As a maintenance professional it’s important to be knowledgeable of terms in the industry. It’s even more essential when the difference between two things could mean increased cost or less efficiency. But, is there a difference between maintenance and repair?
Repair and maintenance are often used interchangeably throughout the industry, but they have key differences that set them apart.
Knowing these differences is crucial to running not only a successful production, but a successful maintenance department and company.
What Is Maintenance?
In the industry, maintenance is how assets are preserved or protected. It’s how maintenance teams keep assets running at their highest levels today, and in the future.
Most maintenance teams have two goals:
- To make machines as reliable as possible
- To keep machines available and operating for as long as possible
Utilizing maintenance – especially the right types – makes those goals a real possibility!
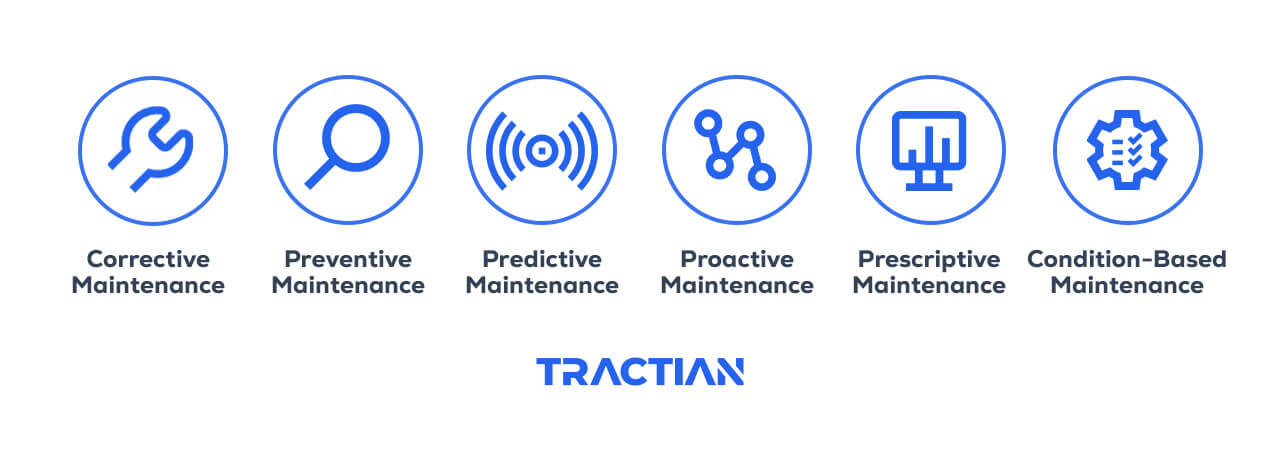
Types of Maintenance
There are multiple types of maintenance teams can implement, but not every strategy is right for each company. All it takes is a little analysis of critical assets, and maintainers can find the best way to implement one or more maintenance strategies to improve reliability and profitability in their company.
All types of maintenance lie within two categories, which may help in differentiating maintenance vs repair:
- Risk-based maintenance monitors assets, analyzing those that pose the greatest risk to production if failure is to happen. It says that maintenance resources should go to these critical assets first. Corrective and reactive maintenance fall under this category.
- Reliability centered maintenance sets safe minimum levels of asset upkeep, focusing on the optimization of maintenance programs. Preventive, predictive, and proactive maintenance strategies fall under this category.
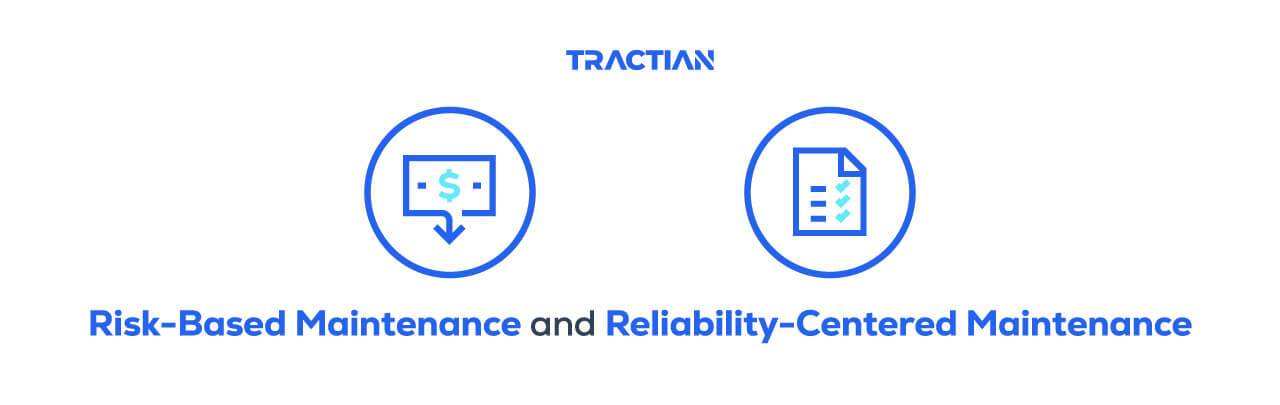
For more on how to choose the right maintenance strategy, check out this article.
What Is a Repair?
The definition of repair is to fix or mend something. In the maintenance industry, repairs are done on assets either before, during, or after a breakdown.
There are two types of failure that repairs set out to fix, partial and complete.
A partial failure is when equipment functionally operates, but can only partially do its job. This includes issues like wear, corrosion, and inadequate lubrication. Partial failures are less serious than complete failures, usually causing the degradation of assets instead of the complete loss of service.
They’re hard to detect, and can take a period of time to be found. Many maintenance teams perform corrective maintenance on partial failures to return the asset to working condition.
On the contrary, complete failures are easy to recognize because the asset is practically unusable. Common complete failures include vessel, pipe, or valve ruptures, engine or turbine propeller breakdowns, boiler or HVAC malfunctions, or bearing failures.
Partial breakdowns are often difficult to find and can cause issues for long periods of time. Complete failures can be quickly identified or repaired – limiting the impact of the failure.
To answer the age old question, yes, there is a difference between repair and maintenance. Repairs restore asset functionality after downtime to minimize loss, and maintenance preserves functionality to prevent unplanned downtime.
Repair and Maintenance Expense
Because of their unplanned nature, cost incurred by repairs is more than maintenance – but both do carry a cost. By utilizing predictive and preventive maintenance strategies, you can incur what your costs may be after a certain period of time. This gives you data to analyze for the future.
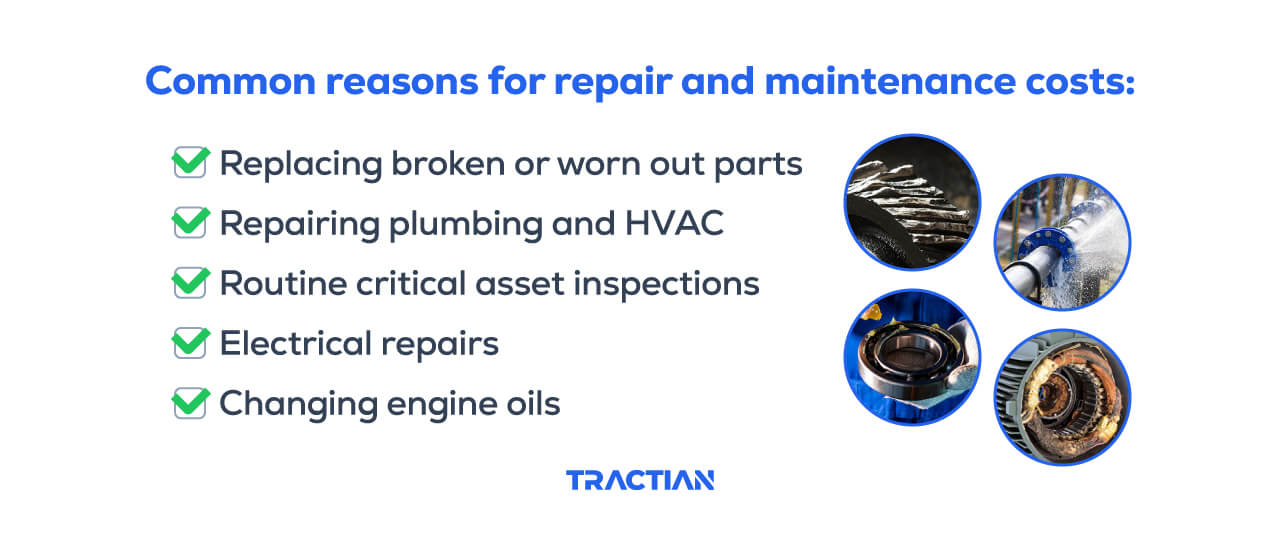
Proactive Maintenance vs Repair
So, how do maintainers keep up with routine maintenance of all of their assets? Simply put, they monitor machines and catch failures before they happen. One way to monitor every asset is with the TRACTIAN sensor, Smart Trac. It collects real-time data, making it available to maintenance teams on their phone, tablet, or computer, 24/7.
The sensor measures asset vibration and temperature, generating prescriptive insights about various failure modes and operation status. This data enables you to create a predictive maintenance strategy, optimized maintenance tasks, and work orders – keeping your production on track.
With the help of machine learning and artificial intelligence, we’ve created a condition monitoring system. It alerts you before repairs are necessary, helping companies create proactive maintenance strategies they can follow into the future.
Our fault detection technology has been patented by the USPTO – the world’s leading patenting institution. Our goal is to help maintenance teams optimize their strategies and reduce unplanned downtime, and this patent helps us do that.
To learn more about how Smart Trac can optimize your asset management, click here and speak with a specialist!