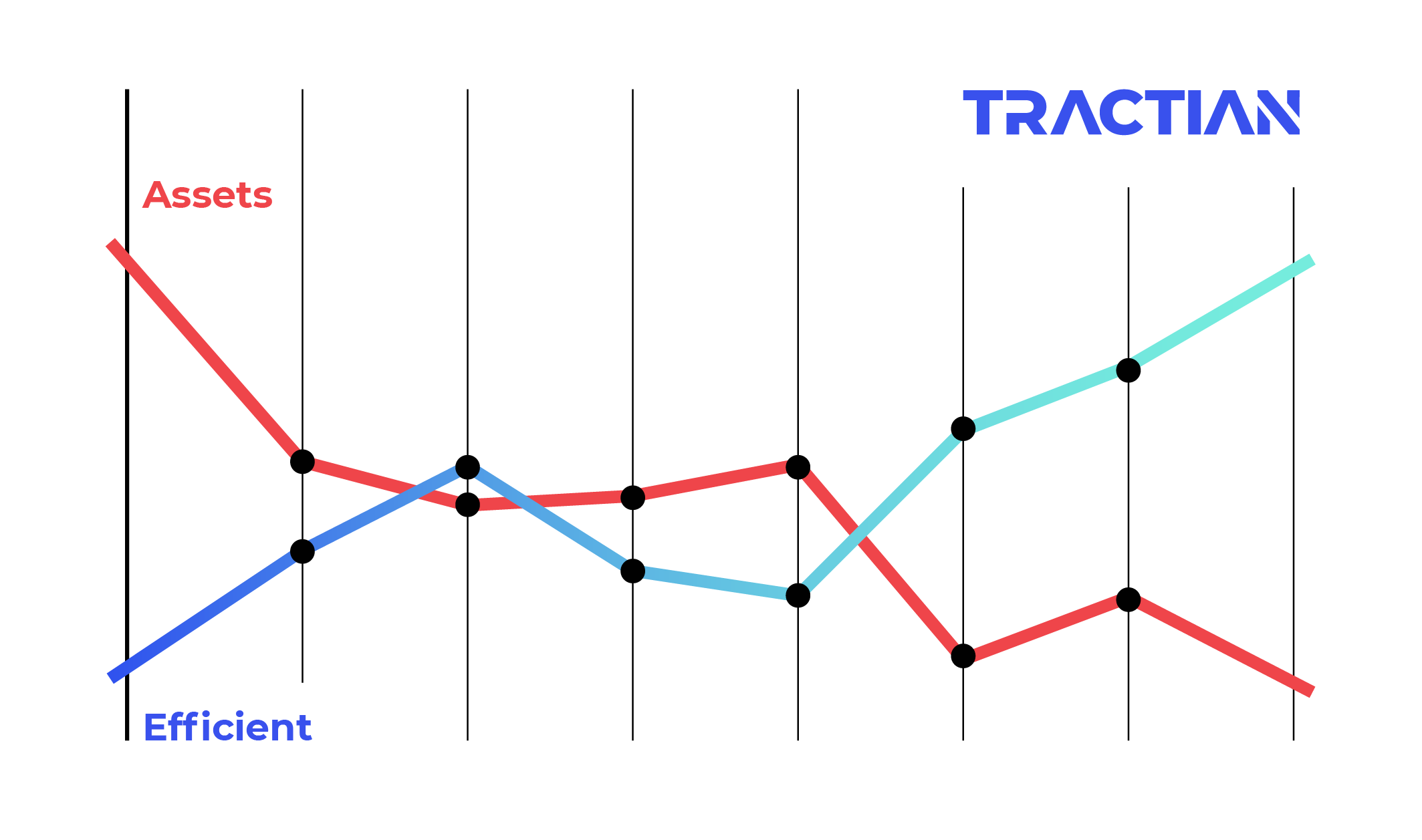
What maintenance strategies are applied by MPC?
The use of the correct maintenance strategy guarantees the adequate functioning of the asset, besides proposing improvements that avoid future failures.
Because it works with process optimization and planning, Maintenance Planning and Control must be applied to preventive and predictive maintenance, which is why it is essential that they are present in the plan.
The MPC phases
Maintenance Planning and Control can be divided into three main phases: planning, scheduling, and control. Understanding them is essential to know the importance in structuring and applying the actions.
Each one of them has its own form of management and execution, but all converge to a common objective: to ensure the asset reliability and availability.
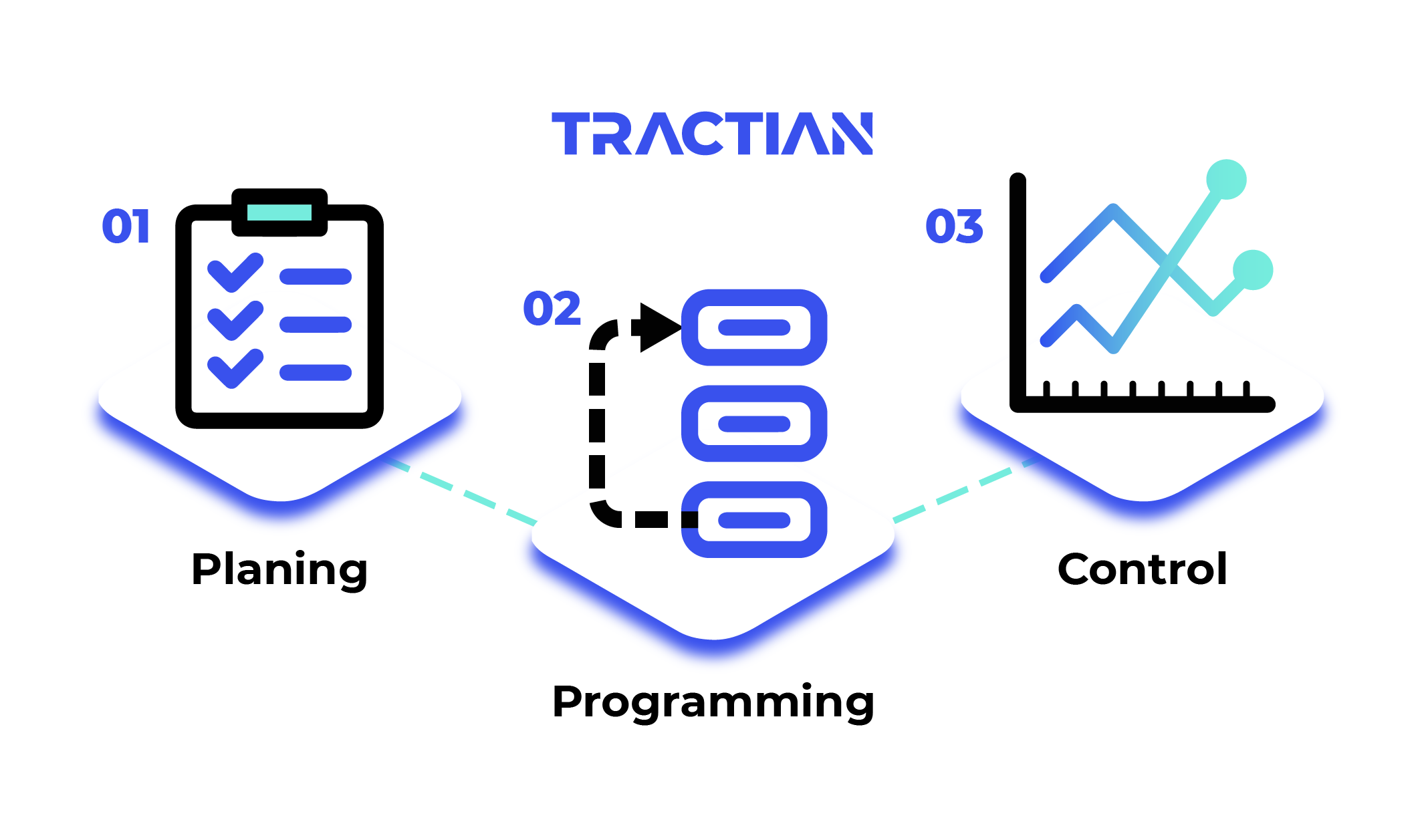
1st step – Planning
In this phase, the team must evaluate each asset, its criticality and which strategies will be applied, considering all the necessary aspects for the execution of the scheduled activity.
The manager must manage all the resources involved in the operation: meetings, training, labor, stock, and materials. Then, it is fundamental to foresee all the operation’s needs in order to avoid future problems between the established goals and the expected results.
It is also necessary to describe in detail each of your maintenance plans, considering the minimization of costs related to maintenance and the increase of the asset availability index.
2nd step – Programming
The second step consists in scheduling the activities that were planned for the necessary interventions to be done, which can happen weekly, monthly or annually.
Remember that the established deadlines must always be in accordance with the criteria that were aligned in the previous phase.
The points to be considered during the realization of the MPC are:
- Activities level of urgency;
- Availability of resources;
- Feasibility of stops;
- Occurrences chronology.
Organize the teams, set up schedules, facilitate communication, and establish who will be responsible for each activity. Make sure they are all properly trained, qualified and skilled to perform the tasks.
Step 3 – Control
In the third and last step, it is necessary to monitor and analyze the whole process executed in the first and second steps by means of metrics and maintenance indicators.
These indicators must be established according to what the company considers relevant to the process and what it wants to measure, so that they can be compared over time.
The three key points of MPC
There are three key factors for a good MPC. They are:
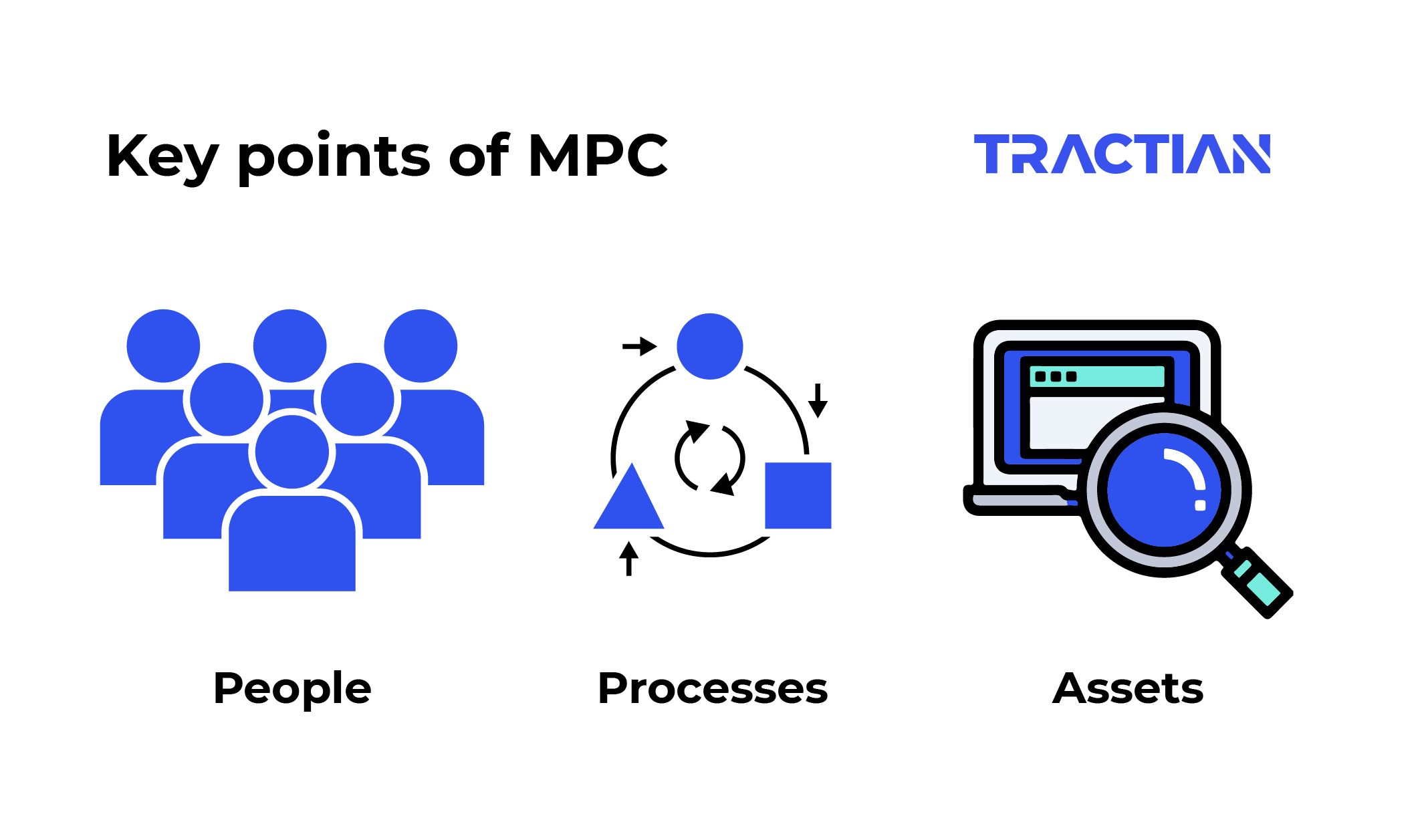
People: for processes to get better, the manager should engage and motivate workers, after all, they are in all spheres of the company, from execution to management.
Processes: The manager must be attentive to the processes, observing if there are optimizations to be made and eliminating waste.
Assets: all MPC activities must be focused on the assets, planning well the resources that will be used.
Applying MPC to the maintenance routine
Once you know all the information about MPC, it is time to put it into practice.
Remember: there is no single step-by-step, because every industry has its own procedures.
However, we have listed six steps that can be followed in any situation:
Develop a schedule
Gather information about the production lines and draw up a schedule. Know exactly what resources are available, the production capacity, and what state the assets are in.
Attention to downtime
Stipulate dates for machine shutdowns and repairs. For this step, you can rely on online monitoring software, capable of detecting when an asset will stop, allowing your team to perform maintenance before the failure affects the production line.
Describe the maintenance processes
Detail all the activities that the maintenance team will perform. Here, maintenance management software can also be a great ally.
You can issue Work Orders online with details of the activity, including the name of the person responsible for that inspection and the deadline for it to be executed, as well as following the activity progress in real time.
Plan resources
Assess what is already in stock and forecast what will be needed for the job. Thus, it will be possible to schedule purchases, manage the stock, and, if necessary, hire people or outsource to other companies.
Follow up the process
At this stage, it is fundamental to follow up the maintenance, evaluating if what was planned is being executed.
Here you can also count on the help of online monitoring, through sensors that use the mobile network to collect data from the assets in real time.
Every day of the week, these devices record essential information from the assets, such as vibration, temperature, hour meter, and energy consumption. Through this data, the online monitoring system identifies misalignment, unbalance, mechanical play, wear, cavitation, and other problems.
Use the appropriate technology
A good method for applying MPC is to rely on a tool that allows you to centralize all industrial processes, such as TracOS™, TRACTIAN’s asset management software.
It combines online monitoring, asset management, and OEE (Overall Operations Effectiveness), besides facilitating executions such as planning, operational performance, control, and productivity.
On the platform, the manager has access to metrics, standardized Work Orders, view over the asset tree, inventory and procedures.
With detailed information about your assets, you will know exactly when the next component change should take place, prioritize a certain activity, or simply track the status of the equipment.
Having this information centralized also allows for management reporting.
The use of more complete tools is, without a doubt, a differential that makes the company stand out.
Count on solutions that gather all these data in a single place and integrate the Maintenance Planning and Control results, ensuring that they are achieved in an assertive, fast and efficient way.
Contact the TRACTIAN team and find out how our solution can enhance your MPC and facilitate the routine of your maintenance team.