You already know that in maintenance management, predictive maintenance is how we call the continuous monitoring of an asset.
This methodology is directly related to the prevention of potential failures that can affect the machine’s condition. And to prevent them, monitoring based on data collection is required.
There are two methods of asset monitoring in predictive maintenance: offline monitoring and online monitoring. The name may be similar, but they are very different from one another, each with its own specificities.
In offline predictive maintenance, we use manual collectors, which demand industry professionals to perform the collections.
In online monitoring, which has become increasingly used by companies that make part of the Industry 4.0 movement, the situation is quite different. IoT sensors when combined with Artificial Intelligence and installed in the machines, collect data automatically, 24 hours a day, every day.
One has to understand the two methods of asset monitoring to know which one to choose, since the decision contributes directly to a good asset management, with more assertive strategies that in turn impact maintenance costs and companies profitability.
That is why, in today’s article, we will explain the main differences between offline and online monitoring, as well as their pros and cons.
Offline Monitoring
In the offline monitoring method, the handheld vibration picker – also known as the vibration pen – is most commonly used by industry professionals.
Its measurements are made by a technician, who went to the asset making the overall vibration measurement for speed and/or displacement.
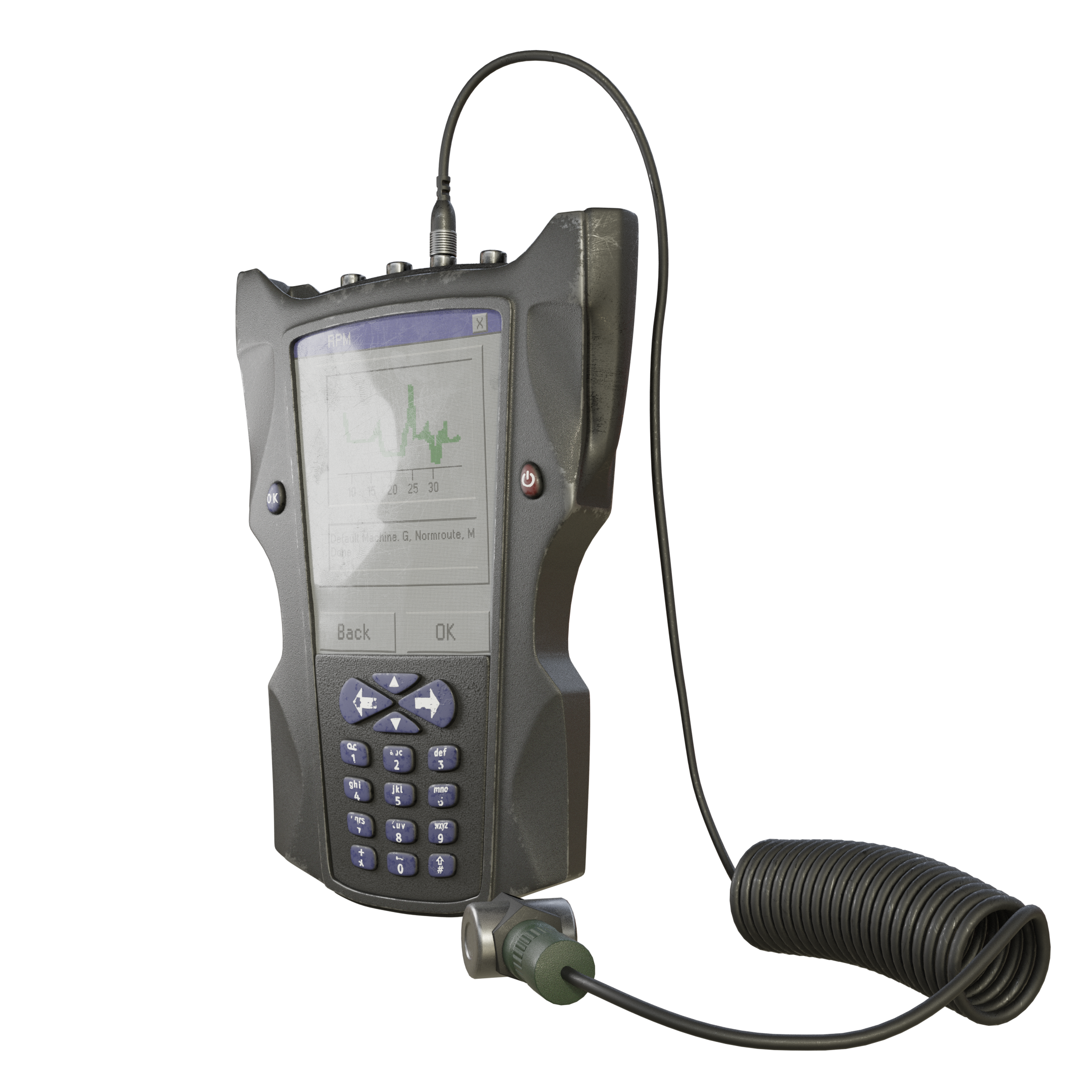
These collections happen at periods established in non-periodic inspection routes.
The whole process of collecting and downloading data requires a significant amount of time, not to mention that some assets may be difficult to access, depending on the industrial plant.
Here is an example to clarify the main differences between the two types of predictive maintenance: imagine a situation where a vibration measurement of a mill needs to be done.
If the maintenance manager opts for the offline method, it is necessary to prepare in advance the measurement material, which involves collector, sensors, cables and support – in addition to the safety materials (PPE) required to access the equipment.
In addition, in this type of collection, the technician must always be accompanied by a support team, since the situation presents risks.
The method is simple (although it requires a high level of expertise from the technician to analyze the collected data), but care must be taken and the measurement must be carefully planned.
After all, if the technician forgets some equipment or realizes that some data to be collected is missing, he will need to come and go from the mill several times.
This lack of preparation when performing offline predictive maintenance can cost a lot of time and effort for the team, keeping them from performing more important tasks.
Online Monitoring
On the other hand, in online asset monitoring, the IoT (Internet of Things) nature of the sensors attached to the machine allows data to be collected in real time, without requiring displacement, time or effort from the employees.
The maintainer does not have to worry about going to the asset, since the whole process is automated and remote. This includes the analysis of the collected data, which is also automatic and based on Artificial Intelligence.
An example of this type of predictive system is TRACTIAN, which offers the Smart Trac IoT sensors and the asset monitoring and management platform. Once the industry get the receivers, the team simply plug them into all the assets that will be monitored, since they have a magnetic base. They also have their own network (so they don’t depend on industrial Wi-Fi).
When accessing the platform for the first time, the maintenance manager enters the data of each asset and starts the sensors’ learning process. After that, they can start monitoring their machines through the computer, tablet, or cell phone, in a 100% remote and practical way.
With this, it is easier for the team to make strategic decisions for maintenance, since they no longer need to pre-set a date (sometimes randomly) to collect data.
The data is collected all the time by the sensors, stored in the cloud, and analyzed by the platform, which sends it to the maintainers in the form of insights about the machine’s condition. Thus, asset management is made easier and optimized.

The data collected by online asset monitoring systems can be divided into two types: vibration and temperature or asset specifications.
Vibration and temperature data is get from the moment the sensor is put on the machine and starts collecting information about the mechanical behavior and physical condition of the machine.
In addition to vibration analysis, machinery observability is provided, allowing you to control the data and fully understand the operating dynamics of all monitored assets.
The asset specifications are provided by the managers or responsible parties, and are intended to categorize the operation of the evaluated machine and facilitate its consultation and classification.
With this information, it is possible to identify from simple to more complex failures, such as: wear, misalignment, unbalancing, lack of lubrication, excessive vibration, downtime and several other problems that can appear in more than 30 types of rotating assets.
To learn more details about which assets the sensor monitors, read this article.
TRACTIAN online monitoring aims to mimic the behavior of the field analyst, but in an automated and continuous manner, increasing accuracy and decreasing the influence of randomness in the process.
Want to learn more about online predictive maintenance and how it can optimize production processes in your industry? Talk to our experts and schedule a demonstration.