Yara is the largest fertilizer manufacturer in the world – they have sales in 140 countries across the globe with over 200 warehouses, blending units, and bagging facilities in 60 of those countries. They pioneered the use of nitrogen-based systems in the industry, and continue to lead innovation in the crop nutrition sector.
With production sites on six continents, Yara quickly realized they were indispensable. After all, they’re responsible for fertilizing around 80% of the food chain. This relevance in the market made them realize they needed to invest in reliable maintenance solutions – ones that guarantee asset reliability and reduce unplanned downtime.
Negative unforeseen events can happen, and Yara wanted to do everything they could to prevent them – so they chose TRACTIAN condition monitoring sensors and Artificial Intelligence platform.
Starting the Project
In the beginning, the project only had five sensors. Since then it’s expanded exponentially, with hundreds of sensors monitoring assets in real time.
A corporate maintenance specialist at Yara says they started looking for predictive maintenance solutions with Artificial Intelligence (AI) in 2019. What they were looking for was a robust technology, one that could withstand the corrosive atmosphere of the fertilizer production process.
The team found what they wanted in Smart Trac, an IoT sensor integrated with a proprietary AI platform. Together, the sensor and platform learn machine behavior patterns and compare each data collection – about 300 per day – with collections from other similar assets around the world.
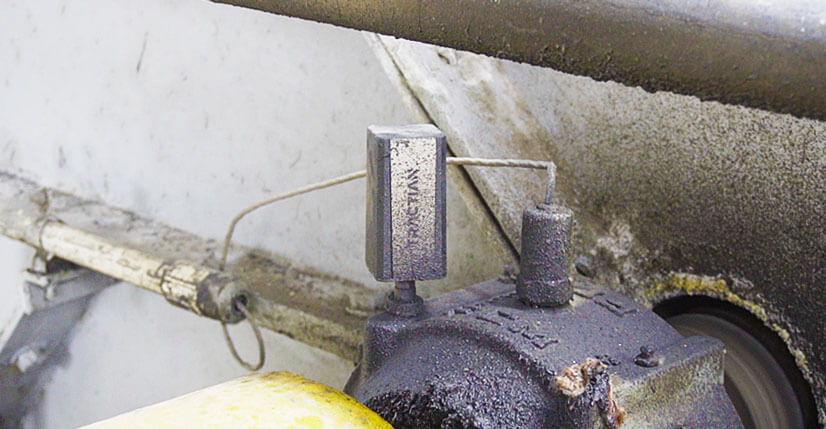
All this to be able to detect, diagnose, and prescribe potential failures automatically, making the Yara team aware of everything that is happening inside the machines involved in the production process.
At the beginning of the project, Yara’s maintenance supervisor had nothing but support to use the platform. Installation was extremely easy, giving him the ability to control all assets on whichever device he chooses – smartphone, tablet, or computer. Today, managers don’t have to take time to manually analyze data; the platform sends prescriptive insights at the slightest sign of an anomaly in the machine’s behavior.
“Now it has become easier to make decisions, and I can prepare to act more quickly, before causing a major consequence or impact.”
Because Yara is so dependent on harvest periods and rural producers, the deadline for product delivery is non-negotiable. Each customer wholly depends on fertilizer, so machines need to be continuously up and running.
Online condition monitoring guarantees Yara’s teams the predictability and reliability they’re looking for – making it an irreplaceable tool in the company’s production lines.
“We know that in the production of fertilizers, one day of downtime costs a lot of money for the company,” Yara’s maintenance supervisor said. During the 15 month project there were failures that – had they not been identified and solved in advance with the alerts and prescriptions of the platform – would have caused 24+ hour production stoppages and losses of around $69,408 each.

In this project so far, more than 4.1 million collections have been performed on over 200 machines. This resulted in more than 141 failures being identified in 15 months since starting the project.
Insights Making a Difference
Before Tractian monitoring, Yara was performing vibration monitoring with other systems. There are two main reasons the old system wasn’t performing: notifications weren’t being sent in real time, and the data that was collected wasn’t being interpreted to indicate the possible causes of the failure.
With TRACTIAN sensors, maintenance technicians first consult information, like vibration trends collected by the Smart Trac. Then they’re able to perform inspections directly on the assets. It’s both precise and non-invasive, allowing maintenance strategies to be more efficient. Yara’s maintenance is now more prescriptive than predictive.
“One of the great highlights about TRACTIAN is the ease and versatility in being able to adapt to any type of industry, even those that have their own peculiarities.”

Besides the prescriptive insights, another feature of the platform widely used by the entire Yara team are the dashboards.
The dashboard section gives you a broad view of all assets that are in operation and being monitored in real time by Smart Trac. Any operator can check which machines are in downtime, which are on alert, and the latest key insights – all on a single screen.
TRACTIAN solved a common industry problem – the difficulty of developing projects due to lack of data – and it became obsolete at Yara. With the sensors and software, the team monitors the history of the assets, reports and maintenance KPIs in seconds, allowing decision-making that will bring results.
Generally, maintainers keep track of the main indicators that are calculated by the platform. They can easily export this data, and use it to present to supervisors and managers.
Avoided Failures
The patented prescriptive maintenance technology identifies and diagnoses potential failures at the first symptoms, sending instructive insights to users.
An overload alert on the TRACTIAN platform was pointed out in one of Yara’s fertilizer production units.

Inside the gearmotor of a Redler (a critical piece of equipment) the elastic coupling grid fell off, causing the asset elements to come loose.
Redler’s are absolutely critical to the production process; when they stop, the entire production line is interrupted.
TRACTIAN sensors detected the overload and immediately the monitoring platform informed the maintenance team. This gave them a chance to intervene before the breakdown happened.
The estimated expense of this failure was $13,392.
There was another avoided failure in a blower, which is equally crucial to production. Any serious failure in a blower directly impacts the loading of trucks, possibly preventing the entire day’s production of fertilizers.
The blower in question was in a restricted part of the plant, making it even more difficult to inspect the machine. Thankfully, the team used online condition monitoring to identify a looseness in the bearing, making sure daily production wasn’t halted. Had this failure not been avoided, there would’ve been 24 hours of production downtime and a loss of $68,920.

Management 4.0 – The Change Generated by Online Condition Monitoring
Yara places maintenance at the top of its strategy, with the goal of delivering quality products to the consumer.
Deciding which assets to monitor is strategic, and many maintenance teams start with the most critical equipment.
For Yara’s maintenance analyst, the TRACTIAN system works as the “eyes of maintenance”.
He says that although the manual inspection plans were robust, they also had large intervals between them. Now, with real-time prescriptive monitoring, they can inspect operating assets and be alerted in real time of flaws that are being presented.
“There are days that I use the platform a few hours a day. If we don’t monitor all the time, we won’t even know about many changes in operations. It’s a good thing that TRACTIAN registers for us.”
Yara’s success with the TRACTIAN solution wasn’t just a fluke – your industry can benefit from prescriptive condition monitoring too. Implement the right maintenance strategies and systems to see an increase in equipment life and to multiply maintenance results. Learn more about the system and schedule a free demo.