One of the main goals of efficient management in maintenance is to keep asset availability and production reliability indicators at the highest levels. Equipment failure prevention becomes essential to maintain any company’s operational efficiency, as well as to increase the safety of factory floor workers.
In this article, we will explore strategies for reliability engineers who want to ensure that their most critical assets operate consistently and reliably, avoiding costly and dangerous shutdowns and unscheduled downtime.
The Importance of Reliability in Equipment Failure Prevention
Critical equipment failures not only disrupt the immediate machine operation, but can also trigger a series of problems in the production process.
The effects of these failures are extensive and diverse. Production lines can be affected, employee safety may be put at risk, and, in worst-case scenarios, environmental disasters can also happen.
The application of Reliability-Centered Maintenance (RCM) concepts within industries has therefore been recognized as the most efficient way to prevent failures and their potential effects.
RCM focuses on critical equipment or production bottlenecks, as failures in these assets can lead to greater damages compared to auxiliary equipment.
This empowers industries to achieve excellence in maintenance activities, increasing equipment availability and reducing costs associated with accidents, defects, repairs, and replacements.
Best maintenance practices like RCM shouldn’t be seen as a cost, but rather as an investment. Investing in the impact of preventive machine maintenance leads to sustainable production continuity.
Types of Maintenance: Preventive, Predictive, Reactive Maintenance, and more
Reliability Concepts in Industrial Production
The reliability of an item corresponds to its probability of performing its specified purpose adequately, for a given period of time and under predetermined environmental conditions.
In an industrial environment, low reliability has consequences that extend beyond simple repair costs or downtime. It impacts the company’s reputation, customer satisfaction, and even its competitive position in the market.
Imagine a factory experiencing frequent shutdowns due to critical equipment failures. This not only raises operating costs but also leads to delivery delays, potentially resulting in customer loss and ultimately, declining revenue.
When optimized, reliability serves as a guiding principle for maximizing productivity across the entire organization.
Reliability KPIs

Reliability Key Performance Indicators (KPIs), such as Mean Time Between Failures (MTBF) and Mean Time to Repair (MTTR), provide quantitative metrics that help measure the success of a preventive maintenance program.
MTBF represents the average amount of time elapsed between each failure for a repairable system, while MTTR is the average time it takes to repair a system or component after a failure. These indicators enable managers to make proactive adjustments to maintenance strategies. For instance, a high MTBF and a low MTTR are signs of a highly reliable and effective system.
Learn About the 8 Essential Maintenance KPIs
As a result, analyzing these metrics can drive decision-making regarding investments in reliable equipment, personnel training, and the implementation of technologies for failure prevention.
Operational Efficiency and Critical Equipment: The Role of the Industrial Engineering and Reliability Manager
Production process losses and costs can be attributed to lack of planning and problems in executing maintenance tasks.
Companies should strive to ensure the reliability and availability of their pieces of equipment through maintenance and asset management methods and systems.
In environments that heavily depend on critical equipment, the Industrial Engineering and Reliability Manager plays a vital role. They are responsible for creating, managing, and maintaining an environment where failure prevention goes through a system of data analysis, predictive modeling, and continuous feedback.
These managers serve as pillars of leadership and expertise in their industries when it comes to optimizing reliability engineering. They also play a pivotal role in reducing costs and minimizing unplanned downtime, always ensuring the maximum stability of the assets essential for production.
Leadership and Communication
The ability to lead teams and communicate strategies and procedures clearly is crucial for the success of any effective industrial maintenance program. But how to be a good leader?
Leadership involves setting goals, promoting a safety culture, developing the team, and making data-driven decisions.
On the other hand, effective communication, both internally and externally, is essential to ensure that maintenance strategies are understood and implemented in the best possible way.

Data Analysis for Decision Making and Equipment Failure Prevention
Maintenance managers need to analyze collected data on the performance and maintenance of critical equipment to identify trends and gain a stronger foundation for production-related, informed decisions.
This entails continuously monitoring KPIs, such as failure rates and mean time between failures, and comparing them to predetermined benchmarks and targets.
By pinpointing data patterns and anomalies, managers can take proactive steps to prevent major failures, schedule preventive measures at the right time, and allocate resources more effectively.

Proactive Risk Management
Proactive risk management is a key element for optimizing critical equipment and ensuring well-performed maintenance. It encompasses the identification of critical systems, the assessment of potential failures, and the control of risks associated with operating these equipment.
Reliability managers must be attentive to potential failure scenarios and their potential impacts. The development of contingency plans is a vital part of this process, enabling the team members to always be prepared to respond quickly to adverse situations.
Planning and Resource Allocation
Detailed planning and efficient resource allocation are crucial aspects for a maintenance manager in their role of leading preventive failure strategies.
Planning involves identifying the most critical assets, analyzing failure histories, and formulating maintenance practices that enhance industrial reliability while also using availability as an index of efficiency.
Resource allocation encompasses hiring skilled personnel, managing budgets for spare parts and critical equipment monitoring technologies, as well as investing in training.
Practical Strategies for Equipment Failure Prevention
There are a number of strategies that focus on helping industrial and shop floor teams prevent failures. We’ll go over some of them below.
Online Condition Monitoring
Online condition monitoring is a proactive approach in industrial maintenance made possible by the advancements of Industry 4.0, utilizing high-tech, cutting-edge sensors.
Through continuous monitoring of variables like vibration and temperature, interventions can be made before failures occur, contributing to the optimization of industrial machinery, increased efficiency, as well as cost reductions, and higher availability and reliability.
The effectiveness of this system relies on robust failure prevention data analysis, which interprets all data collections accurately.
Today, there are IoT solutions for availability that incorporate artificial intelligence for processing, integrating real-time data with historical records and even equipment manuals.
The sensors gather data on vibration, temperature, pressure, flow, and humidity, allowing for immediate detection of anomalies and instant alert notifications to maintenance teams.
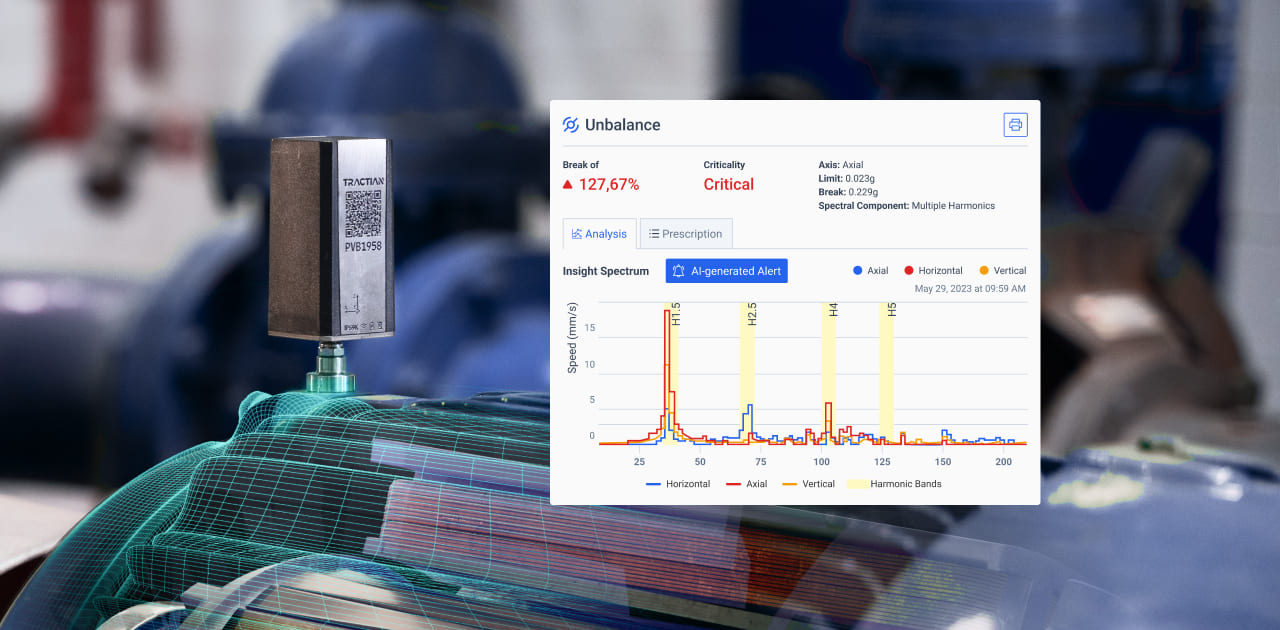
Continuous Improvement Initiative
Managers should constantly seek process optimization in maintenance. This involves reviewing existing practices based on data, failures, and feedback, as well as evaluating and selecting optimization and monitoring technologies deemed appropriate, such as IoT sensors and automated management systems.
Tracking KPIs is also a crucial practice for measuring the success of processes and directing improvements, ensuring that operations happen with maximum predictability, ultimately contributing to the organization’s success.
Team Training
A well-trained team is the first line of defense against failures in industrial machinery. Therefore, managers should ensure that all employees involved in the operation and maintenance of critical equipment are properly trained and up-to-date.
This will not only enhance the performance of your maintenance but also help your team identify issues more efficiently and accurately.
Inventory and Spare Parts Management
Inventory and spare parts management plays a critical role in preventing downtime. Maintaining a well-organized and strategically managed inventory of spare parts is essential to ensure that your industry is prepared to handle emergency situations promptly.
Immediate access to critical parts, which may need urgent replacement, also ensures that the essential assets of the plant remain up and running for as long as possible, generating savings and maintaining the operational efficiency of the company.
Skimping on material quality can lead to much higher costs in the long run, including the potential cost of equipment failure and production downtime.
Reliability and the Future of Industry
Reliability-Centered Maintenance is entering a new era thanks to the rapid advancement of Internet of Things (IoT) and Artificial Intelligence (AI) technologies.
In particular, predictive maintenance within industries is becoming increasingly viable and necessary. Instead of reacting to failures after they occur, predictive maintenance uses sensors, real-time data, and machine learning algorithms to predict failures before they happen.
Artificial Intelligence Assisted Maintenance, The Evolution of Reliability
This approach not only enhances system reliability but also optimizes the use of resources, as maintenance can be scheduled based on the actual needs of the equipment.
How Companies Improve Asset Reliability through Advanced Predictive Maintenance Approaches
Cibra, one of the largest fertilizer companies in America and partner of Omimex Resources, has provided high-quality agricultural products for over 28 years, and has implemented reliability-centered predictive maintenance approaches in its factory floors.
Through meticulous work in selecting critical systems, studying failure modes of critical assets and their respective effects, and adopting a hybrid maintenance approach combining online and offline condition monitoring techniques, several gains in efficiency and predictability were achieved:
- Reduction of equipment downtime from 8.9% to 3.2%
- Decrease in man-hours exposed to reactive or emergency practices
- Increased team productivity in scheduled activities
- More accurate, data-driven decision-making
The adoption of modern strategies for failure prevention has shifted from being an option to becoming an undeniable competitive necessity.
The bottom line is that with careful strategic planning, implementation of advanced monitoring technologies, and rigorous personnel training, it is possible not only to minimize risks but also to create an environment that is as efficient as it is safe.
If you want to follow in Cibra’s footsteps and increase the reliability of your assets through online condition monitoring, simply click this link.