Eye on Failure is a series of maintenance stories about professionals who implemented our solution, eliminated failures and unpredicted downtime in machines. To know other cases, such as Embraer, AmstedMaxion and Ahlstrom Munksjo, visit our blog.
The company
Corteva Agriscience is a multinational company, the result of the merger of Dow Chemical and DuPont, both agricultural businesses. The company operates in three pillars: seeds, crop protection and digital agriculture, so that producers can maximize their productivity and profitability.
Its purpose is to improve the lives of those who produce and those who consume, ensuring the progress of the next generations. Corteva’s team has decades of experience in the agricultural industry focused on promoting a performance-based culture. In addition to that, the company is committed to sustainable agricultural practices for the benefit of producers and consumers on a global level.
Currently, Corteva has 4 thousand researchers, 150 research centers in 25 countries, and is present in six continents.
A history of growth
Fernando Miron Cortes Vicente is a Chemical Engineer and started at the company when it was still Dow Chemical, as a Trainee.
He became an Improvement Engineer and worked in different sectors of the company, such as Reliability and Production Engineering, which is the position he worked in for the longest time.
I started my career here and went through the transition from Dow Chemical to Corteva. From the internship until today, I’ve been in the same plant for 8 and a half years.
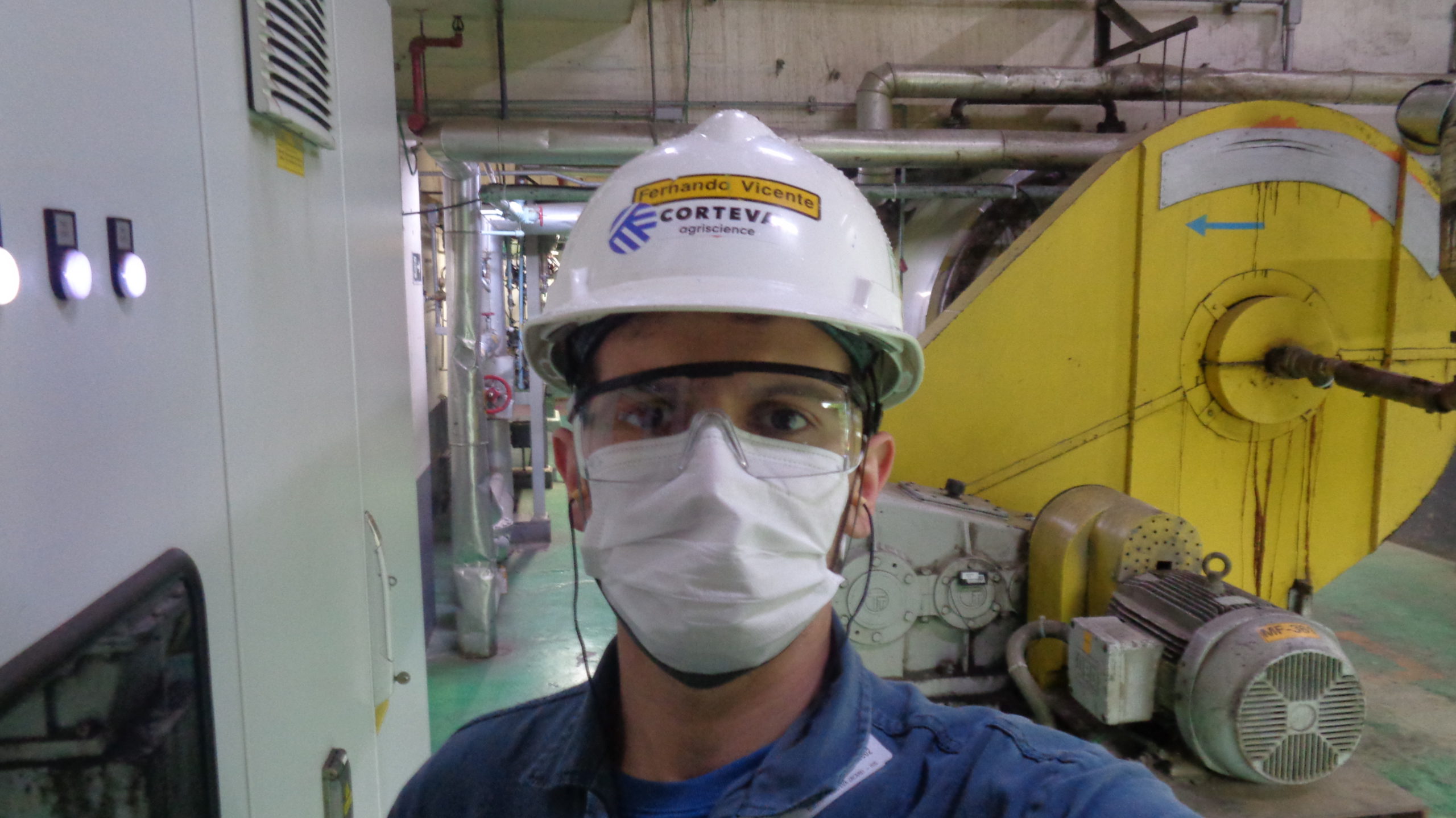
First contact with TRACTIAN’s solution
Having been a Maintenance Leader for a year and a half, Fernando says that his unit is not large, but it has a high production capacity.
The production process includes pastes with high solid content and encrusting characteristics. This requires good discipline of periodic cleaning to ensure a good equipment performance.
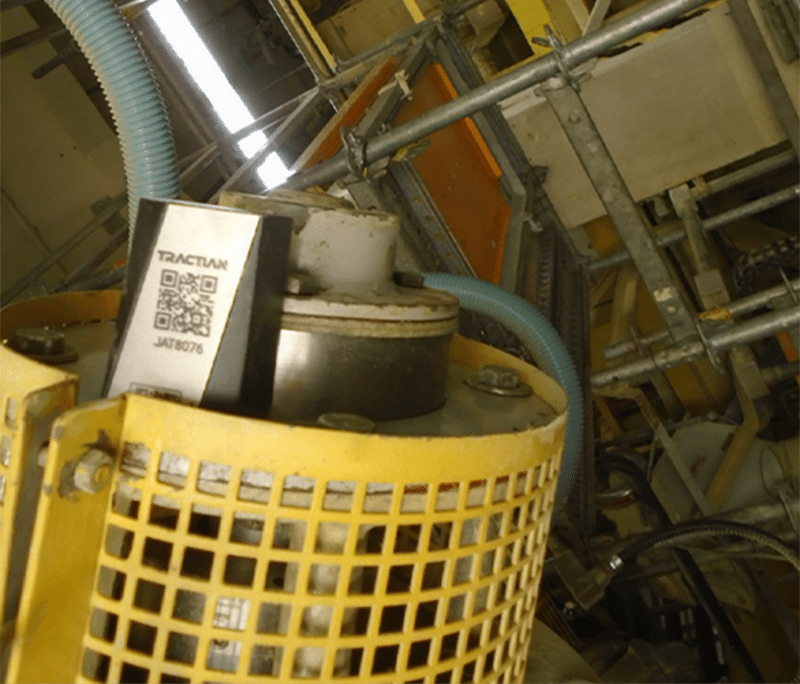
The company had a predictive strategy that performs vibration analysis with a certain frequency, depending on the criticality of the equipment and the failure rate.
Because the plant operates 24 hours a day, 7 days a week, production interruptions are not frequent and are always for maintenance or cleaning. Most of the time, even with monthly predictive inspections, some failures or anomalous behaviors were not identified, besides the lack of asset backup in case of malfunctions.
I found TRACTIAN through a colleague of mine, he gave me the contact information, and I started keeping up with the company. But before TRACTIAN, it was basically that, we had a good preventive and predictive plan, but we still didn’t have online monitoring.
First insights detected
Although the maintenance team had only been operating with TRACTIAN sensors for a few months, several alerts were already sent by the platform.
The monitored assets were chosen based on criticality, that is, the most important machines for Corteva’s production line.
To learn how to choose the right assets and apply online monitoring
We made a selection and there were up to 7 or 8 assets that really needed it, but we got 10 sensors in order to observe other equipment that we were curious about.
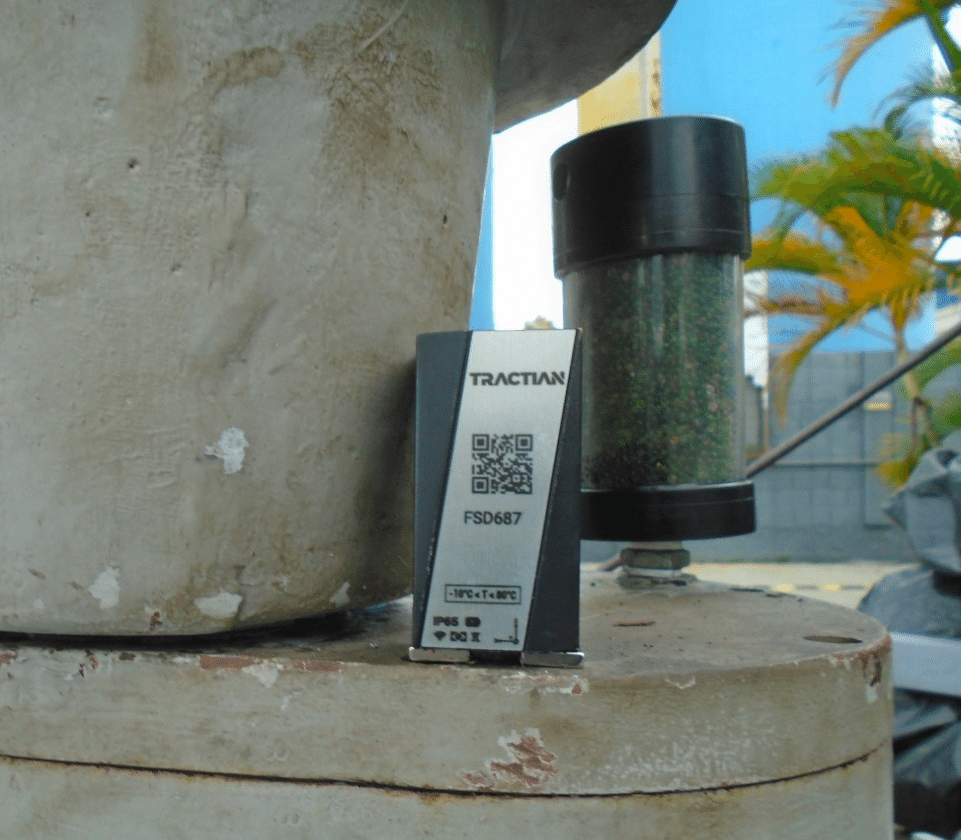
Fernando reports that the industry has some assets that really needed to be monitored by the sensors. Among them, two pumps where the failure rate was very high, with an oscillating vibration pattern. And a tag exhaust fan: B270, with a fouling issue that unbalances over time, due to the product that sticks to the motor.
We were having a planned shutdown only a week before the vibration rates went too high and the sensor picked it up. And the most curious thing is that we did the vibration analysis sample a week before the insight was issued, and had we waited a month, we might not have noticed it. You notice noise in the area but without the data, there is no way to confirm it.
Online monitoring has helped in detecting abnormal vibration before a functional failure or even a breakdown.
The sensor has been useful for decision-making, to know whether we stop an operation or not, to see how far into the future the equipment can go on operating. But now we have data to know how much of that dirt is affecting the vibration of the equipment.
In addition to the change in vibration profile, within the same period, the sensor also detected an unbalance and a misalignment.
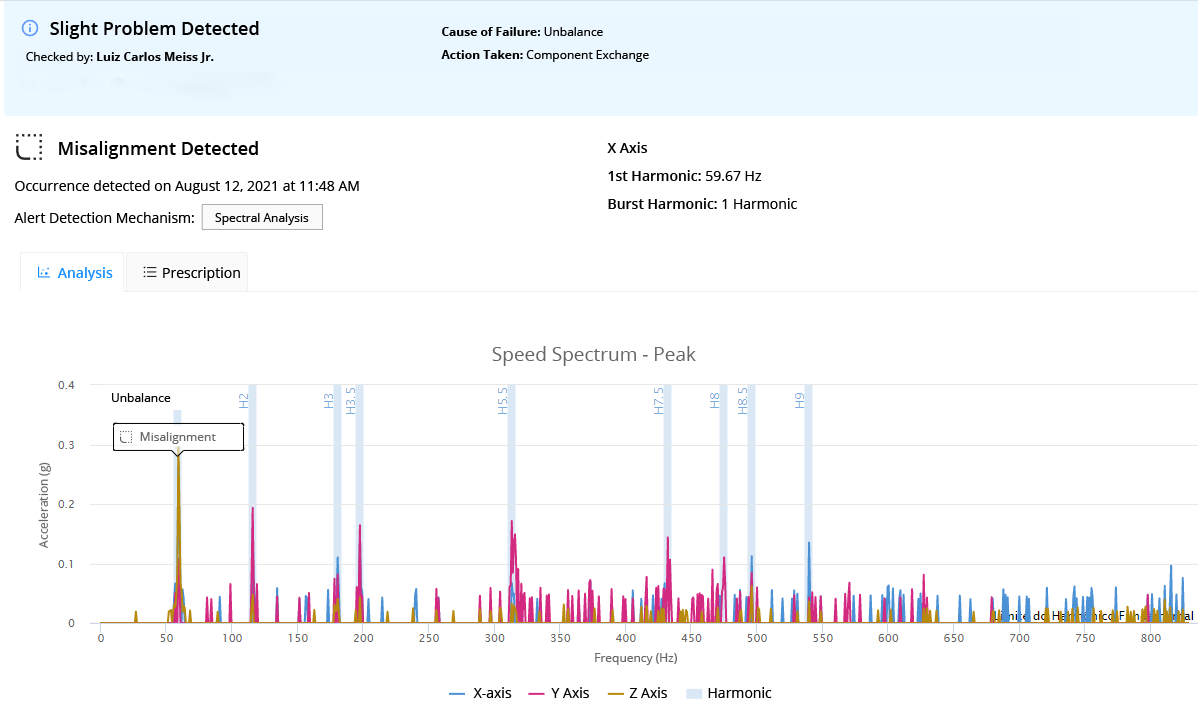
In this insight generated by the platform, an unbalance in the 1st harmonic (H1) was identified, where the established limit was exceeded. The value of H1 is very high when compared to the historical average of the period. After the alert, preventive maintenance was done and, as shown in the image below, the RMS speed levels went back below the ISO Critical Zone limit.
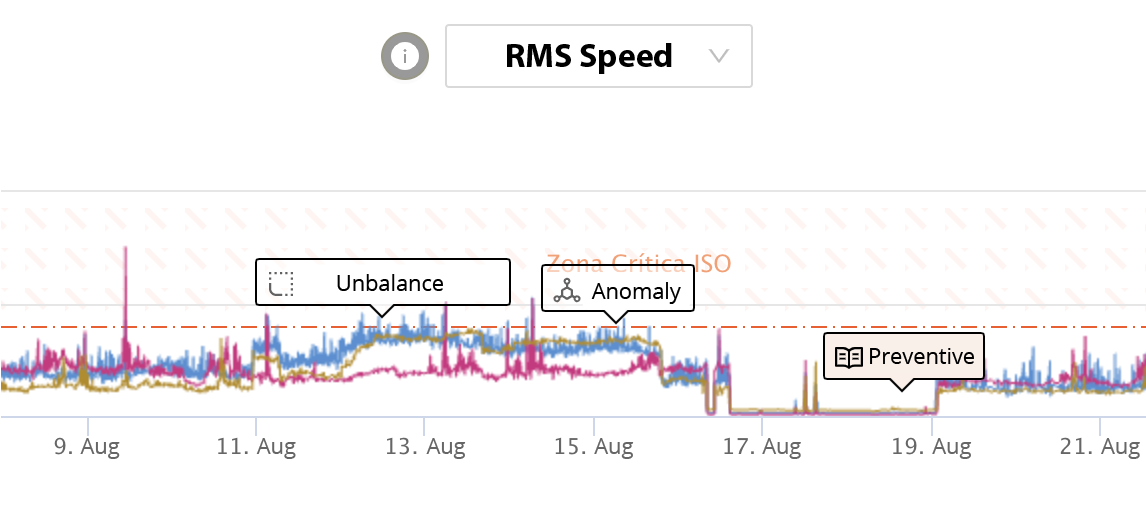
The platform also detected a misalignment, which is when the value of Harmonic 2 (H2) is high compared to Harmonic 1. In Corteva’s case, H2 was 30% higher than H1.
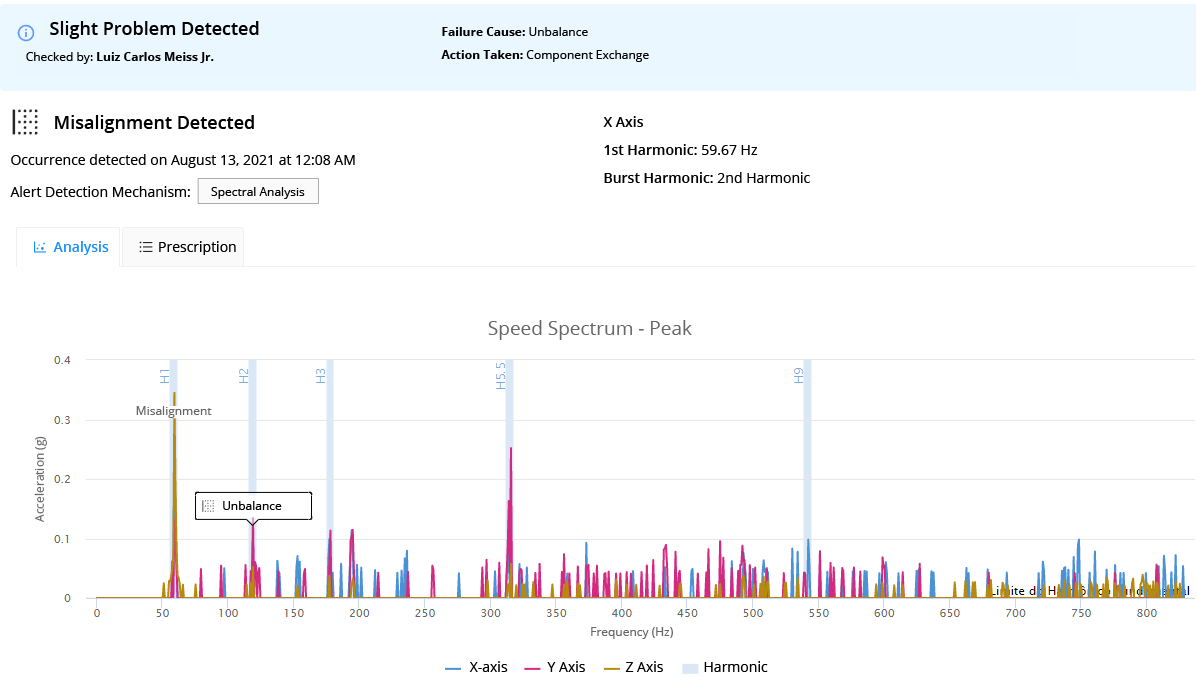
Both alerts avoided huge losses. In one of them, the insight issued managed to avoid a breakdown that could have cost between US$4,000 and US$12,000.
What sets TRACTIAN apart
For Fernando, having access to vibration, acceleration and speed profiles, and not only to global trends, is one of TRACTIAN’s greatest perks.
One of the best aspects of the platform is the ease of communication. The insights go straight to your cell phone, so you can answer them and solve the problem right away.
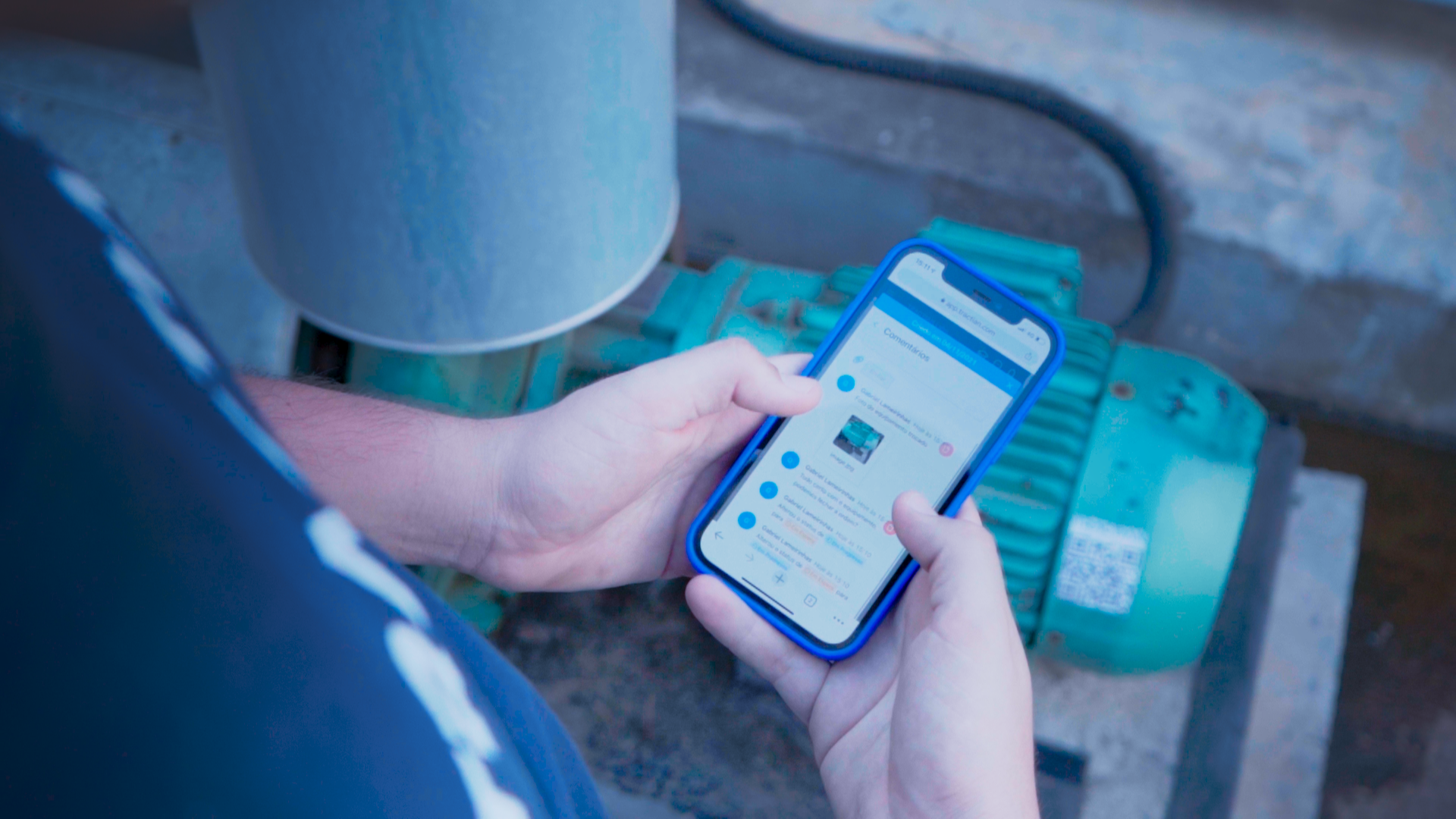
The engineer also highlights that the interface available is very intuitive to be managed, filled out, and handled.
The ease of installation is also another point that I like to highlight. The fact that you don’t have to install a modem or anything like that is a great advantage. I just need an outlet with electrical power and I can perform the analyses.
The company has some critical equipment that, if stopped, would affect the whole production plan. Online monitoring was able to identify 3 anomalies that had a high potential of evolution and would probably result in the failure of the equipment after a few hours.
Identifying these failures early on allowed us to make a repair that was simple, cheap, and had almost no impact on production.
To improve the practicality and reliability of your company’s maintenance, just like Fernando, contact one of our specialists and retire conventional maintenance.