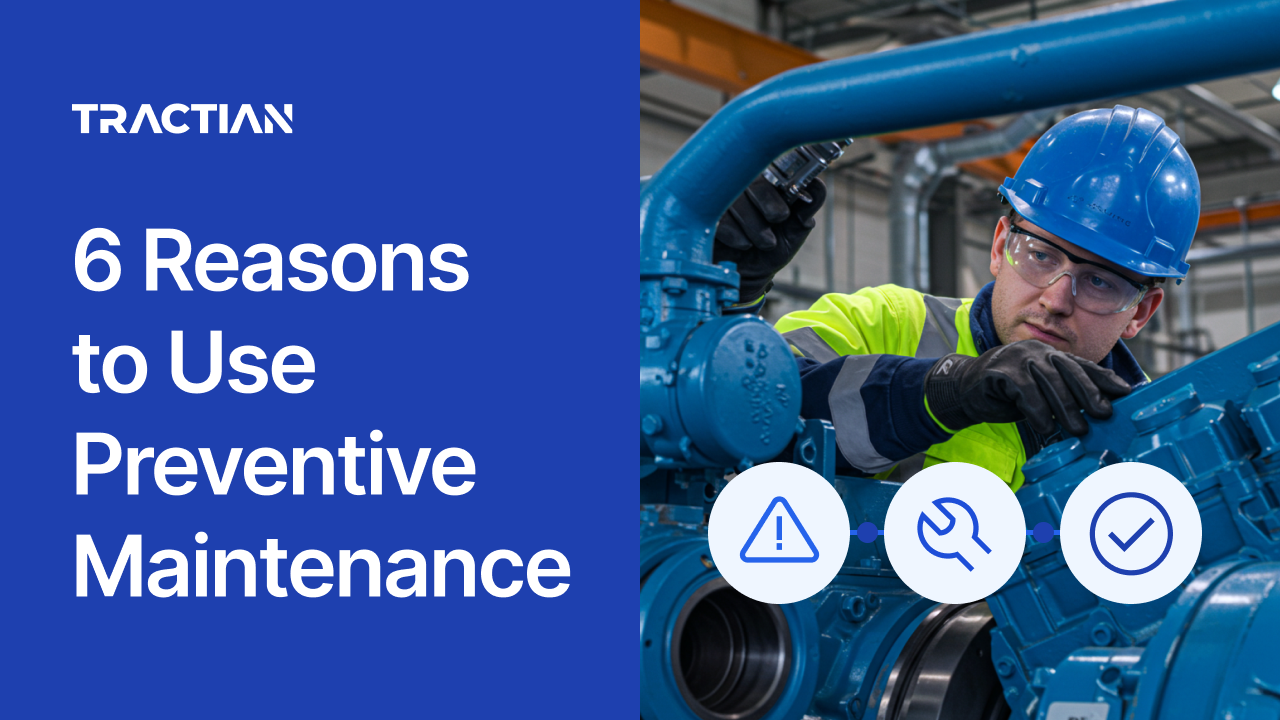
6 Reasons to Use Preventive Maintenance
Explore how preventive maintenance reduces downtime, cuts costs, and extends asset life to keep industrial operations safe, efficient, and compliant.
Keep readingLatest Articles
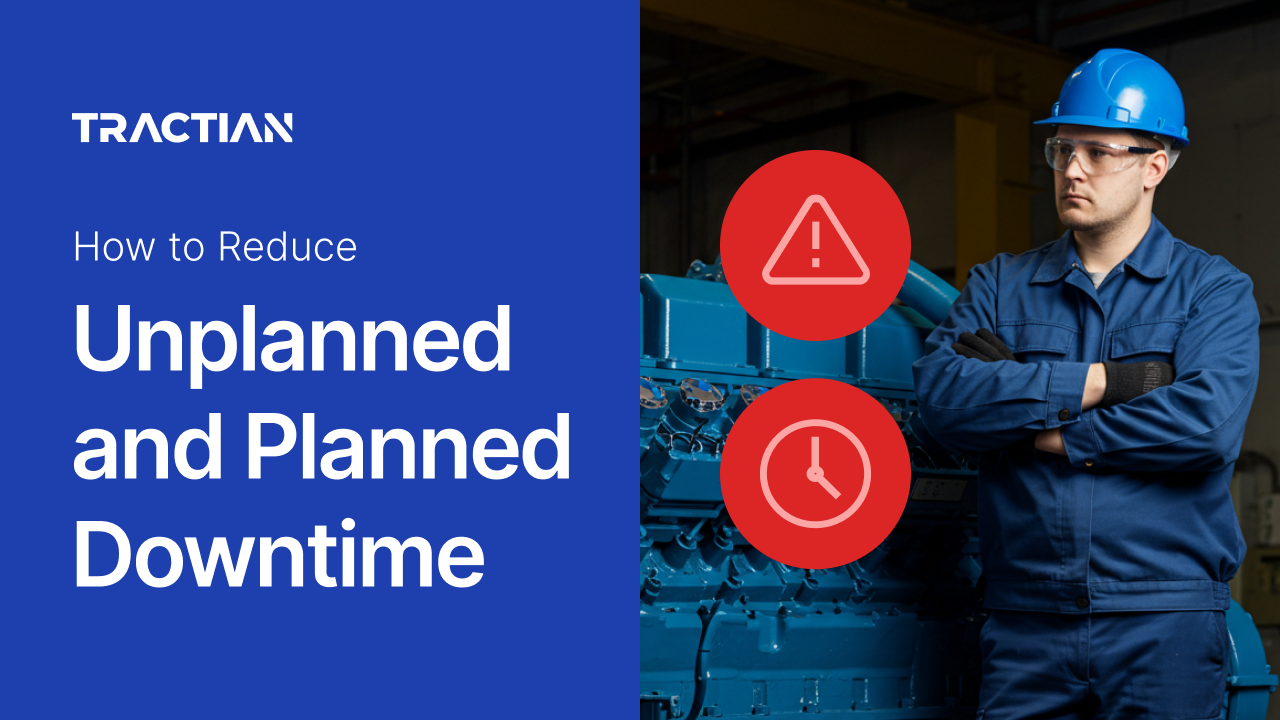
How to Reduce Unplanned and Planned Downtime
Learn key strategies to cut downtime, improve MTTR and OEE, and plan maintenance smarter. Discover how condition monitoring drives reliability.
Michael Smith
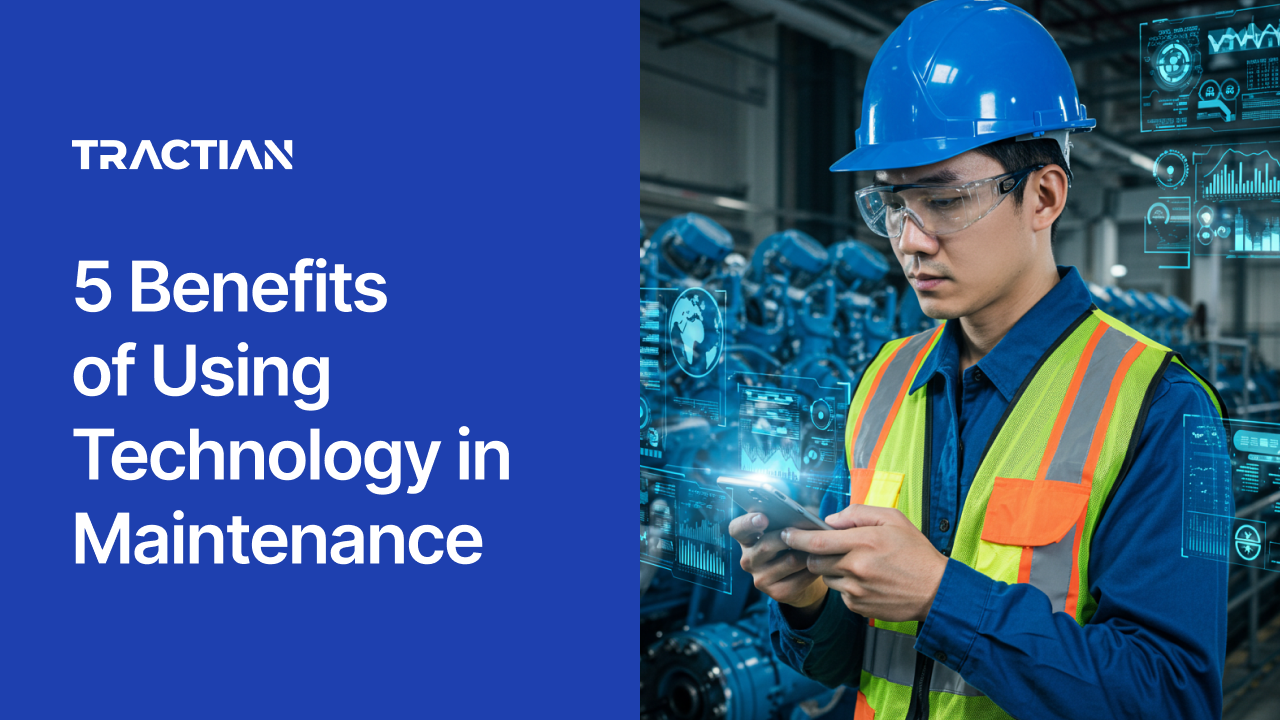
5 Benefits of Using Technology in Maintenance
Explore 5 practical benefits of using technology in maintenance, from reducing equipment failures to improving operational efficiency and reliability
Billy Cassano
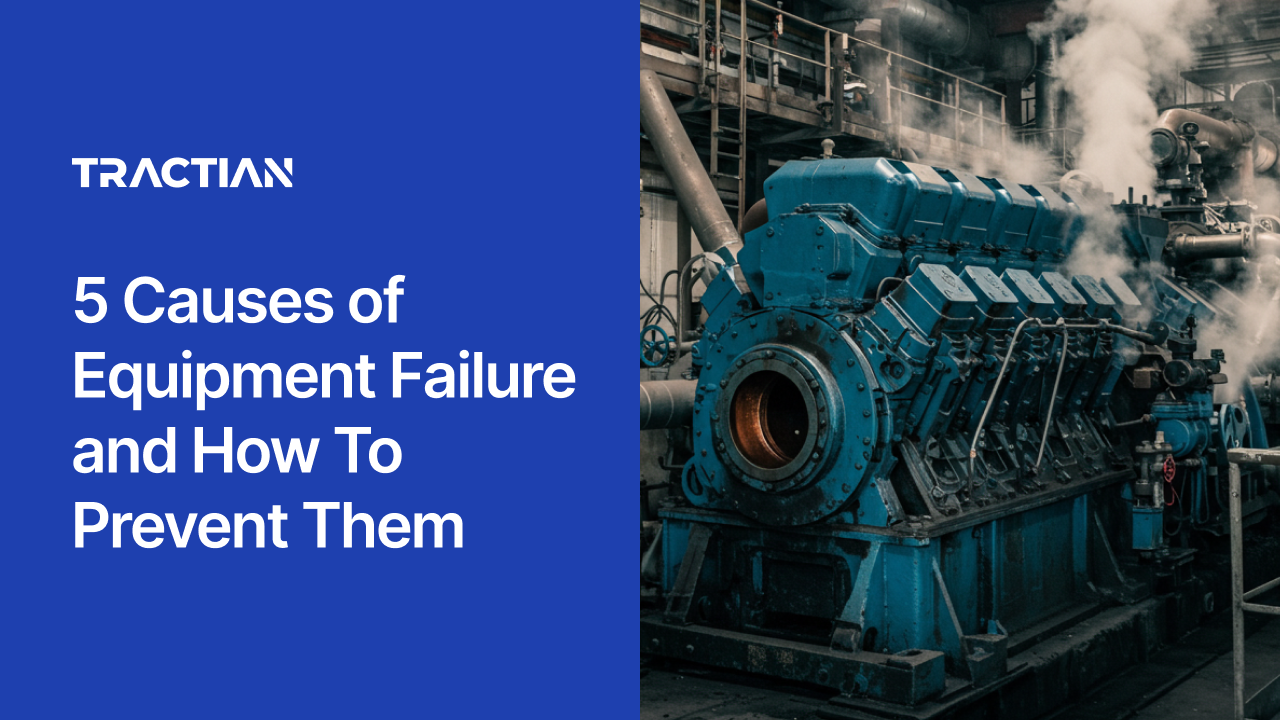
5 Causes of Equipment Failure and How To Prevent Them
Discover the 5 main causes of equipment failure and learn some practical strategies that can prevent downtime and boost operational efficiency.
Michael Smith
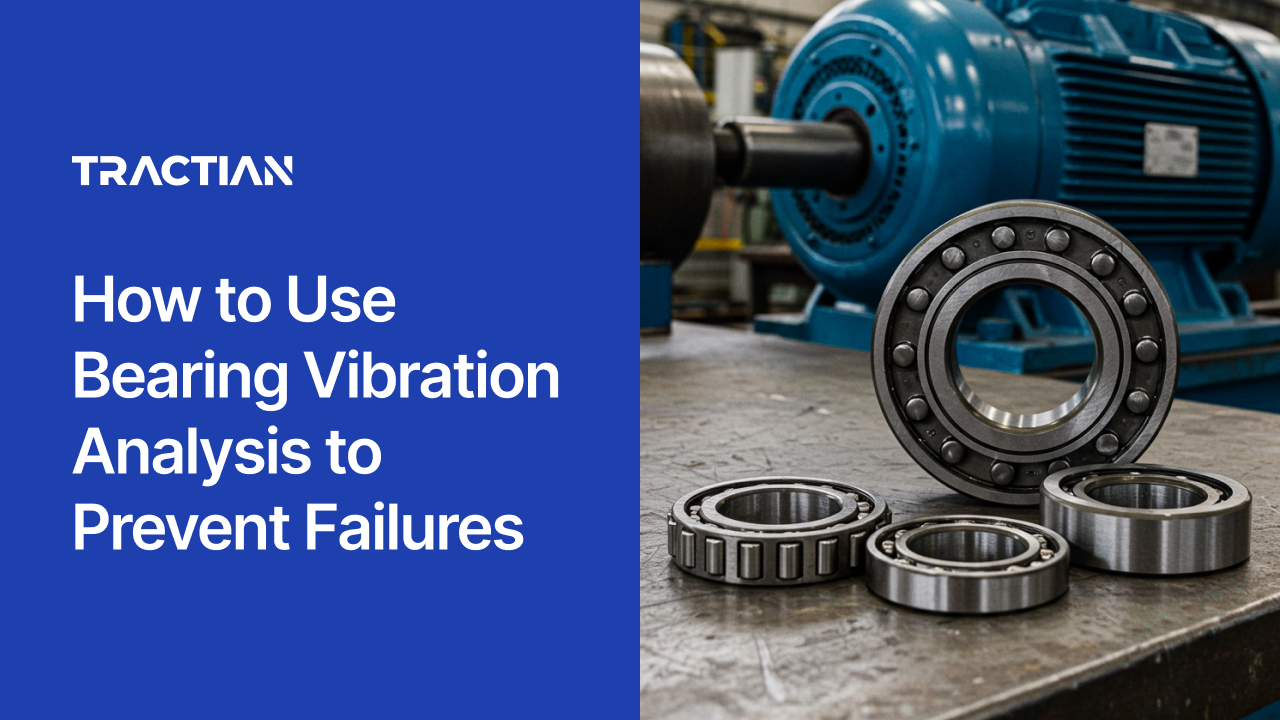
How to Use Bearing Vibration Analysis to Prevent Failures
Learn how bearing vibration analysis helps detect faults early, monitor wear, and prevent equipment failure using data-driven predictive strategies
Billy Cassano
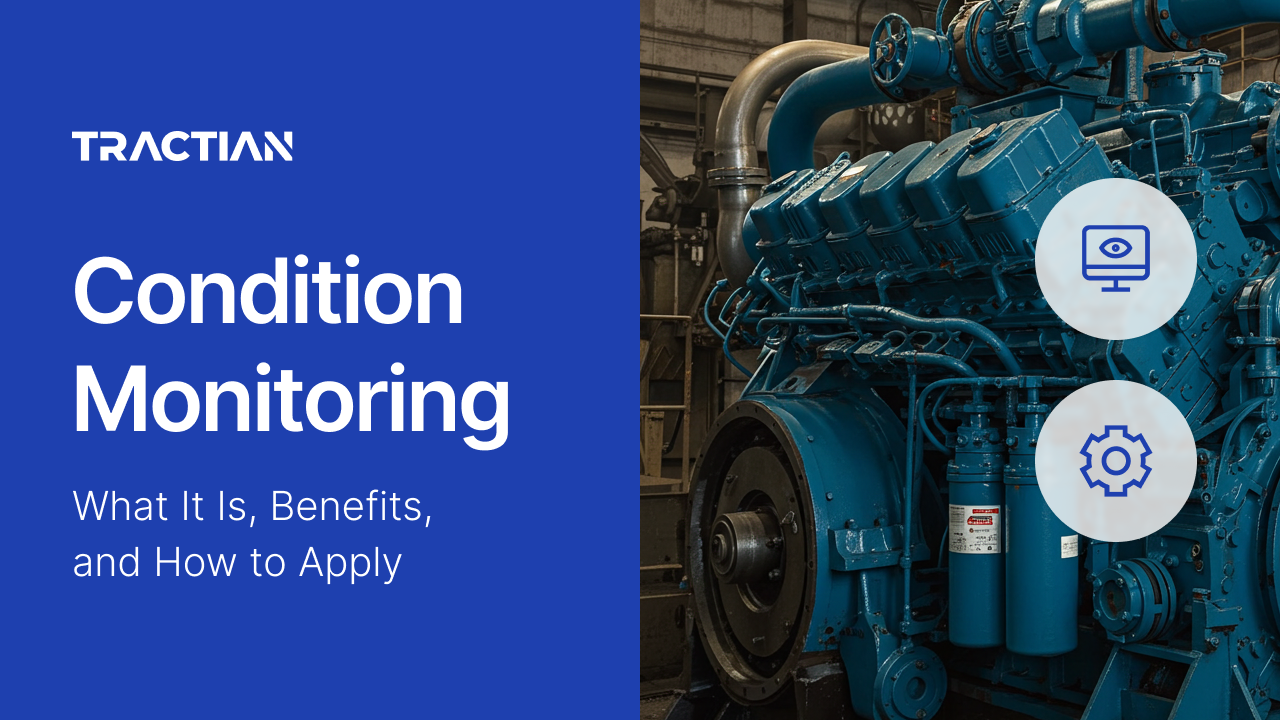
Condition Monitoring: What It Is, Benefits, and How to Apply
Learn how condition monitoring works, explore key techniques, and see how it helps prevent failures, reduce costs, and boost industrial reliability.
Michael Smith
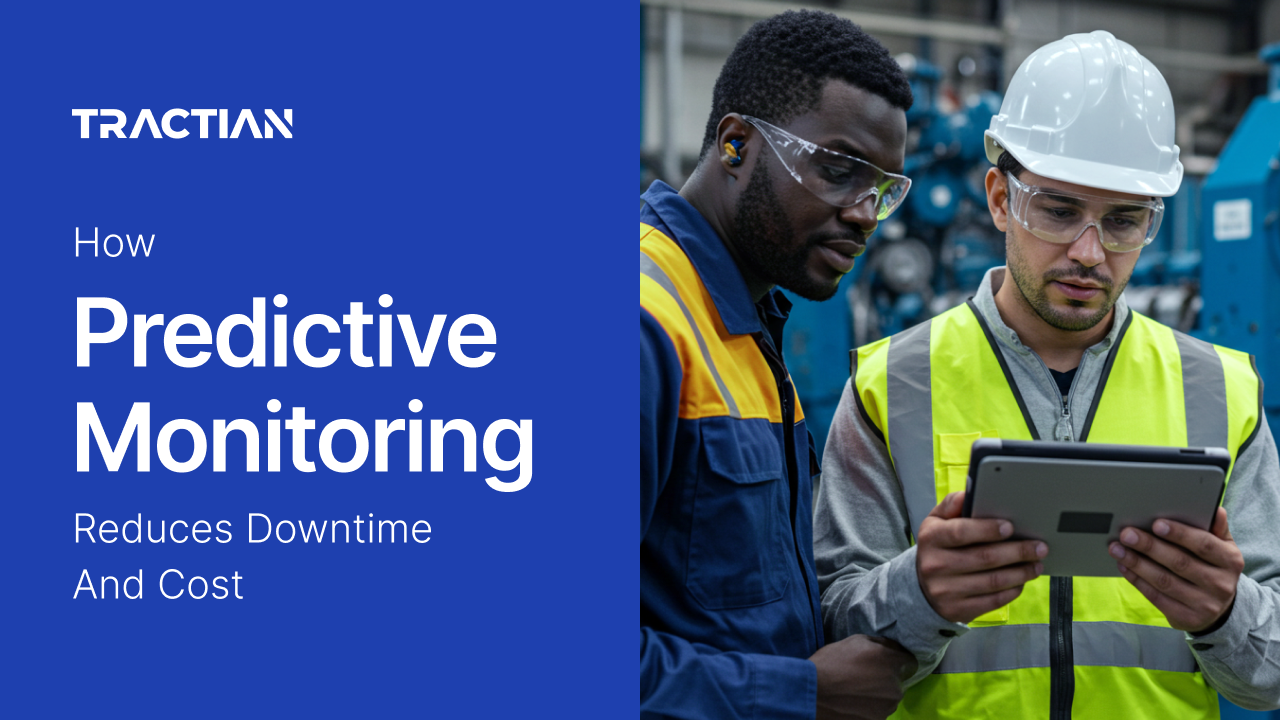
How Predictive Monitoring Reduces Downtime And Cost
Discover how predictive monitoring helps you reduce downtime, optimize maintenance, and extend asset life in process manufacturing environments.
Geraldo Signorini
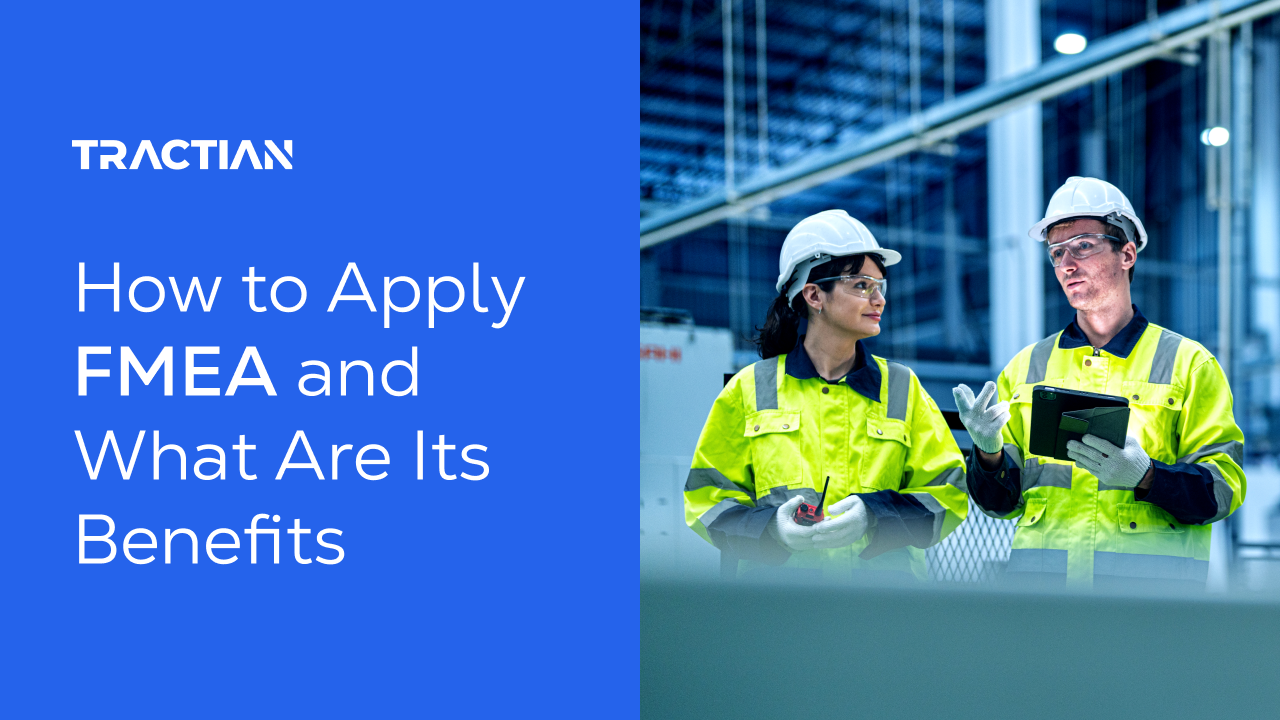
How to Apply FMEA and What Are Its Benefits
Master FMEA to reduce downtime, prevent costly failures, and improve reliability. This step-by-step guide shows you how to implement it effectively.
Billy Cassano
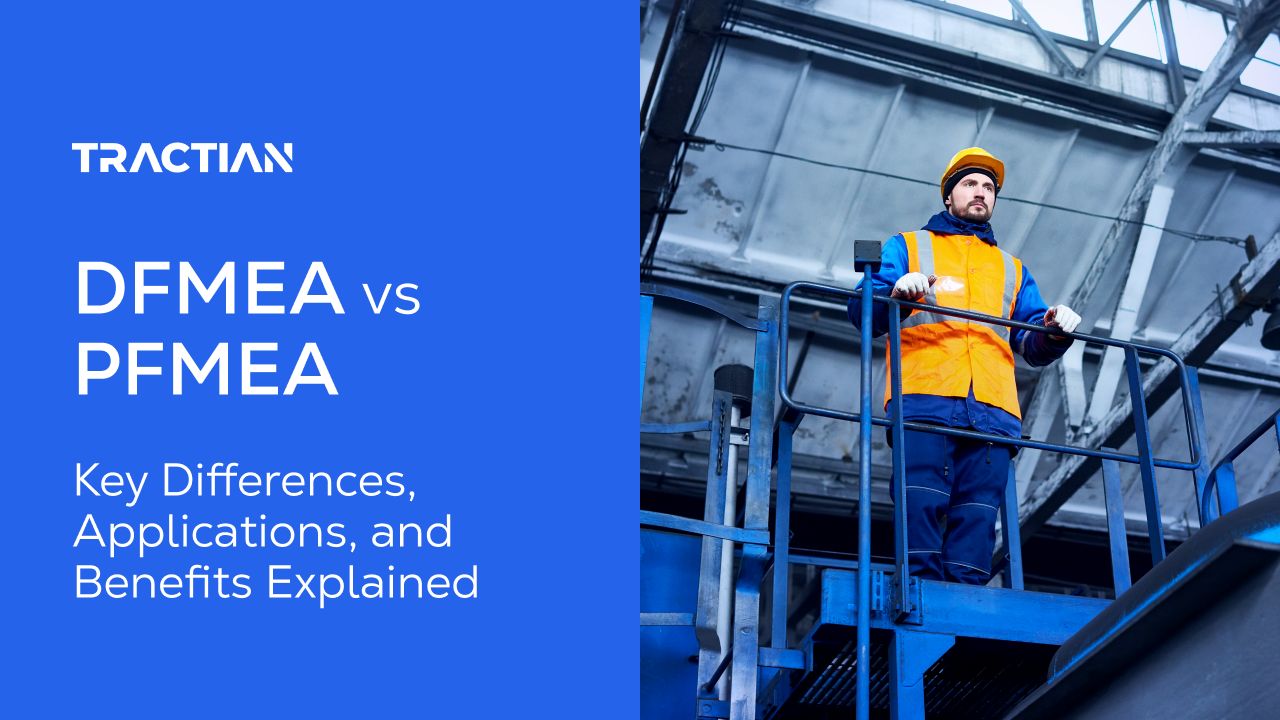
DFMEA vs PFMEA: Key Differences, Applications, and Benefits Explained
Manufacturers rely on Failure Mode and Effects Analysis (FMEA) to identify potential product and process failures. By assessing where and how things can go wrong, FMEA helps prevent costly mistakes before they happen. This methodology is split into two key categories: Design FMEA (DFMEA) and Process FMEA (PFMEA). DFMEA focuses on spotting failure modes during product design, while PFMEA addresses risks within the manufacturing process. Understanding and applying DFMEA and PFMEA can be the diff
Billy Cassano
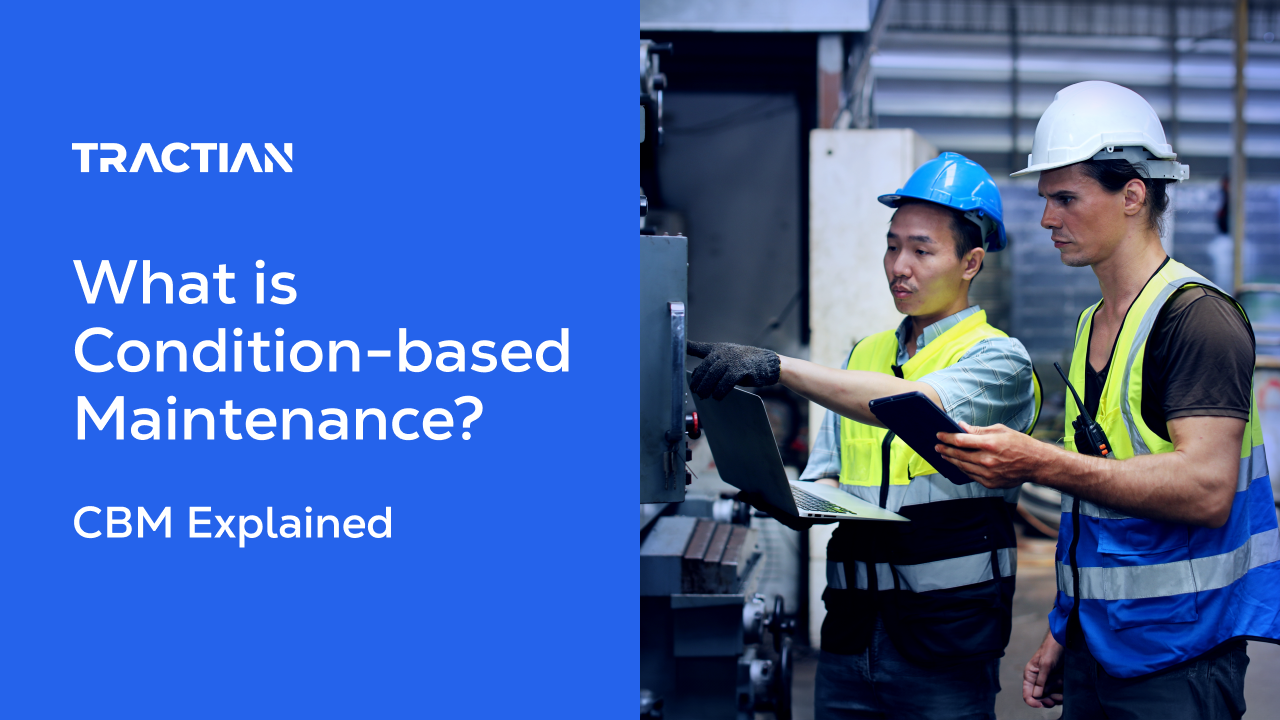
What is Condition-based Maintenance? CBM Explained
Condition-based maintenance (CBM) is a proactive approach where maintenance tasks are performed based on the actual condition of equipment rather than a fixed schedule. By using real-time data, CBM helps detect early signs of wear or potential failure, ensuring that maintenance is done only when necessary. This method transforms industries by reducing downtime, prolonging equipment lifespan, and optimizing resource use. Instead of reacting to breakdowns or sticking to rigid schedules, CBM allow
Billy Cassano
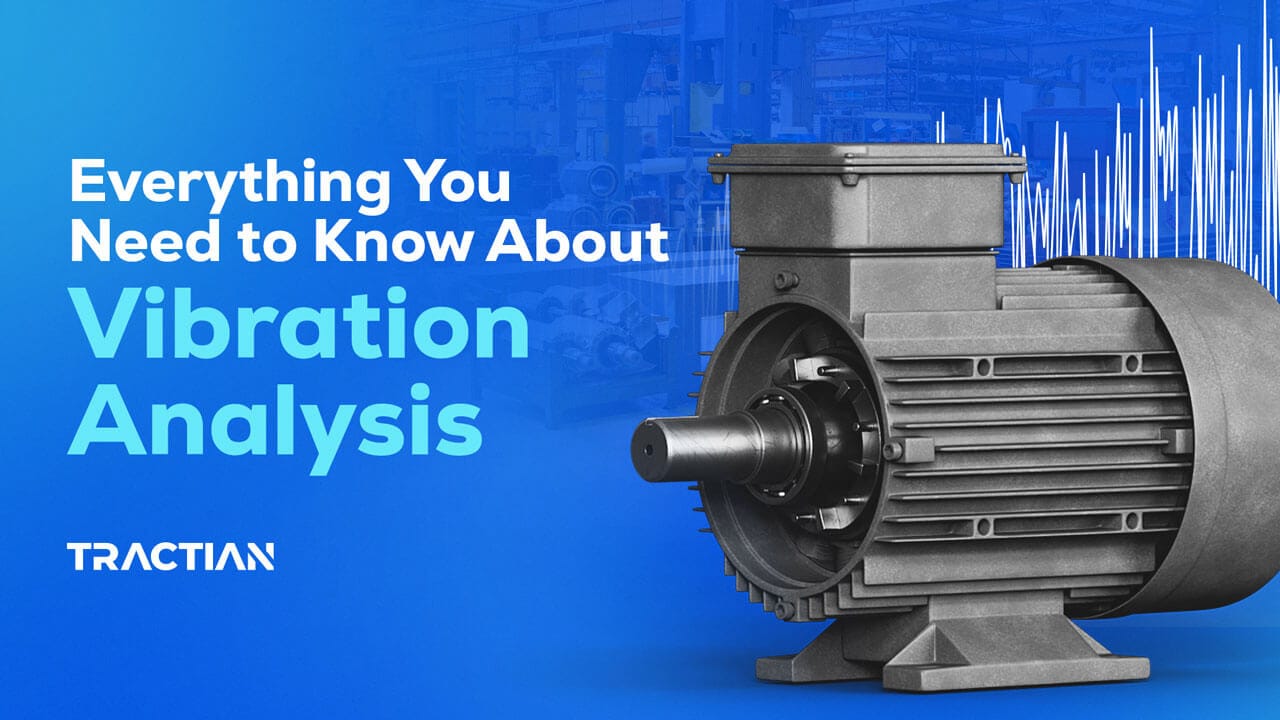
Vibration Analysis: The Complete Guide
The main goal of maintenance is simple: to improve performance and increase profits. In order to achieve these, teams must focus on tasks that increase asset reliability and availability – in turn reducing downtime. One of the most efficient ways to do this is by monitoring machine conditions. Condition monitoring lets us assess each asset, giving us crucial information about their behavior and current condition. The most common and efficient monitoring technique is vibration analysis (VA). I
João Granzotti
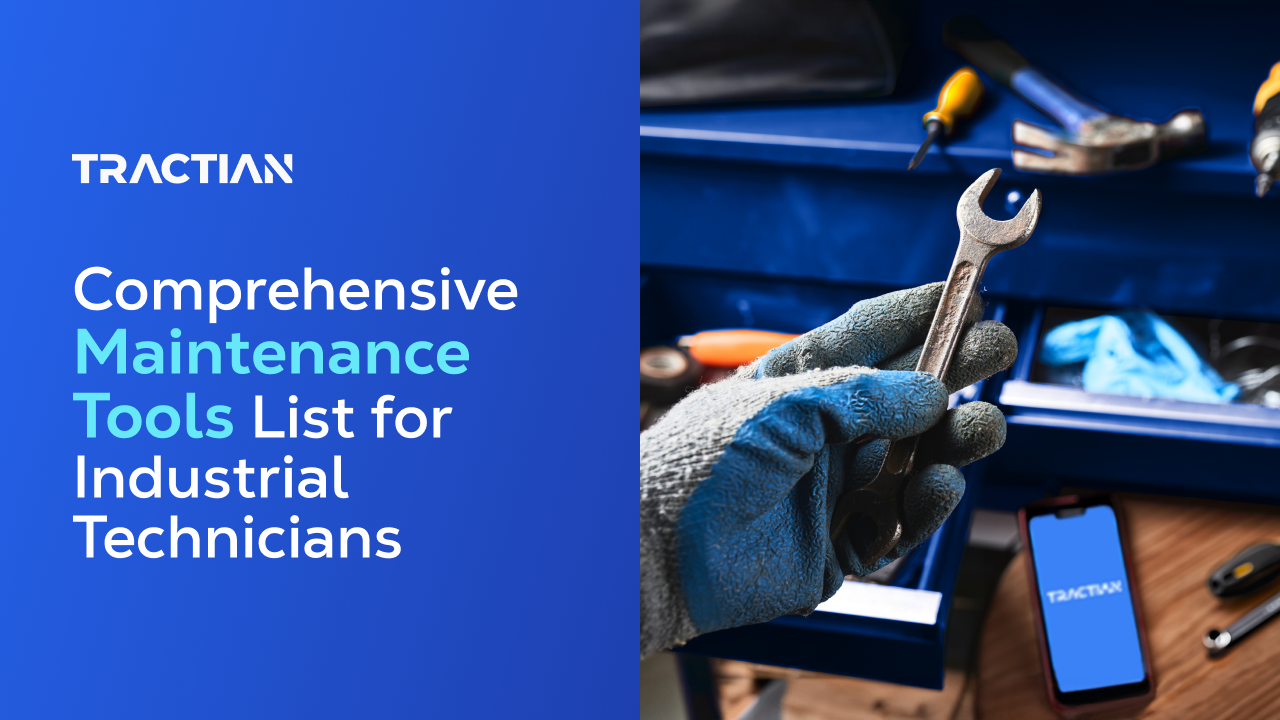
Essential Maintenance Tools: Boosting Industrial Efficiency
Have you ever wondered how crucial tools are to a maintenance technician’s success? In industrial operations, the effectiveness of maintenance work hinges significantly on the maintenance tools list. The deal is: maintenance is vital to prevent costly downtimes and extend equipment lifespan. But, without the right tools, even the most skilled technicians can struggle, leading to inefficiencies and potential failures. Conversely, equipped with a comprehensive toolkit, they can enhance productiv
Billy Cassano
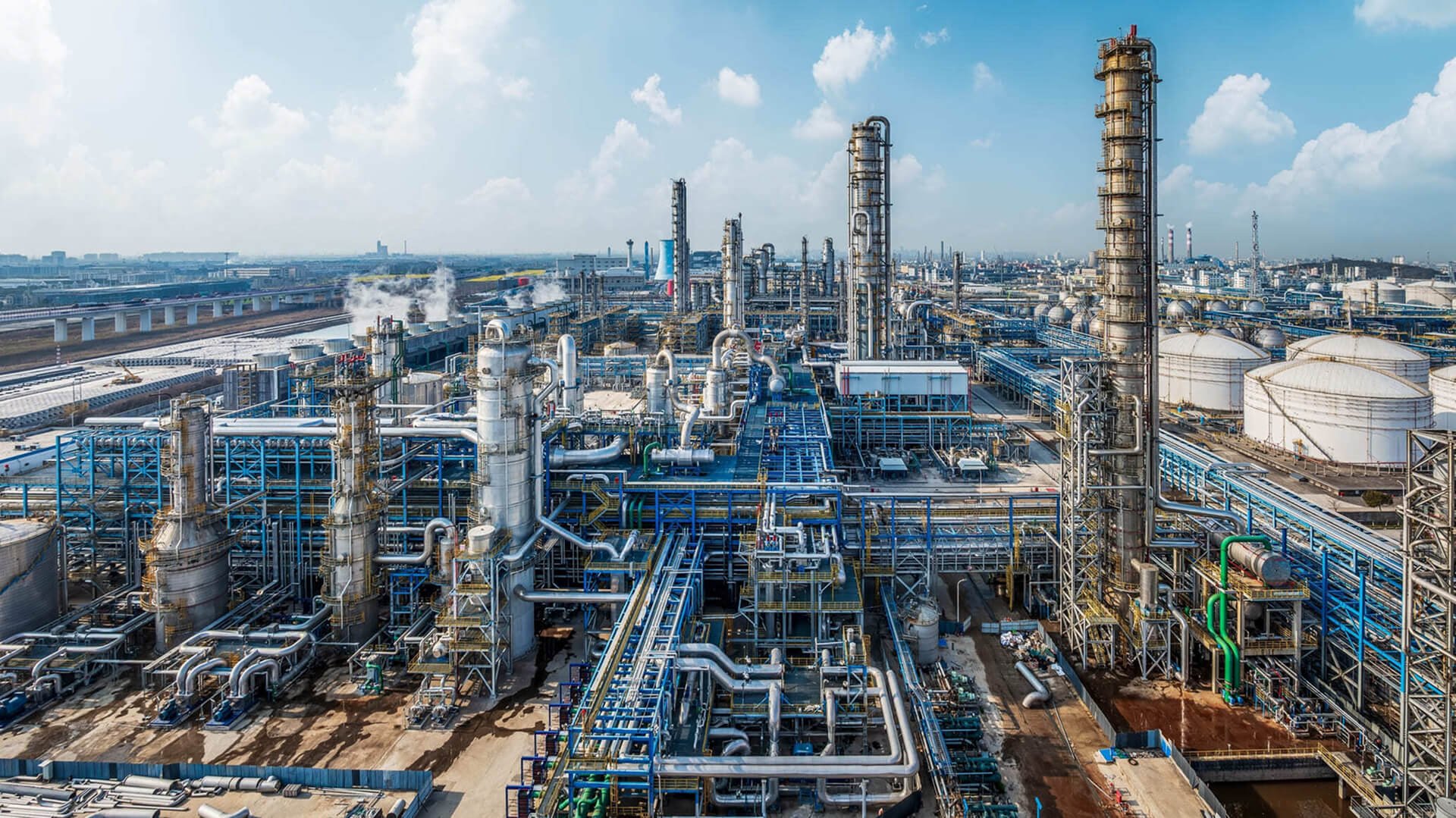
Elevating Predictive Maintenance with Advanced Vibration Sensors
The expression ‘time is money’ has never been more accurate than in today’s fast-paced industrial landscape, particularly when it comes to machinery maintenance and reliability. Unplanned downtime can lead to significant losses, making predictive maintenance an essential practice for modern manufacturing and production facilities. Predictive maintenance (PdM) is one of the more complex strategies when it comes to implementation, simply because minor performance changes are difficult to detect w
Billy Cassano
TRACTIAN Video Library
Discover our YouTube ChannelComprehensive free materials for your maintenance and reliability
Get free access to materials for increased productivity and an optimized maintenance routine.